Chênh lệch màu gốc, trước và sau chênh lệch màu
nguyên nhân
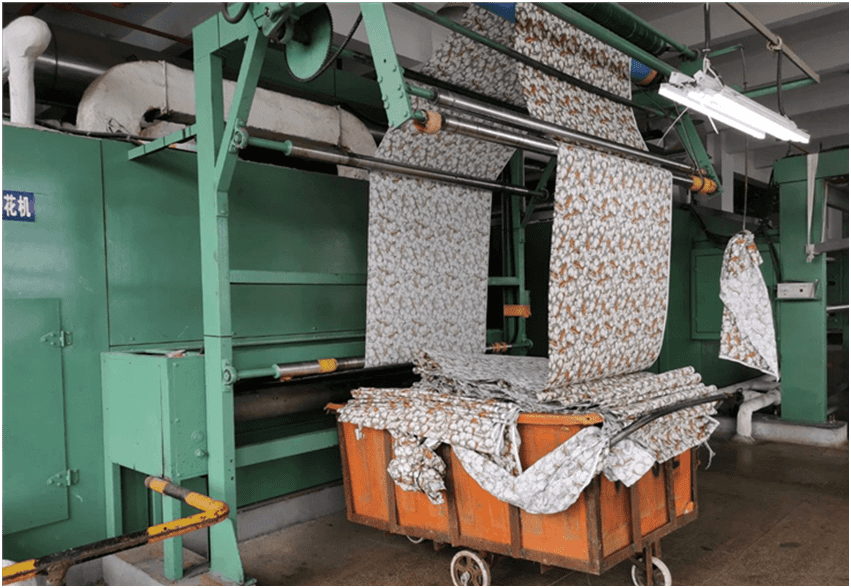
1. Thao tác không được tiêu chuẩn hóa và không có sự kiểm soát các thông số quy trình khi bắt chước màu sắc của các mẫu nhỏ, do đó các mẫu màu giả không thể phản ánh màu sắc và ánh sáng thực của công thức nhuộm.
2. Cân không chính xác, nguyên liệu hóa học không chính xác và kiểm soát không phù hợp các thông số kỹ thuật khác nhau khi giải phóng mẫu, mẫu không thể phản ánh màu bình thường của công thức nhuộm, ảnh hưởng đến phán đoán thông thường của nhân viên so màu và độ lệch của việc điều chỉnh công thức.
3. Các mẫu của khách hàng không được phân tích cẩn thận và sự kết hợp thuốc nhuộm được chọn cho công thức nhuộm khác với thuốc nhuộm được sử dụng trong các mẫu của khách hàng và có hiện tượng cùng màu và quang phổ khác nhau (đèn nhảy), xuất hiện màu sắc khác nhau dưới các nguồn ánh sáng khác nhau.
4. Lỗi tầm nhìn của nhân viên pha màu, dẫn đến việc phối màu không chính xác.
5. Mẫu nhỏ giả màu, mẫu xuất xưởng xe lớn sau khi không theo tiêu chuẩn hoàn thiện trong hợp đồng của khách hàng dẫn đến hàng về hoàn thiện màu sắc và ánh sáng thay đổi lớn.
6. Công thức nhuộm có sự chênh lệch hiệu suất thuốc nhuộm quá lớn, quy trình sản xuất ô tô lớn khi các thông số quy trình dao động thì sự thay đổi màu vải quá lớn.
7. Sự không nhất quán về hiệu ứng len, độ trắng, giá trị pH, rũ hồ và hiệu ứng mài len của bán thành phẩm trước khi nhuộm.
8. Sự biến động của các thông số kỹ thuật chính của quá trình nhuộm như biến động về mức chất lỏng nhuộm trong máng cán, tốc độ của xe, nhiệt độ nướng, nhiệt độ nướng, áp suất của xe lăn , nhiệt độ khử (màu đặc), thời gian, nồng độ của thuốc nhuộm, chất lỏng màu rắn, nồng độ của chất lỏng khử, v.v., dẫn đến thay đổi màu sắc.
9. Thuốc nhuộm bị biến màu khi ủi, dẫn đến việc phối màu không chính xác.
10. Nguyên nhân gây ra vải trắng: Các nhà sản xuất khác nhau, các lô vải trắng khác nhau của cùng một nhà sản xuất thường là do chất lượng sợi bông khác nhau, độ xoắn sợi khác nhau, kích thước sợi dọc khác nhau, độ hút nước và tính chất nhuộm của vải sau khi giặt khác nhau. xử lý, dẫn đến sự khác biệt về màu sắc giữa các hố khi nhuộm.
11. Nguyên nhân thuốc nhuộm: sự khác biệt về ánh sáng màu và độ mạnh của thuốc nhuộm từ các nhà sản xuất khác nhau và các lô khác nhau của cùng một nhà sản xuất.
Biện pháp phòng ngừa
1. Phân tích cẩn thận loại sợi, loại thuốc nhuộm, nguồn sáng màu, hiệu ứng hoàn thiện, v.v. của mẫu của khách hàng và sử dụng cùng một loại vải trắng có đặc điểm kỹ thuật, cùng loại thuốc nhuộm và cùng một quy trình hoàn thiện theo yêu cầu của hợp đồng. Nếu mẫu của khách hàng khác với vải hợp đồng thì nên làm mô phỏng một mẫu nhỏ rồi bàn giao cho khách hàng duyệt trước khi tổ chức sản xuất xe lớn.
