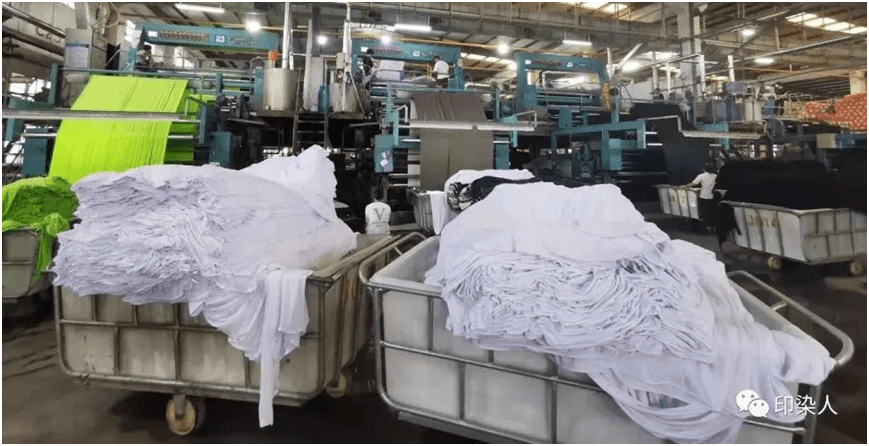
Trước tiên hãy hiểu các kiểu vải khác nhau
Kiểu vải thường đề cập đến các đặc tính độc đáo của vải và khác với các sản phẩm khác, chủ yếu bao gồm các đặc tính bên ngoài và đặc tính bên trong. Thông thường, các đặc tính bên ngoài có thể được thể hiện rõ ràng hơn, được các nhà chế biến và người tiêu dùng chấp nhận một cách trực quan, chẳng hạn như nếp nhăn trên bề mặt vải, viên kim cương nhỏ, các hạt nhỏ giống như ngọc trai, v.v.
Kiểu dáng bên ngoài của vải thuộc về khía cạnh chính của kiểu dáng vải. Và phong cách bên trong đôi khi cần phải kiểm tra con người hoặc con người bằng những phương pháp đơn giản để nhận dạng, chẳng hạn như cảm giác của vải và độ đàn hồi của vải, v.v. Kiểm soát kiểu vải chủ yếu đề cập đến cách kiểm soát sự hình thành kiểu vải của các điều kiện quy trình khác nhau.
Vải giống crepe
Vải giống crepe chủ yếu bao gồm hai loại, một loại là kiểu crepe do cấu trúc mô của vải tương đối đặc biệt, loại còn lại là vải co giãn sợi ngang trong quá trình nhuộm và hoàn thiện có chủ ý khuếch đại tất cả các điều kiện quy trình và phương pháp xử lý có thể tạo ra bánh crepe dọc.
Một số loại vải crepe được hình thành bằng phương pháp ép đùn, những sản phẩm như vậy cũng có thể thuộc loại vải kẻ sọc. Vải loại Crepe trong quá trình xử lý nên chú ý đến các khía cạnh chính từ độ co trước đến loại xác định trước, từ nhuộm đến sấy khô và cuối cùng là bộ thành phẩm.
Các loại vải giống crepe bao gồm vải crepe dọc và vải crepe sợi ngang, thường là vải crepe dọc. Do sợi ngang bị co quá mức trong quá trình xử lý nên sợi dọc không thể co lại theo sợi ngang thông thường và tạo thành các sọc không đều trên bề mặt vải. Để duy trì các sọc này, trong quá trình xử lý phải chú ý giảm thiểu độ căng khi xử lý sợi ngang. Nếu vải được co trước trong bể nhuộm, có thể tăng áp suất của vòi phun bể nhuộm một cách thích hợp để tăng độ căng dọc của vải trong quá trình xử lý. Trong quá trình sấy và định cỡ thành phẩm, bằng cách tăng độ căng dọc của vải, giảm chiều rộng cửa định cỡ một cách thích hợp, giữ lại hoàn toàn quá trình xử lý trước đó trên bề mặt vải hình thành các sọc dọc.
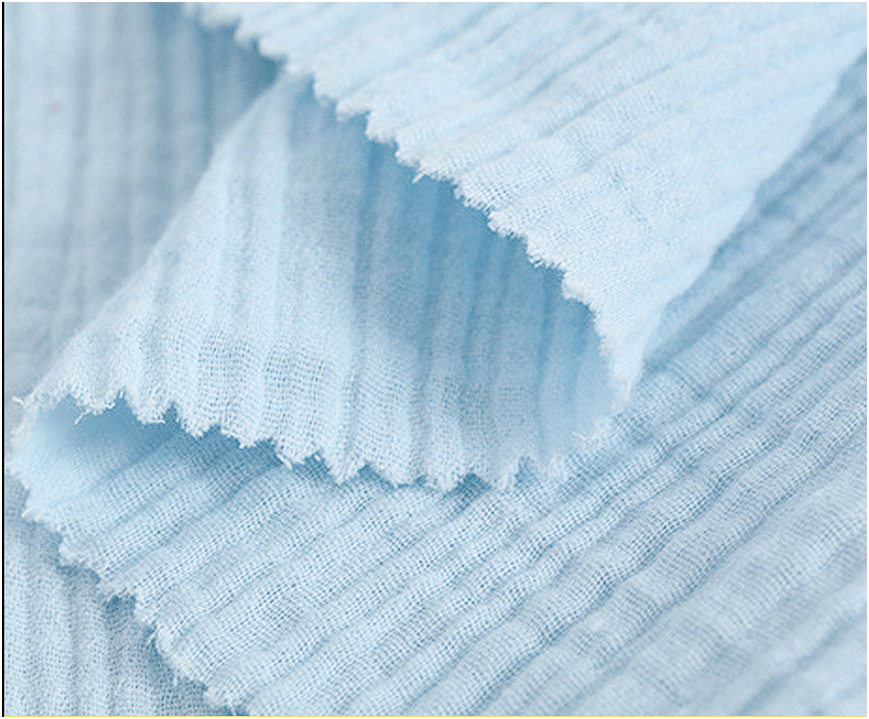
vải bong bóng
Có nhiều phương pháp tạo bong bóng, vải cotton có thể thông qua “co rút kiềm” phương pháp trên bề mặt vải để tạo thành một số lượng lớn các chỗ phình nhỏ giống như bong bóng, mà còn thông qua cấu trúc tổ chức của vải và các cài đặt mật độ sợi dọc và sợi ngang, để bề mặt vải thành phẩm tạo thành các hạt nhỏ giống như kim cương hoặc ngọc trai. Vải loại phồng rộp và vải loại crepe là khác nhau, trong quá trình xử lý không chỉ cần chú ý giảm độ căng dọc càng nhiều càng tốt mà còn phải đồng thời giảm độ căng của sợi ngang. Giảm độ căng dọc không chỉ bao gồm giai đoạn co rút trước vải, công đoạn đặt và nhuộm mà còn bao gồm công đoạn sấy khô và tạo hình thành phẩm.
