Printing basic concepts
Printing
The use of dyes or pigments in the textile printed with a certain dye fastness of the flower pattern processing.
The classification of printed matter
The object of printing is mainly fabric and yarn. The former pattern directly attached to the fabric, so the pattern is clearer. The latter is the pattern will be printed on the parallel arrangement of the yarn collection, after weaving the fabric to produce a hazy style pattern effect.
The difference between printing and dyeing
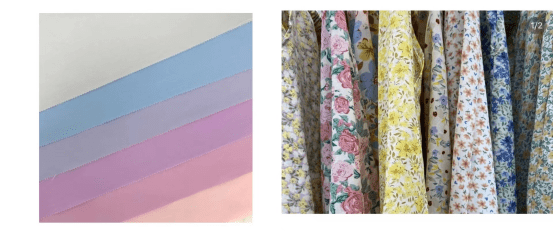
1. Dyeing is to dye the dye evenly on the textile, to get a single color. Printing is printed on the same textile with one or more colors of pattern patterns, in fact, is a local dyeing.
2. Dyeing is the preparation of dyestuff and dyeing on the fabric through water as a medium. Printing but with the help of slurry dyeing medium, the dyes or pigments into printing slurry printed with the fabric, after drying, in accordance with the nature of the dye or color vaporization, color development and other subsequent processing, so that it is dyed or fixed in the fiber, and finally by soap washing, washing, remove the floating color and color slurry in the paint, chemicals, etc.
Printing pre-treatment
Similar to the dyeing process, the fabric must be pre-treated before printing, has obtained good wettability, in order to make the color paste evenly into the fiber. Polyester and other malleable fabrics sometimes need to be heat-set, in order to reduce the printing process of shrinkage deformation.
The method of printing
According to the printing process, there are direct printing, anti-dye printing and dyeing printing; according to the printing equipment is mainly roller printing, screen printing and transfer printing, etc. From the printing method, there are manual printing and mechanical printing. Mechanical printing mainly screen printing, roller printing, transfer printing and spray printing, the first two applications are more common
Printing methods and their characteristics
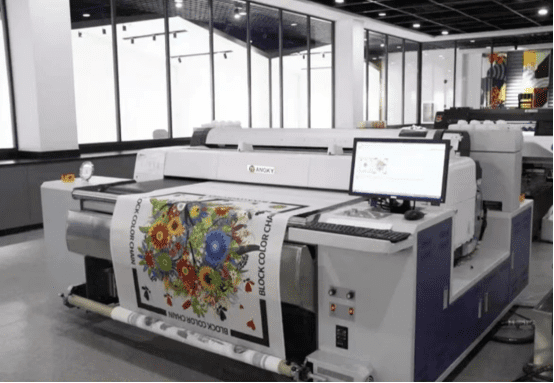
Fabric printing according to printing equipment can be divided into: screen printing, roller printing, heat transfer printing, wood stencil printing, hollow type printing, tie-dye, batik, splash printing, hand-painted printing, etc.. Among them, there are two printing methods of commercial importance: screen printing and roller printing. The third method is heat transfer printing, which is relatively less important. Other printing methods that are rarely used in textile production are traditional wood stencil printing, wax valance (i.e. wax-proof) printing, yarn tie-dye fabric printing and dye proof printing. Many textile printing plants mostly use screen printing method and roller printing method to print fabrics. Most of the heat transfer printing carried out by the printing factory is also printed with this method.
Traditional printing technology
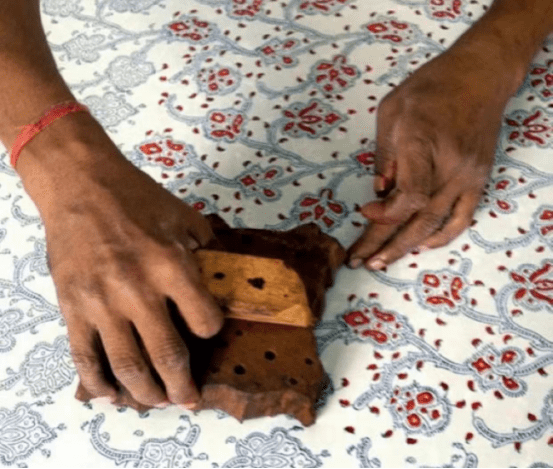
1. wood stencil printing: in the convex grain wood on the fabric printing method.