Bề mặt hoàn thiện của vải poplin cotton có hình kim cương nhỏ rõ ràng, không chỉ cần đưa ra các yêu cầu thiết kế cần thiết về mật độ sợi dọc và mật độ sợi ngang của vải, trong thành phẩm khi định hình độ căng dọc và định hình chiều rộng cửa giữa quá trình hình thành kim cương nhỏ kiểu dáng trên bề mặt vải cũng có tác động không nhỏ.
Vải sợi lanh ngọc trai hoàn toàn bằng polyester nhẹ, không chỉ cần phải co trước, đặt, nhuộm và định cỡ thành phẩm càng nhiều càng tốt để giảm độ căng và căng dọc và ngang, và quy trình quan trọng là co rút trước và nhuộm sau làm khô nhiệt độ vải và độ căng dọc. Nếu nhiệt độ sấy vải quá cao và độ căng dọc quá cao ở trạng thái nhiệt ướt, kiểu dáng ngọc trai đầy đủ trên bề mặt vải sẽ bị ảnh hưởng nghiêm trọng. Việc sử dụng thiết bị sấy loại rời ở tốc độ sấy vải thấp hơn, càng nhiều càng tốt để giữ lại bề mặt vải đầy kiểu dáng ngọc trai, là trọng tâm của việc kiểm soát kiểu dáng bề mặt vải loại phồng rộp.
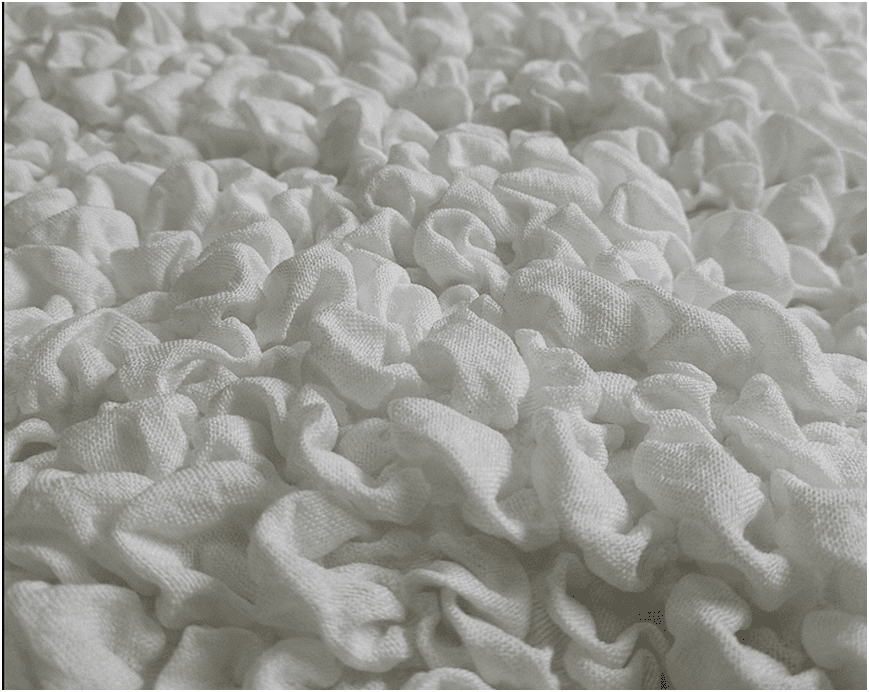
Vải đánh bóng
Cán lịch là một quá trình tạo độ bóng đặc biệt cho bề mặt vải. Cán bằng máy cán là phương pháp xử lý chính của cán vải. Có hai loại thiết bị cán được sử dụng phổ biến, một là máy cán nhiệt bằng điện và loại kia là máy cán kiểu áp suất. Lịch làm nóng bằng điện còn được gọi là lịch điện, lịch áp suất có áp suất cơ học, áp suất dầu và áp suất không khí ba chiều. Cán giúp bề mặt vải sáng bóng, có thể làm nổi bật vẻ ngoài phong phú và sang trọng của vải, phản ánh sở thích thẩm mỹ của người mặc quần áo và theo đuổi cá nhân.
Cán vải khi nhiệt độ cán, áp suất cán, thời gian cán, tốc độ cán và độ bóng bề mặt vải là những yếu tố chính ảnh hưởng đến hiệu quả cán vải. Nhiệt độ càng cao, áp suất càng lớn, càng nhiều lần thì độ sáng của bề mặt vải sau khi cán càng rõ.
Vải trơn, vải chéo và vải sa tanh sau khi cán, bề mặt vải sa tanh được hoàn thiện rõ ràng nhất. Vải sợi bông và vải sợi polyester hoàn toàn so với các loại vải sợi thông thường sau khi cán, độ bóng bề mặt rõ ràng hơn. Vải cuộn hoàn toàn bằng polyester cũng vậy, bản chất của nguyên liệu thô trên bề mặt hoàn thiện vải cũng tác động rất trực tiếp. Cùng một loại sợi, cùng mật độ, cùng cấu trúc mô của sợi FDY và sợi co giãn thấp DTY so với độ bóng bề mặt của sản phẩm FDY thường sẽ cao hơn sản phẩm DTY. Mật độ sợi dọc của vải cũng là một trong những yếu tố chính ảnh hưởng đến độ hoàn thiện bề mặt. Mật độ sợi dọc của vải càng cao thì bề mặt hoàn thiện càng tốt. Bản thân độ sạch bề mặt của vải trước khi cán cũng sẽ ảnh hưởng trực tiếp đến chất lượng của sản phẩm được cán. Nếu bề mặt vải có quá nhiều tạp chất, quá nhiều lông, quá nhiều mối nối sợi, sợi khô không đều, v.v. sẽ ảnh hưởng đến chất lượng của sản phẩm cuộn.
Nhiệt độ cao của quá trình cán nhiệt điện sẽ khiến vải sợi hóa học trở nên cứng khi chạm vào, cần đặc biệt chú ý trong quá trình xử lý. Để cải thiện độ mềm mại của độ bóng bề mặt của vải, có thể thực hiện việc cán bề mặt vải và bề mặt vải tiếp xúc giữa phương pháp cán. Độ phẳng của vải trong quá trình lăn nhẹ qua điểm cán ảnh hưởng trực tiếp đến mức chất lượng của quá trình gia công sản phẩm. Để giảm nguy cơ xuất hiện vết xước trên bề mặt vải trong quá trình lăn nhẹ, vải có thể được giãn nở đúng cách trước khi đi vào điểm lăn nhẹ. Trải rộng hấp thụ cạnh điện, trải con lăn thẳng có ren và trải con lăn cong là những phương pháp trải phổ biến hơn. Độ giãn nở của sợi con lăn thẳng, tốc độ quay của con lăn giãn nở và áp lực của con lăn giãn nở lên bề mặt vải không được quá lớn, nếu không sẽ dễ tạo ra vết mài mòn trên bề mặt vải.
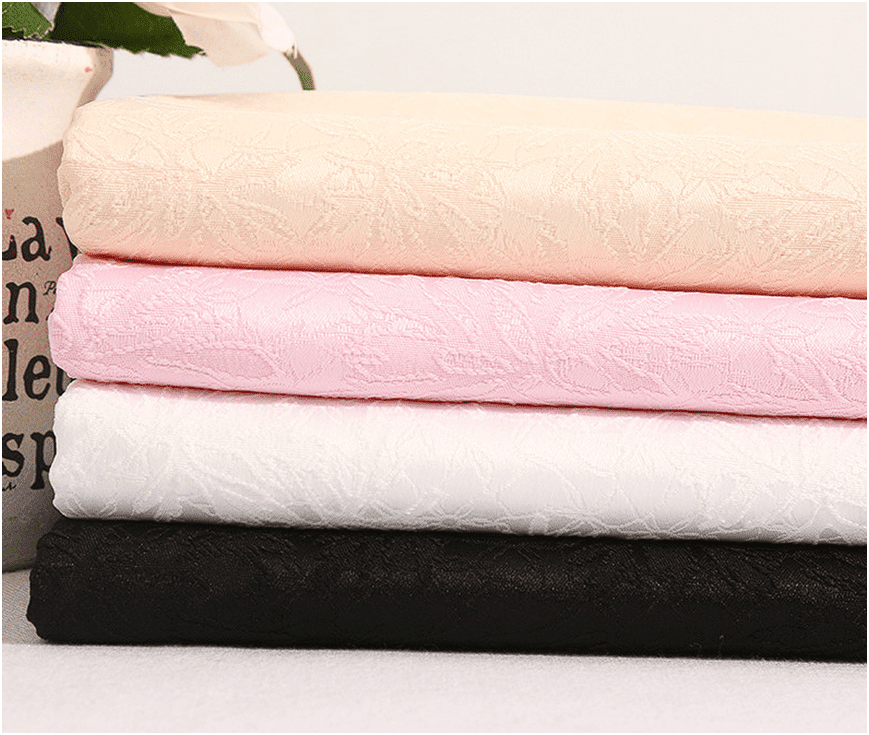
Vải đã qua chế biến
Quá trình gining thông thường được thực hiện trên máy gin. Máy lịch điện có thể hoàn tất quá trình cán vải sau khi thay thế các cuộn vải bằng mẫu. Trong quá trình cán, độ căng dọc của vải, nhiệt độ cuộn và tốc độ cán là các thông số chính của quy trình. Vải kẻ sọc thường thích hợp làm vải trang trí nhưng cũng có một phần nhỏ được dùng để may quần áo phụ nữ. Hầu hết quá trình cán vải được thực hiện sau khi vải thành phẩm được tạo hình.
Việc giữ được hình dáng vĩnh viễn của vải kẻ sọc là vấn đề cần phải được chú ý trong quá trình sử dụng sản phẩm vải kẻ sọc. Việc thực hiện các điều kiện xử lý tương đối khắt khe trong quá trình cán bông là cơ sở để duy trì tính lâu dài của sản phẩm gingham. Khi phát triển các điều kiện của quy trình, cần phải tính đến cả hiệu quả sản xuất và chất lượng của sản phẩm, cũng như khả năng chịu đựng của vải.
Vải nhung
Tính đồng nhất của việc chải là khía cạnh chính của chất lượng sản phẩm được chải. Vết đánh răng, xơ vải dài, phần đáy lộ ra ngoài, v.v... là những lỗi thường gặp khi chải răng. Giữ nguyên độ sắc nét của vải kim chải, tốc độ chạy của vải kim chải, độ căng chải, độ phẳng của vải khi chạy trên máy chải, độ phẳng của khớp sản phẩm, tốc độ chênh lệch giữa tốc độ trục lăn kim chính của máy chải và tốc độ ra vải, v.v. là những yếu tố chính ảnh hưởng đến chất lượng của sản phẩm chải.
Các sản phẩm sợi hóa học rất dễ tạo ra tĩnh điện trong quá trình chải, vì vậy việc mở bộ khử tĩnh điện khi xử lý là rất quan trọng. Sau khi chải một số sản phẩm, cần có quá trình cắt phụ để tăng độ đồng đều về chiều dài cọc trên bề mặt sản phẩm cọc dài. Số lần cắt và khoảng cách giữa con lăn cắt và con lăn đỡ vải quyết định chiều dài của cọc dài bề mặt vải. Các yếu tố như độ phẳng của bề mặt vải khi đưa vào vải và độ phẳng của các mối nối, độ mịn của thiết bị trong quá trình vận hành sẽ ảnh hưởng không nhỏ đến chất lượng cuối cùng của sản phẩm chải.