2 hollow type printing: mainly divided into three categories: hollow type version of white paste anti-dye indigo printing, hollow type version of white paste anti-dye paste printing and hollow type version of color paste direct printing.
3. tie-dye printing: in the embryonic cloth using string bundle, sewn into a certain fold and then tied firmly, dyed to obtain the pattern.
4. batik printing: in cotton, silk and other fabrics need to show the pattern of parts of the coating, and then dip-dyeing or brush-dyeing, so that the wax-free parts of the fabric dyed color, and then in boiling water or a specific solvent to remove the wax stains, so that the fabric now pattern.
5 . Dyeing printing: Acid dyes are used to splash or brush colors on silk fabrics at will, and then salt is sprinkled on the screen before it dries, with the neutralization of salt and acid dyes, forming a natural flow of abstract patterns on silk. Commonly used in silk.
6 . hand-painted printing: directly dipped in the dye solution with a pen on the fabric to depict the pattern of a printing method.
Screen Printing
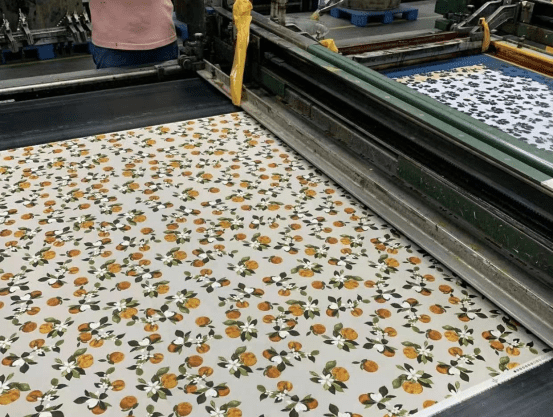
Screen printing includes the preparation of the printing screen, printing screen (used for printing process screen was once made of fine silk, the process is called screen printing by taut on a wooden or metal frame with a fine mesh of nylon, polyester or wire fabric made. The screen fabric should be coated with an opaque non-porous film. Where there is a pattern, the opaque film is removed, leaving a fine mesh stencil, and this area is the part where the pattern will be printed. Most commercial screen fabrics are first coated with a photosensitive film, and then the pattern area of the film by the photographic method to remove the pattern and show the pattern. The screen is placed on the fabric to be printed. The printing paste is poured into the printing frame and forced through the mesh of the screen by a squeegee (a tool similar to a wiper on a car windshield). Each color in the printing pattern requires a separate screen, the purpose is to print a different color.
Hand Screen Printing
Hand screen printing is produced commercially on long panels (panels up to 60 yards long). The printed roll of fabric is laid smoothly on the board, and the surface of the board is pre-coated with a small amount of adhesive material. The printers then move the frame by hand continuously along the entire board, printing one frame at a time, until the fabric is completely printed. Each frame corresponds to a printing color. The production speed of this method is 50-90 yards per hour. Commercial hand screen printing is also used in large quantities to print cut pieces of clothing. In the piece printing process, the garment making process and the printing process are aligned together.
Customized or unique designs are printed on the garment before the pieces are sewn together. Because hand screen printing can produce large mesh frames for large patterns, fabrics such as beach towels, novelty printed aprons, draperies and shower curtains can also be printed by this printing method. Hand screen printing is also used to print limited edition, highly fashionable women’s garments and to print small quantities of products for market exploration.