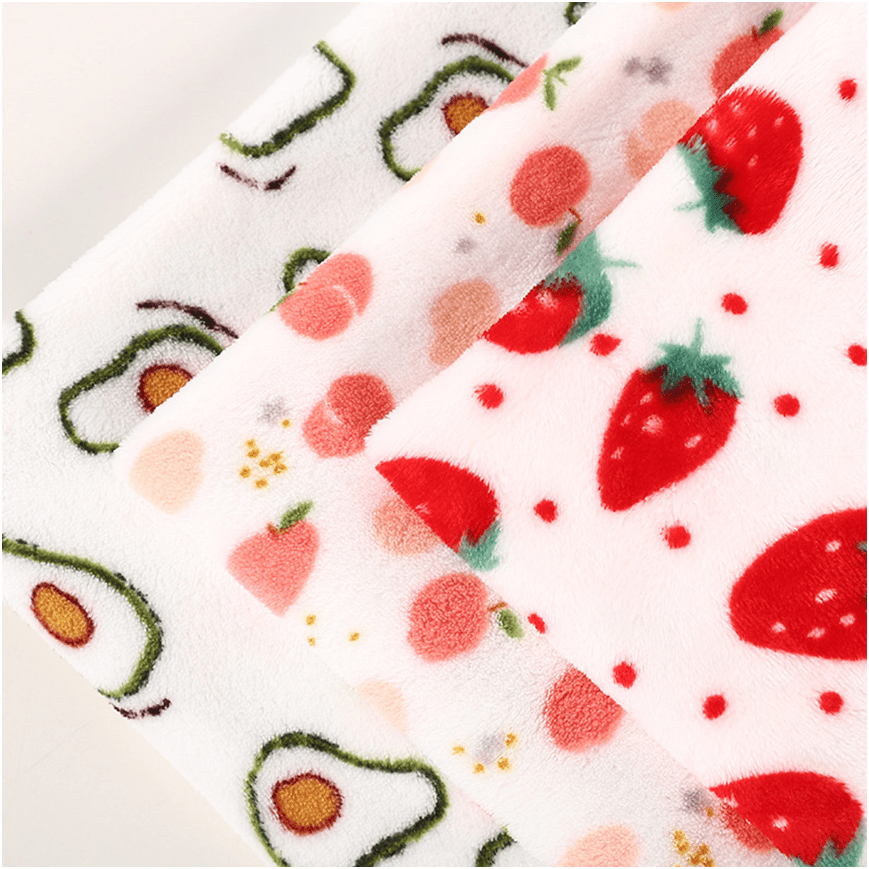
Vải chải
Đối với vải dệt thoi, việc chải ngày càng trở nên phổ biến, trong khi đối với vải dệt kim là cách chính để thay đổi tính chất bề mặt của vải. Đối với các loại vải cotton có mật độ cao, mật độ cao, xử lý đánh bóng bằng enzyme sinh học sau khi chải là một công nghệ xử lý mới. Dù mài hay chải, không chỉ có thể cải thiện đặc tính bề mặt của vải mà còn có thể cải thiện cảm giác của vải. Đồng đều, dày đặc và ngắn là những yêu cầu cơ bản của quá trình xử lý len chải.
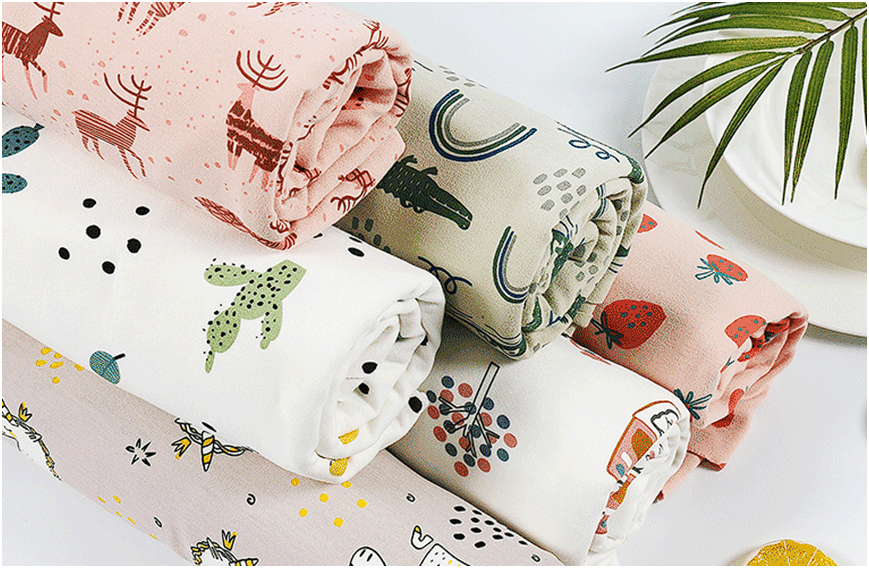
Các yếu tố khác nhau như cấu trúc mô vải, mật độ, đặc tính sợi, phương pháp chải, tốc độ chải, độ phẳng của vải trong quá trình chải và độ mịn khi vận hành thiết bị sẽ ảnh hưởng rõ rệt đến chất lượng chải.
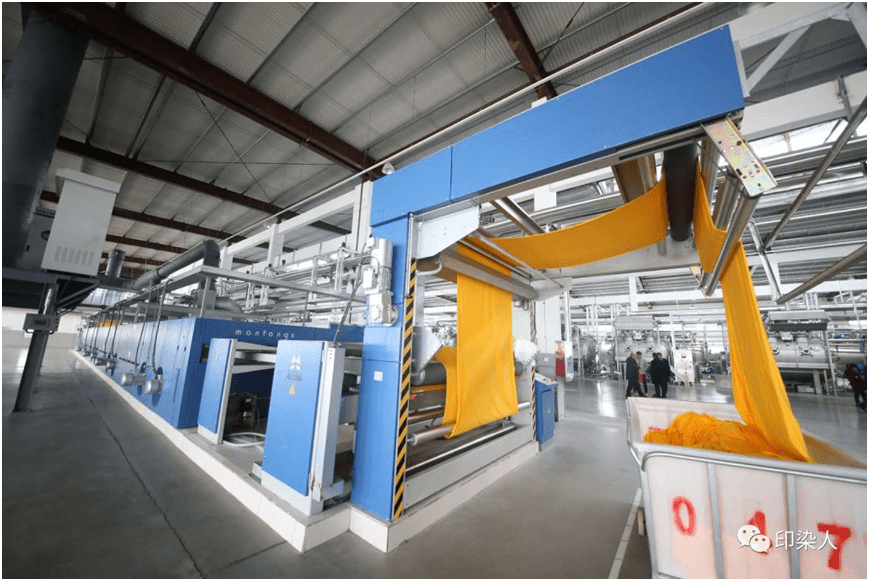
Tạo hình phải kiểm soát một số điểm
Nhiệt độ là yếu tố quan trọng nhất ảnh hưởng đến chất lượng gia nhiệt. Bởi vì sau khi vải được xử lý nhiệt, mức độ nhăn hiện có ban đầu được loại bỏ, độ phẳng bề mặt được cải thiện, kích thước của vải ổn định nhiệt và các đặc tính lấy khác, tất cả đều có mối quan hệ chặt chẽ với nhiệt độ cao và thấp -cài đặt.
Sau khi vải được dệt thành thành phẩm, để làm ra loại vải có một số mục đích đặc biệt, vải sẽ được xử lý tạo hình. Bởi vì vải sau khi định hình, các tính chất vật lý và hóa học ổn định hơn, ví dụ: độ co, chiều rộng, mật độ sợi dọc và sợi ngang, v.v. không dễ thay đổi, bề mặt của vải cũng phẳng hơn. Tuy nhiên, do nhiệt độ cài đặt cao hơn nên chúng ta nên chú ý đến sự thay đổi màu sắc trước và sau khi cài đặt, đặc biệt là một số màu nhạy cảm như xám, xanh quân đội, kaki nhạt, v.v., vì vậy nhìn chung chúng ta nên chú ý đến màu sắc. sau khi thiết lập. Đồng thời, việc cài đặt có thể kiểm soát chiều rộng của vải, mật độ sợi dọc và sợi ngang, tốc độ co rút, v.v., đặc biệt là việc kiểm soát tốc độ co rút, ảnh hưởng trực tiếp đến chi phí gia công cũng cần đặc biệt chú ý.
Các thông số và kiểm soát quy trình chính
1, Công thức
Tức là khi tạo hình trên chất lỏng nguyên liệu, tỷ lệ sử dụng các loại hóa chất khác nhau trong chất lỏng nguyên liệu quyết định cảm giác, độ trượt, màu sắc,… của vải sau khi tạo hình.
2, Áp lực con lăn
Áp lực của con lăn dùng để định hình vật liệu sẽ quyết định lượng chất lỏng của vật liệu mà vải mang theo, điều này có ảnh hưởng quan trọng đến cảm giác và màu sắc của vải.
3, Nhiệt độ sấy
Nhiệt độ sấy khi tạo hình là một trong những yếu tố chính ảnh hưởng đến chất lượng tạo hình, đặc biệt là trong quá trình hoàn thiện nhựa, nhiệt độ sấy tạo hình đến độ ổn định của kích thước vải, độ phẳng bề mặt có tác động lớn hơn, để hoàn thiện mềm mại, kiểm soát nhiệt độ sấy trong sản phẩm. Bề mặt vải khô vừa phải, nhiệt độ sấy không nên quá cao, nếu không sẽ ảnh hưởng đến cảm giác của vải.
4、Cho ăn quá nhiều
Kích thước của lượng thức ăn quá mức ảnh hưởng trực tiếp đến mật độ sợi ngang của vải, do đó ảnh hưởng đến hiệu suất co rút của vải, đồng thời tính đến độ căng của quá trình sản xuất vải để ngăn ngừa nếp nhăn cuộn và xiên sợi ngang một cách hợp lý.
Chiều rộng của khung định hình chiều rộng xác định chiều rộng của vải sau khi định hình, sao cho chiều rộng của vải sau khi định hình đáp ứng được yêu cầu của quá trình, sao cho chiều rộng của vải sau khi co trước đạt yêu cầu của khách hàng. .
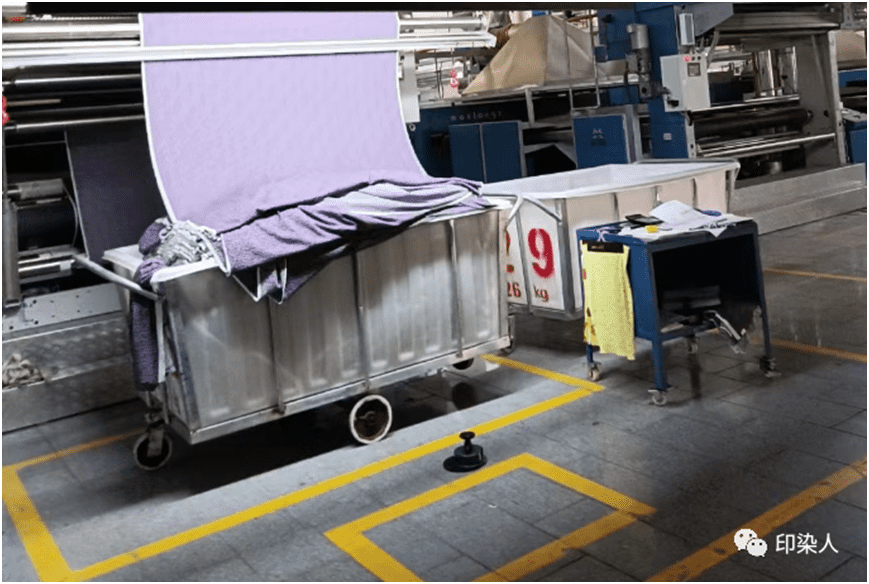
Điều kiện quá trình cài đặt nhiệt
Cài đặt nhiệt cho vải thường là quá trình giữ vải ở một kích thước nhất định, làm nóng vải trong một thời gian nhất định trong điều kiện nhiệt độ và độ ẩm nhất định rồi làm mát. Do đó, các điều kiện chính của quá trình cài đặt nhiệt chỉ là nhiệt độ, thời gian, độ căng và chất trương nở.
1, Nhiệt độ
Nhiệt độ là yếu tố quan trọng nhất ảnh hưởng đến chất lượng gia nhiệt. Bởi vì vải sau khi xử lý nhiệt, sự tồn tại ban đầu của các nếp nhăn bị loại bỏ, mức độ cải thiện độ phẳng bề mặt, kích thước của độ ổn định nhiệt của vải và hiệu suất lấy khác, có mối quan hệ chặt chẽ với nhiệt độ cài đặt nhiệt.
2、Thời gian
Thời gian tạo hình là một điều kiện quan trọng khác của quá trình cài đặt nhiệt. Sau khi vải vào khu vực gia nhiệt, thời gian cần thiết để cài đặt nhiệt có thể được chia thành các phần sau.
① vải vào vùng làm nóng, thời gian cần thiết để làm nóng bề mặt vải đến nhiệt độ cài đặt, hay gọi là thời gian làm nóng.
② Bề mặt vải phải đạt đến nhiệt độ tạo hình, sao cho vải bên trong và bên ngoài các bộ phận của sợi có cùng nhiệt độ tạo hình cần thiết cho thời gian truyền nhiệt.
③ vải để đạt đến nhiệt độ định hình, các phân tử trong sợi, theo các điều kiện định hình, sẽ có thời gian cần thiết để điều chỉnh, hay gọi là thời gian điều chỉnh phân tử.