Automatic Screen Printing
Automatic screen printing (or flat screen printing) is the same as hand screening except that the process is automated and therefore faster. The printed fabric is conveyed through a wide rubber belt to the screen, rather than being placed on a long table (as in manual screen printing). Like manual screen printing, automatic screen printing is an intermittent rather than a continuous process.
In this process, the fabric moved to the screen below, and then stop, the screen scraper for scraping (automatic scraping nail), scraping after the print, the fabric continues to move to the next frame below, production speed of about 500 yards per hour. Automatic screen printing can only be used for the whole roll of fabric, cut pieces of clothing generally do not use this method of printing. As a commercial production process, automatic screen printing (referring to flat screen printing) production is declining because of the preference for more productive circular screen printing.
Screen Printing
Screen printing differs from other screen printing methods in several important ways. Screen printing and in the next section will describe the roller printing, the same continuous process, the printed fabric through the wide rubber belt is transported to the continuous movement of the cylinder under the screen. Screen printing is the fastest of all, with production speeds greater than 3,500 yards per hour. Seamless perforated metal or plastic screens are used. The largest wire mesh circumference is greater than 40 inches, so the largest flower return size is also greater than 40 inches. Screen printers with more than 20 sets of colors have also been produced, and this printing method is slowly replacing roller printing.
Cylinder printing
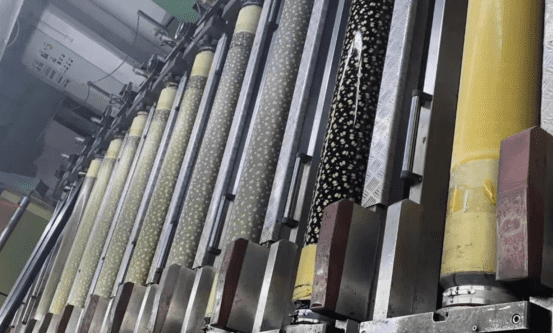
Roller printing is like newspaper printing, is a high-speed process that can produce more than 6,000 yards of printed fabric per hour, this method is also called mechanical printing, roller printing, the pattern through the engraved copper roller (or rollers) printed on the fabric. The copper roller can be carved out of the closely spaced very fine grain, and thus can print a very detailed, soft pattern. For example, the fine, dense Pelizli swirl pattern printing is printed by roller printing a class of patterns.
Cylinder engraving
Should be identical with the design of the pattern designer’s design, each color each need a carving roller Jane (in the textile industry special printing process, five-roller printing, six-roller printing, etc. commonly used to indicate five sets of colors or six sets of colors roller printing. Roller printing is the least used method of mass production of printing, production continues to decline each year. If the production of each pattern is not a very large batch, this method is not economic.
Heat transfer printing
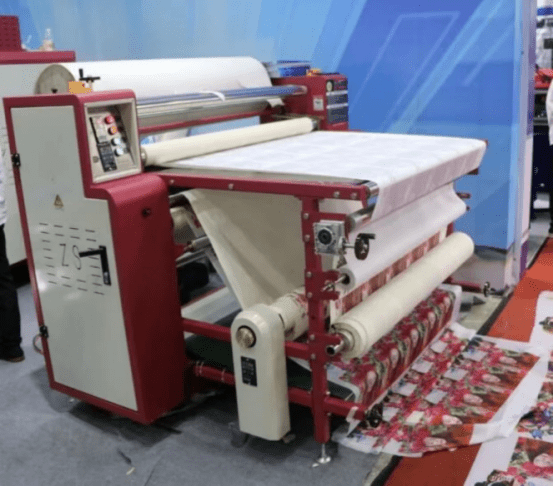
The principle of heat transfer printing is somewhat similar to the transfer printing method. In heat transfer printing, the pattern is first printed on paper with disperse dyes and printing ink, and then the printing paper (also called transfer paper) is stored for use in textile printing plants. When the fabric is printed, it passes through the heat transfer printing machine so that the transfer paper and the unprinted side are attached together and passed through the machine at about 210°C (400T). At such a high temperature, the dye on the transfer paper sublimates and is transferred to the fabric, completing the printing process without further processing. The process is relatively simple and does not require the expertise necessary for roller printing or screen printing. Disperse dyes are the only dyes that can sublimate, and in a sense are the only dyes that can be heat transferred, so the process can only be used on fabrics made up of fibers that have an affinity for such dyes, including acetate, acrylonitrile, polyamide (nylon) and polyester.