④ vải ra khỏi phòng sấy, để kích thước của vải cố định trong thời gian cần thiết để làm mát, hay còn gọi là thời gian làm mát. Thông thường đề cập đến thời gian tạo hình, thường đề cập đến ba thời gian cần thiết đầu tiên và không bao gồm mục thứ tư.
Nếu hạng mục đầu tiên được coi là hiệu ứng làm nóng trước thì thời gian đông kết chỉ đề cập đến thời gian cần thiết cho hạng mục thứ hai và thứ ba, tức là thời gian cần thiết để truyền nhiệt và điều chỉnh phân tử.
Về thời gian cần thiết để gia nhiệt và truyền nhiệt, nó được xác định bởi hiệu suất của nguồn nhiệt, trọng lượng của vải trên một đơn vị diện tích, độ dẫn nhiệt của sợi và độ ẩm của vải, v.v.
3, Căng thẳng
Độ căng mà vải phải chịu trong quá trình cài đặt nhiệt có ảnh hưởng nhất định đến chất lượng cài đặt, bao gồm độ ổn định nhiệt, độ bền và độ giãn dài khi đứt của vải. Độ ổn định nhiệt theo chiều dọc tăng lên khi tăng lượng ăn quá nhiều của sợi dọc trong quá trình định cỡ, trong khi độ ổn định nhiệt theo chiều ngang giảm khi tăng mức độ kéo dài chiều rộng cửa.
Độ bền sợi đơn trung bình của vải sau khi định cỡ cao hơn một chút so với vải không tạo kiểu và sự thay đổi theo hướng sợi ngang rõ ràng hơn so với hướng dọc. Sau khi định hình độ giãn đứt của vải, hướng ngang giảm khi tăng mức độ giãn, trong khi hướng dọc trở nên lớn hơn khi tăng lượng cấp liệu quá mức.
Vì vậy, để vải có được kích thước ổn định nhiệt tốt và giúp cải thiện khả năng chịu lực của vải, việc cài đặt nhiệt phải phù hợp để đưa sợi dọc vào quá mức, độ giãn dài của sợi ngang không được quá cao. Vì lý do này, yêu cầu xử lý trước không sử dụng lực căng dọc lớn để không bị giãn quá mức và buộc sợi ngang phải co lại lớn, do đó cuối cùng cần phải có độ giãn lớn hơn.
①Số lần cuộn lại của chuỗi phân tử tăng theo nhiệt độ xử lý nhiệt.
(ii) Sức căng cản trở quá trình cuộn cuộn của chuỗi phân tử.
(iii) Ở nhiệt độ rất cao, vai trò của lực căng trong việc cản trở việc gấp dây xích giảm đi rất nhiều.
Lực căng có ảnh hưởng đáng kể hơn đến cấu trúc sợi và cấu trúc sợi có liên quan chặt chẽ với nhau, do đó, điều quan trọng là phải chú ý đến việc kiểm soát lực căng trong bất kỳ quá trình đông kết nào.
4, Chất hòa tan
Nước có “lỏng lẻo” cấu trúc sợi, tăng cường vai trò của chuyển động giống như chất lỏng của phân đoạn chuỗi phân tử. Độ ẩm trong quá trình dẻo hóa nhiệt, do đó ảnh hưởng đến cấu trúc siêu phân tử và tính chất vật lý của sợi.
Độ nghiêng sợi ngang là quá trình sản xuất vải trong điều kiện không ổn định về hình dạng ở nhiệt độ cao, ví dụ như bông, có thể bị rách bằng tay, nhưng dấu vết rách tự nhiên không phải là theo chiều ngang mà là một vết rạch, tức là độ nghiêng của sợi ngang rõ ràng hơn.
Vải nói chung có một sợi ngang nhỏ không phải là vấn đề lớn, không ảnh hưởng đến việc sử dụng thông thường, chỉ có kẻ sọc, dải dọc hoặc dải ngang không thể xuất hiện sợi ngang, hoặc mất thời gian cắt sản xuất là rất lớn, hoặc thậm chí không thể cắt được.
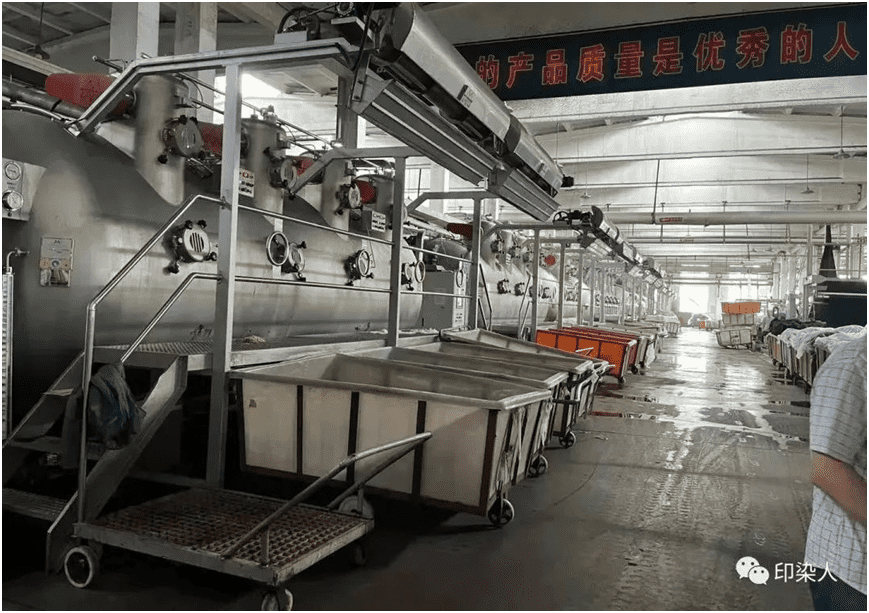
Phân loại khuyết tật độ dốc sợi ngang của sản phẩm
1, Đường nghiêng ngang có chiều rộng đầy đủ
Loại sợi ngang này được đặc trưng bởi sợi ngang về cơ bản là thẳng và tiêu chuẩn ngang có độ dốc khoảng 30 °. Loại nghiêng sợi ngang này là vải trong quá trình nhuộm và hoàn thiện bằng lực căng kéo về phía trước, khi giao điểm sợi dọc và sợi ngang trên lực có giờ lớn, sợi ngang không thể tiến về phía trước và có sự khác biệt giữa nhanh và chậm hoặc chậm Về phía trước, sự hình thành của sợi ngang bị lệch, có rất nhiều nguyên nhân dẫn đến sự xuất hiện của nó.
A. Nhà máy dệt vải đôi khi chật một mặt hoặc cả hai mặt chặt ở giữa, trong quá trình xử lý dây gây ra bởi cuộn gói, khó khăn về chiều rộng mở, dễ tạo ra một đường thẳng bị lệch.
B. Đôi khi, đường cắt mở của nhà máy dệt đến phôi không thẳng, đầu may của nhà máy in và nhuộm, không xé được khí trên đường may, dẫn đến đầu may bị nghiêng, do quá trình xử lý sau và không chỉnh sửa, thậm chí mức độ lệch hơn.
C. Khi xử lý chiều rộng phẳng, bề mặt con lăn không phẳng; lắp đặt con lăn không bằng phẳng; đường kính con lăn không cùng kích thước, không song song với nhau; lực ép ở hai đầu con lăn có kích thước; Đường tâm máy không thẳng, khiến vải chạy về phía không thẳng; chất lượng lắp đặt máy kém, chân cục bộ bị lỏng; một phần các bộ phận bị nghiêng, cong vênh của vải sang hai bên lực không đồng đều; máy làm bóng ở cả hai mặt của kẹp vải kéo chiều dài vải không giống nhau, dẫn đến độ lệch của sợi ngang; vào vải thiết bị hút cạnh kéo vải Góc giữa con lăn và vải quá nhỏ và độ căng ở cả hai bên không đồng đều; bong bóng địa phương “Túi nước” được tạo ra khi lăn chất lỏng theo chiều rộng phẳng; ổ trục dẫn hướng bị mòn hoặc đầu dò bị mòn; Con lăn áp lực trên máy kiểm tra vải có áp suất hai mặt khác nhau, miệng dao k của máy kiểm tra vải không bằng nhau sẽ gây ra hiện tượng nghiêng sợi ngang.
Tình trạng trên thuộc về tình trạng thiết bị không bình thường, nếu vận hành không đúng hoặc không theo hệ thống tiêu chuẩn cũng sẽ gây ra hiện tượng nghiêng sợi ngang.
Ví dụ như trong quá trình may vá, tham lam thuận tiện, thắt nút bừa bãi; khi con lăn phẳng đi vào, vận hành không đúng cách, khiến vải bị nhăn hoặc mép cuộn; cuộn vải rơi, vải bọc không phẳng; vào vải hoặc tua lại, hướng đông bị lệch hoặc trái phải.
Thứ hai, trong quá trình xử lý dây, độ căng không đồng đều, con lăn của máy giặt dây không phẳng, lực vải không đồng đều, lúc lỏng, lúc chặt, dễ gây ra hiện tượng nghiêng sợi ngang; Máy dệt dây quấn đầu chồng lên nhau, lực dọc vải không đồng đều, mòn quá nhiều rãnh, thân vải quá chật, tạo ra độ nghiêng sợi ngang đồng đều, đôi khi máy giặt dây đeo góc gói vải quá lớn, độ căng lớn, độ nghiêng của sợi ngang cũng to lớn; sản phẩm chế biến dây thừng tại địa phương “Túi nước “và gây ra độ dốc sợi ngang không đều, bọt bột giấy co lại “Túi nước” Rõ ràng hơn, khi vải phẳng thành dây, vòng tròn sứ không nằm ở giữa, phẳng thành dây hoặc dây phẳng, đôi khi khoảng cách quá ngắn, vải dễ quấn, cũng dễ tạo ra độ dốc sợi ngang, vải thả lớn J -hình hộp, đáy hộp hình vòng cung lớn, vải trượt Khó, dễ bấm và gây căng; Gia công dây thừng vào bể vải, chứa quá nhiều nước, dẫn đến khó khăn về chiều rộng mở và độ dốc sợi ngang.
2, Độ nghiêng ngang cong đầy đủ
Loại nghiêng ngang này được đặc trưng bởi độ nghiêng ngang hình cánh cung cong hoặc lõm của sợi ngang. Chủ yếu xảy ra ở con lăn uốn của con lăn giãn nở, do chiều rộng phẳng của con lăn uốn hoặc xi lanh nướng trước đây đôi khi có một nếp nhăn nhỏ và được lắp đặt một con lăn uốn, để mở rộng vai trò loại bỏ nếp nhăn. Khi áp dụng mức độ căng thích hợp để vải giãn ra, nếp nhăn cũng đồng thời kéo sợi ngang vào giữa cung lồi. Mức độ vòng cung lồi với vải có độ dày mỏng, độ cong của con lăn cong, vải trong con lăn cong do lực căng và các yếu tố khác.
Ngoài ra, trong máy làm bóng và máy định hình, vải được giữ về phía trước bằng kẹp vải, bằng không khí nóng, làm ướt kiềm bằng ánh sáng nóng hoặc sẽ giặt bằng kiềm, làm giãn vải, dẫn đến vải trong một phần của hiện tượng trễ câu hỏi, bên ngoài những chiếc kẹp vải là một vòng cung nghiêng nghiêng của sợi ngang. Tình trạng này dễ xảy ra hơn trên vải mỏng.
3, góc treo xiên ngang
Loại sợi ngang này có đặc điểm là sợi ngang bình thường một mặt vải, một mặt lệch.
Nguyên nhân: một mặt vải là một góc của lực; hoặc con lăn dẫn hướng, xi lanh sấy một mặt của một góc tích tụ cặn; hoặc ra khỏi con lăn vải chuyển động của vải bọc, về phía một mặt do quá dày; hoặc vào nhiều con lăn, một mặt của cạnh cuộn nghiêm trọng, chủ yếu được hình thành bởi chênh lệch áp suất trái và phải của con lăn. Kiểu nghiêng sợi ngang này khó dừng lại hơn, chỉ có thể dùng con lăn kéo căng toàn bộ sợi ngang hoặc con lăn áp lực đặc biệt luân phiên cho toàn bộ sợi ngang.
4, Độ dốc sợi ngang cục bộ cố định trong một phần vải
Kiểu dốc ngang này được đặc trưng bởi độ dốc ngang cục bộ có hình dạng đều đặn. Nguyên nhân chính là do bụi bẩn tích tụ trên con lăn dẫn hướng, chẳng hạn như cuộn dây trên dải vải đầu sợi; hoặc vải vào các con lăn trước dải vải nhăn, làm cho độ căng không đều. Do con lăn dẫn hướng bám bụi bẩn hoặc nếp nhăn được cố định nên vải tạo ra các phần xiên ngang và hình dạng cũng tương đối cố định.