Spray Printing
Jet printing is the process of spraying small droplets of dye and holding them in precise positions on the fabric. The nozzles used to spray the dye and pattern formation can be computer-controlled, and complex patterns and precise pattern cycles can be obtained. Jet printing eliminates the delays and cost increases caused by carving rollers and making screens, which is a competitive advantage in the fast-changing textile market.
Jet printing systems are flexible and fast, moving quickly from one pattern to another. Printed fabrics are not subject to tension (i.e., the pattern is not distorted by stretching) and the surface of the fabric is not rolled, thus eliminating potential problems such as fabric pilling or linting. However, this process cannot print fine patterns, and the outline of the pattern is blurred. Now jet printing method is almost always used for carpet printing, is not an important process of clothing textile printing. However, with the research and development of mechanical and electronic control technology, this situation may change.
The basic way of printing
Printing by printing equipment can be divided into direct printing, dyeing printing and anti-dyeing printing.
1.Direct printing
direct printing is a direct printing on white fabric or in the pre-dyed fabric. The latter is called cover printing. Of course, the color of the print pattern is much darker than the dyed base color. A large number of common printing method is direct printing. If the fabric base color is white or mostly white, and print pattern from the back to look lighter than the front color, then we can determine that this is direct printing fabric (note: because the printing color paste penetration is very strong, so the light fabric can not be judged by this method). If the fabric bottom color front and back of the same shade (due to the pee dyeing), and print pattern than the bottom color is much darker, then this is the cover printing fabric.
2.plucking dye printing
plucking dye printing through two steps, the first step, the fabric is dyed into a single color, the second step, the pattern printed on the fabric. The second step in the printing color paste contains a strong bleaching agent that can destroy the underlying dye, so this method can produce a blue background white polka dot pattern of flower cloth, this process is called plucking white.
When the bleaching agent and will not react with its dyes mixed in the same color paste (reduction dyes belong to this type), color pulling printing can be carried out. Therefore, when a suitable yellow dye (such as reduction dyes) and color bleach mixed together, you can print a yellow dot pattern on a blue background fabric.
Because the base color of the plucked dye printing is first dyed in the way of dyeing, if the base color is printed on the ground than the full print, the color of the base color is rich and much darker. This is the main purpose of the use of dyeing printing. Pull dyeing printing fabric can be printed by roller printing and screen printing, but not by heat transfer printing. Because compared with direct printing, plucking printing fabric production costs are very high, but also must be very careful and accurate control of the use of the required reducing agent. Using this way of printing fabrics, sales are better, the price grade is higher. Sometimes, the reducing agent used in this process can cause damage or destruction of the fabric at the printing pattern. If the color of the base color on both sides of the fabric is the same (because it is dyed), and the pattern is white or a different color from the base color, it can be confirmed as a plucked printed fabric.
3.Anti-dye printing
Anti-dye printing includes a two-stage process:
(1) printing on white fabric can stop or prevent the dye penetration into the fabric chemical or wax resin;
(2) dyeing the fabric. The purpose is to dye the base color so as to set off the white pattern. Note that the result is the same as the plucked printed fabric, however, the method to achieve this result is the opposite of plucked printing. Dye proof printing method is not commonly used, and is usually used when the base color cannot be dyed. Compared to the mass production base, most of the anti-dye printing is achieved through methods such as handcraft or hand printing (such as wax anti printing). Because the same printing effect is produced by plucking printing and anti-dyeing printing, it is often not distinguishable by visual observation.
4.Paint printing
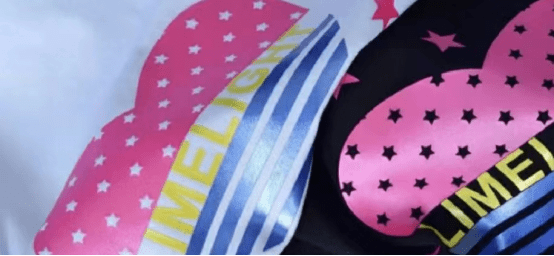
The use of paint rather than dyes to produce printed fabric has become so widespread that it has begun to be treated as a separate printing method. Paint printing is direct printing with paint, the process is usually called dry printing, to distinguish it from wet printing (or dye printing). By comparing the hardness difference between printed and unprinted areas on the same piece of fabric, paint printing and dye printing can be distinguished. Paint printing area than the unprinted area feel a little harder, perhaps a little thicker. If the fabric is printed with dye, the printed part and the unprinted part will not have obvious hardness difference.
Dark paint printing than light or light colors, it is likely to feel harder, more lack of flexibility. When inspecting a piece of fabric with paint printing, be sure to check all colors, because in the same piece of fabric, may contain both dye and paint. White paint is also used for printing, and this factor should not be overlooked. Paint printing is the most inexpensive form of printing in print production because paint is relatively simple to print and requires the least amount of process, usually without steam and wash.
Paints are available in bright, rich colors and can be used on all textile fibers. Their light fastness and dry-cleaning fastness are good to excellent, making them widely used for decorative fabrics, curtain fabrics and garment fabrics that require dry-cleaning. In addition, the coatings hardly produce large color differences on different batches of fabrics, and the coverage of the base color during overprinting is also very good.
5.Special printing
The basic way of printing (as mentioned before) is printed on the fabric, the pattern of each color used in the printing and dyeing method, special printing belongs to the second category, the reason for this classification, because this kind of method can obtain special printing effect, or because of the high cost of the process and not widely used
1.full floor printing
full floor printing of the base color through the printing method and not using the dyeing method to obtain. Usually, in the printing process, the base color and the color of the pattern are printed on white cloth. Sometimes full-field printed fabrics are designed to mimic the more costly plucked or dye-proof printing effect, but it is easy to distinguish the different printing methods from the reverse side of the fabric. The reverse side of a full-field print is lighter; because the fabric has been dyed first, the front and back of a plucked or dye-proof print are the same color.
The problem of full-field printing is easy to appear is sometimes a large area of the base color can not be covered by the dark color. When this problem occurs, carefully check the full floor pattern, will find some dull color spot. This phenomenon is basically caused by washing, rather than due to the amount of dye coverage caused by.
These phenomena do not occur in high-quality full-field printed fabrics produced under strict process conditions. This phenomenon is also not possible when using screen printing for floor printing, because the color paste is scraped on, rather than being rolled in like roller printing. Painted floor printed fabrics are usually very stiff to the touch.
2.Flocking printing
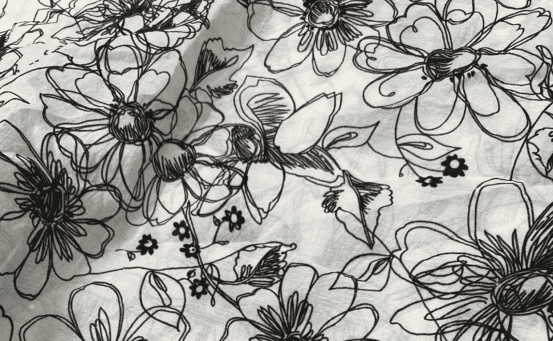
flocking printing is called fiber pile fiber pile (about 1/10-1/4 inch) in accordance with a specific pattern of adhesion to the surface of the fabric printing method. The process consists of two stages: first, a pattern is printed on the fabric using an adhesive rather than a dye or paint, and then the fiber pile is bonded to the fabric, which is only fixed to the part to which the adhesive has been applied. There are two ways to adhere the fiber staple to the fabric surface: mechanical flocking and electrostatic flocking. In mechanical flocking, the fiber pile is sieved onto the fabric when the fabric passes through the flocking chamber in a flat format.