5, Không có hình dạng đều đặn của độ dốc sợi ngang phức tạp
Vải trong máy phẳng do các bộ phận đơn vị hoặc máy gây ra bởi độ dốc sợi ngang ban đầu, về cơ bản là hình dạng đều đặn hoặc đều đặn, vị trí cũng được cố định. Nếu sợi ngang không được điều chỉnh kịp thời hoặc điều chỉnh không đúng cách, sau đó do ảnh hưởng bất thường của một số bộ phận của máy xử lý tiếp theo sẽ tạo ra sự tích tụ của độ dốc sợi ngang, tạo thành độ dốc sợi ngang phức tạp và phức tạp với nhiều hình dạng khác nhau. Tuy nhiên, kiểu dốc ngang này ít phổ biến hơn.
Các biện pháp chống lệch ngang
Độ nghiêng của sợi ngang được tạo ra từ nhiều khía cạnh, và các biện pháp ngăn ngừa tình trạng nghiêng sợi ngang cũng cần được thực hiện từ nhiều khía cạnh.
1, Thiết bị
Thiết bị có chiều rộng phẳng trên các cuộn, cuộn dẫn hướng, xi lanh sấy phải làm bốn việc gần như, đó là lắp đặt con lăn phải phẳng, độ song song giữa các cuộn phải phẳng, áp lực con lăn xung quanh phải phẳng. Đường trung tâm của thiết bị lắp đặt phải thẳng và phần sụn phía dưới phải chắc chắn.
Máy làm bóng, máy tạo hình, máy định hình và các chốt máy, ống bọc, dây chuyền khác phải được kiểm tra và thay thế thường xuyên để đảm bảo rằng cả hai mặt của kẹp vải hoặc tốc độ quay của tấm kim đều giống nhau.
Các con lăn dẫn hướng trên và dưới điều chỉnh tốc độ của từng bộ phận của máy có chiều rộng phẳng phải được giữ thăng bằng.
Vòng sứ dẫn dây phải được điều chỉnh sao cho bó vải nằm chính giữa. Để giảm độ căng của máy đơn dây, việc sử dụng vị trí tập tin hàng phân phối di động, sao cho vải mòn đầu sau cho vải mòn đầu phẳng, v.v., để kiểm soát số lượng kênh vải mòn. Để giảm độ căng khi quay đồng bộ của máy giặt dây, đường chạy phải thẳng, thiết bị dây một đầu có sẵn ống dẫn ánh sáng truyền động đồng bộ lỏng lẻo. Để tấm vải ra khỏi hộp lớn hình chữ J không bị ép, xiên sợi ngang lõm có thể đi vài con lăn cong để giãn rộng chiều rộng; Máy làm bóng tạo ra xiên sợi ngang lõm, có thể được lắp vào máy làm bóng từ kẹp vải sau khi bổ sung một cặp thiết bị sợi ngang cong, vải bên dưới có thêm một con lăn nhỏ mịn 10% hoạt động quá tốc độ, vải phía trên áp lực của con lăn uốn cao su hình vuông, hình chiếu cánh cung của tâm ép vào chính giữa chiều rộng của vải, tùy theo mức độ lõm của bề mặt vải xiên sợi ngang để điều chỉnh áp lực con lăn uốn cao su cong nêu trên Khi độ nghiêng của sợi ngang lồi đi đến phần uốn con lăn, hình lồi sẽ được lật sang hướng ngược lại để chỉnh lại sợi ngang, nhưng mức độ chỉnh sửa còn hạn chế, đồng thời phải ngăn chặn các nếp nhăn.
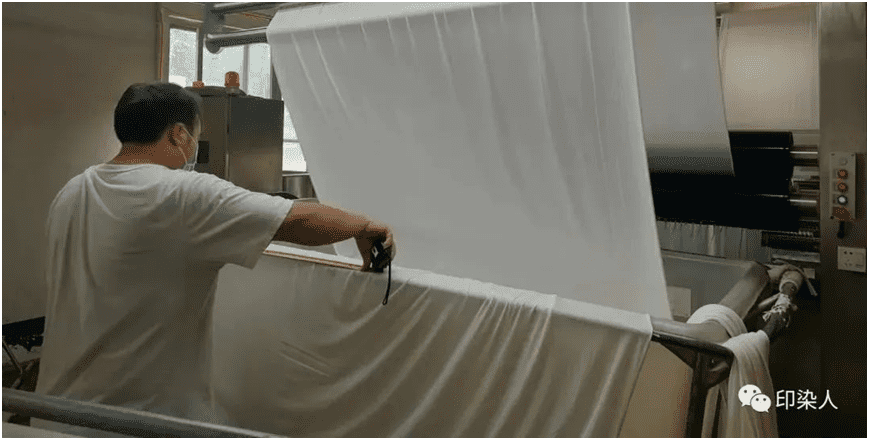
Máy thổi khí nóng phun miệng gió để thay đổi dạng thẳng đứng cho miệng gió xiên, tốc độ gió trong 12 ~ 15m/s, góc giữa miệng gió và bề mặt vải trong khoảng 15 ° ~ 20 °, sao cho gió thổi vào hướng bề mặt vải về phía trước, để cải thiện khả năng thoát khí nóng do độ nghiêng của sợi ngang hình vòng cung.
2. Vận hành
Đầu đường may phải phẳng và thẳng, mật độ kim vừa phải, cần xé đầu sau khi may càng nhiều càng tốt, độ dốc ngang của đầu đường may phải dưới 0,5%.
Vải dây không được thắt nút và phần đầu phải được khâu kỹ bằng máy may. Khi kết thúc quá trình xử lý dây đến đáy bể cọc, vải phải được cuộn khô và không bị ngập nước.
Để loại bỏ việc xử lý dây “Túi nước”, đặc biệt là tình trạng bột giấy bị thoái hóa “Túi nước”.
Vải quấn con lăn phải dày và mỏng đều nhau. Khi gia công tránh bị xơ, cuộn sợi và gây nghiêng sợi ngang. Khi xử lý chiều rộng phẳng, cần chú ý tránh để mép vải bị cuộn và nhăn. Lực tác động lên cả hai mặt của bộ hấp thụ cạnh điện phải đều và góc của miếng vải phải lớn hơn.
Máy đo vải phải phẳng và thẳng.