The machine agitation will make the fabric vibrate, and the fiber staple is randomly placed into the fabric. In electrostatic flocking, electrostatic force is applied to the fiber staple, and as a result, almost all fibers are arranged in an upright direction when they stick to the fabric. Compared to mechanical flocking, electrostatic flocking is slower and more costly, but produces a more uniform and dense flocking effect. The fibers used for electrostatic flocking include all fibers used in actual production, of which viscose and nylon are the two most common.
In most cases, the staple fibers are dyed before being transplanted onto the fabric. The ability of flocked fabrics to withstand dry cleaning and/or washing depends on the nature of the binder. Many high quality binders used in the fabric processing process have excellent fastness to washing, dry cleaning, or both. Because not all adhesives can withstand any type of cleaning, it is important to verify which cleaning method is appropriate for any particular flocked fabric.
3. Warp printing
warp printing refers to the fabric before weaving, the warp yarn printing, and then woven into the fabric with plain weft (usually white), but sometimes the color of the weft yarn and the color of the printed warp yarn contrasts greatly. The result can be obtained on the fabric of the soft shadow pattern, or even blurred effect of the pattern. Warp printing production needs to be careful and meticulous, so almost only in high-grade fabrics can be found on this printing fabric, but the use of heat transfer method of printing fibers woven into the fabric is an exception. With the development of warp heat transfer printing, the cost of warp printing has been greatly reduced. Warp printing can be identified by pulling out the warp and weft of the fabric, because only the warp yarn has the color of the pattern, and the weft is white or plain. It can also be printed to imitate the effect of warp printing, but this is easy to identify, because the color of the pattern will be on both warp and weft.
3.Rotten flower print
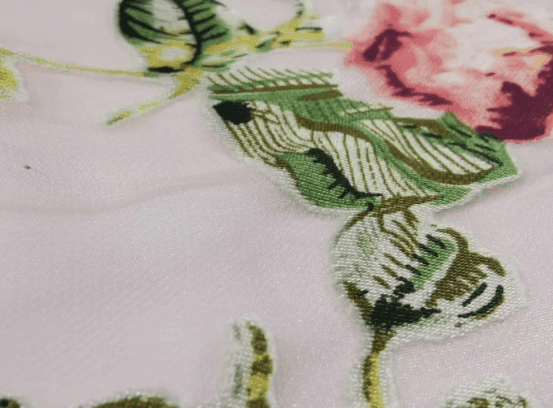
Ragged printing refers to the printing of chemicals that can destroy the fiber tissue at the pattern design. Therefore, the contact of chemicals and fabrics will produce holes. With 2 or 3 rollers printing can get imitation mesh embroidery fabric, one roller contains destructive chemicals, the other roller printing imitation embroidery stitch.
These fabrics are used for inexpensive summer shirts and cotton undergarments for women with raw edges. The edges of the holes in the floral prints are always subject to premature wear, so the fabric is poorly resistant to wear. The other type of foul print is a fabric made of blended yarn, corespun yarn, or an interweave of two or more fibers, where chemicals can destroy a fiber (cellulose), leaving the other undamaged fibers. This printing method can produce many special and interesting printed fabrics.
Fabric can be made of viscose fiber / polyester 50/50 blend yarn, rotten printing, viscose fiber parts disappear (rotten), leaving undamaged polyester fibers, the result of the print only polyester yarn, not printed at the original polyester fiber / viscose fiber blend yarn show the same
4.Double-sided printing
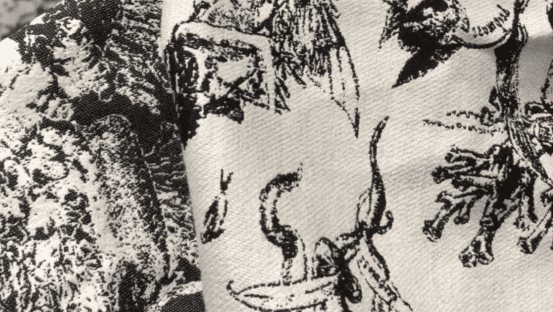
Double-sided printing is printed on both sides of the fabric, can obtain a double-sided effect of the fabric, the appearance is similar to the packaging fabric printed on both sides with a coordinated pattern. The end use is limited to double-sided sheets, tablecloths, no lining or double-sided jackets and shirts.
6. Specialty printing
Specialty prints are prints with two or more unique patterns, each printed on a different area of the fabric, so each pattern will be located in a specific location on the garment. For example, a clothing designer would design a women’s shirt with blue and white polka dots on the front and back pieces, and the sleeves would be the same blue and white, but with a striped pattern. In this case, the garment designer has to work with the fabric designer to design both polka dot and stripe elements on the same roll of fabric. Must carefully arrange the layout of the location of the print and each pattern element requires the number of yards of fabric, in order to make the best use of fabric, will not cause too much waste. Another kind of special printing is already cut into pieces of clothing printed, such as bags, collars, so you can create many different, unique clothing patterns. Pieces can be printed by hand or by heat transfer.
Printing process
The traditional printing process includes pattern design, cylinder carving (or screen plate, round net production), color paste modulation and printing pattern, post-processing (steaming, desizing, washing) and other four processes.
I. Pattern design
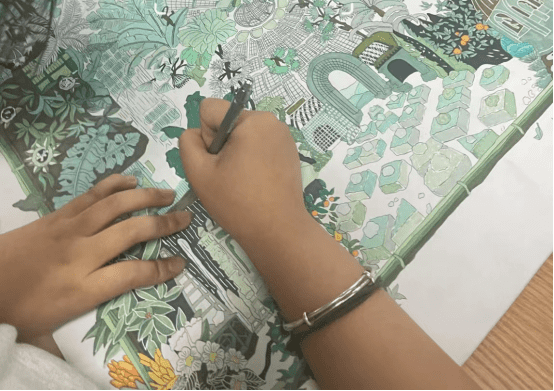
1. According to the use of the fabric (such as men’s clothing, women’s clothing, ties, scarves, etc. grasp the style, tone and pattern of the pattern.
2. Coordinate with the style of fabric material, such as silk products and hemp products have a great difference in the degree of delicacy and color purity.
3. pattern performance techniques, color sets and pattern structure to meet the printing process and the width of the fabric, silk direction, garment cutting and sewing and other factors. Especially the different printing methods, the pattern style and performance techniques are also different, such as roller printing color sets of 1 to 6 sets, flower width by the size of the drum restrictions; and screen printing color sets of up to 10 sets or more, the arrangement cycle is large enough to print a single fabric, but not suitable for the design of neat and regular geometric patterns.
4 pattern style design should consider the market and economic benefits
2.Net making
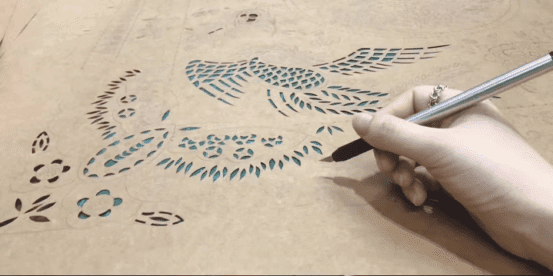
Flower cylinder, screen and round net are specific equipment for printing process. In order to make the designed pattern in the role of the color paste, the corresponding pattern on the fabric, need to carry out cylinder carving, screen plate and round net production process engineering, so as to form the corresponding pattern model.
1. Cylinder carving: roller printing machine printing, pattern carving on the copper cylinder, inside the twill line or network, to store the color paste. The process of engraving concave patterns on the surface of the copper roller is called cylinder engraving. Cylinder with iron hollow roller copper-plated or cast with copper, the circumference is generally 400 ~ 500mm, depending on the range of the printing machine length. Pattern engraving methods are manual engraving, copper core engraving, shrink engraving, photographic engraving, electronic engraving, etc.
2. Screen plate: flat screen printing requires the production of the corresponding screen. Flat screen plate including the production of screen frame, taut screen and screen pattern production. Screen frame made of hard wood or aluminum alloy, and then a certain specification of nylon, polyester or silk fabric tightly taut in the screen frame, that is, into a screen. Screen pattern production commonly used photographic method (or electronic color separation method) or anti-paint method.
3.Round net production: round screen printing needs to make a round net. First make the nickel mesh with holes, and then use the round metal frame in the nickel mesh ends, the nickel mesh taut. Then coated with photosensitive glue on the nickel net, the pattern of color tracing piece wrapped tightly in the nickel net, using the photosensitive method to make a pattern with the round net.
3.color paste modulation and printing pattern
Printing, drying, usually to steam, color or solid color treatment, and then desizing, washing, full removal of paste in the color paste, chemicals and floating color.
4.treatment (steaming, desizing, washing)
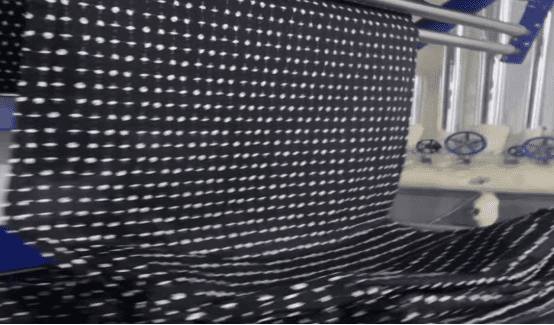
Steaming is also known as steam. Printing color paste to the fabric after drying, in order to make the dye transfer from the color paste to the fiber and complete a certain chemical change, generally also need to enter the steam. In the steam process, the steam first in the fabric condensation, so that the fabric temperature rises, fiber and paste swelling, dyes and chemicals dissolved, some chemical reaction, then the dye will be transferred from the color paste to the fiber, so as to complete the process of dyeing.
In addition, printing dyestuff due to the presence of paste, the dyeing process is more complex, the steaming time than dyeing in the dyeing of rolling dyeing steaming time is longer. Steam process conditions also vary with the nature of different dyes and fabrics.
Finally, the printed fabric should also be fully desizing and washing, washing the paste on the fabric, chemical reagents and floating color. Paste residue in the fabric, so that the fabric feel rough. Floating color residue on the fabric, will affect the color vividness and dyeing fastness.
Printed Fabric Defects
Listed below and described by the printing process caused by the most commonly occurring printing defects. These defects may be caused by improper operation in the printing process, or may be printed before the fabric is improperly treated, or the printed material itself has defects. Because textile printing in many ways similar to dyeing, many defects in dyeing in the printed fabric also exists.
1. Printing dragging pulp (colordrag) printing color paste before drying due to friction and staining.
2. Splash color (colorsplatter) printing color paste is not smoothly poured on the fabric, but splashed in or splashed on the fabric, producing color spots or splash color.
3. Pattern blur (fuzzypattern) pattern edge is not polished, the lines are not clear, most often caused by improper firing or color paste concentration is not appropriate.
4. inaccurate flower (off-register) due to the longitudinal alignment of the printing cylinder or screen is not aligned, resulting in inaccurate alignment of the front and back of the flower pattern. This defect is also called inaccurate color registration or pattern shift.
5. Parking print (stopmark) because the printing machine in the printing process suddenly stop, and then turn on the machine, the result in the fabric color stripes.
6. Part of the brittle (tenderspots) in the printing fabric, printed with one or more color place often damaged, usually due to the use of excessive destructive chemicals in the printing pulp. In the plucking dye printing fabric plucking parts can also be found in this problem.