2. Nhân viên mô phỏng màu mẫu nhỏ, nhân viên so màu xe lớn để thực hiện đào tạo và kiểm tra khả năng nhận biết màu sắc, tầm nhìn thống nhất của nhân viên liên quan.
3. Khi vận hành khớp màu, hãy đảm bảo tính nhất quán của các điều kiện khớp màu, chẳng hạn như nguồn sáng khớp màu, độ sáng, góc quan sát và khoảng cách, v.v.
4. Tăng cường kiểm tra hiệu suất của thuốc nhuộm được sử dụng, chẳng hạn như hiệu suất nung và cố định màu ở nhiệt độ cao của thuốc nhuộm phân tán, độ trực tiếp của thuốc nhuộm hoạt tính, giá trị dịch chuyển cụ thể, khả năng kháng kiềm và khả năng chịu nhiệt độ, v.v., để đảm bảo hiệu suất ứng dụng nhất quán của thuốc nhuộm được sử dụng.
5. Tăng cường quản lý cân, hóa chất, vật liệu trộn để loại bỏ sai sót, giảm thiểu sai sót.
6. Quản lý chặt chẽ hoạt động của máy, đảm bảo điều kiện kỹ thuật của từng quy trình đáp ứng tiêu chuẩn thiết kế quy trình.
7. Trong quá trình sản xuất bình thường, máy phải để mẫu tiêu chuẩn của quá trình sản xuất ô tô cỡ lớn ở tấm vải thả, đồng thời công nhân vải thả, người quản lý máy và người kiểm tra màu sắc nên kiểm tra mẫu bất cứ lúc nào để có thể phát sinh vấn đề. được phát hiện và xử lý kịp thời.
8. Khi phối màu, mẫu phải được làm nguội hoàn toàn để đạt độ ẩm bình thường và có thể làm khô bằng hơi ẩm và thổi điện.
9. Tăng cường quản lý vải trắng, hợp đồng, vị trí màu sắc để sử dụng cùng một nhà sản xuất của cùng một lô vải trắng.
10. Sử dụng cùng một nhà sản xuất và cùng một lô thuốc nhuộm để làm giả mẫu nhỏ, sản xuất ô tô lớn và sản xuất thông thường để ngăn ngừa sự biến động màu sắc do sự khác biệt về thuốc nhuộm.
Sự khác biệt màu sắc trái-giữa-phải
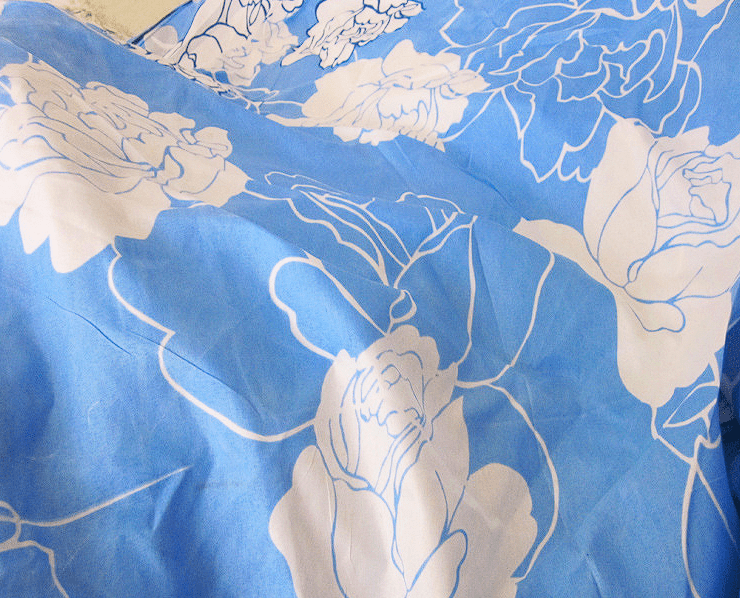
Nguyên nhân.
1. Các bán thành phẩm không nhất quán về tác dụng tổng thể, độ trắng và hiệu ứng kiềm hóa ở giữa bên trái và bên phải.
Nguyên nhân chính của sản xuất là
A. Áp suất không đồng đều ở giữa bên trái và bên phải của máy nghiền. Áp suất không khí xi lanh ở cả hai đầu của máy nghiền không nhất quán, độ mòn ổ trục ở cả hai đầu của máy nghiền không nhất quán và độ mòn của con lăn khác nhau dẫn đến lượng vải với chất lỏng không nhất quán.
B. Mỗi thùng chứa chất lỏng làm việc có nồng độ trái và phải không nhất quán.
C. kiềm hóa khi ngâm kiềm, hấp thụ mức độ la hét không nhất quán.
D-Giặt không đủ, vải còn lại ở độ pH phù hợp, chứa tạp chất, chất hoạt động bề mặt không đồng nhất.
2. Vải polyester và vải pha trộn, đan xen khi định hình nhiệt độ không đồng đều ở ô bên trái và bên phải.
3. Sự không nhất quán về tác dụng mài mòn ở mặt trái và mặt giữa bên phải của vải.
4. Khi nhuộm, sơn lót, giảm áp suất không khí lăn đồng đều ở hai đầu, kiểm soát áp suất dầu ở giữa không phù hợp, áp suất dòng xe lăn không nhất quán, dẫn đến vải bên phải có lượng chất lỏng khác nhau; nồng độ chất lỏng nhuộm thùng cuốn (chất lỏng khử, chất lỏng màu đặc) không đồng đều; sấy không khí nóng, sấy xi lanh khi mức độ sấy của từng bộ phận không đồng nhất, dẫn đến sự dịch chuyển của thuốc nhuộm; pha trộn polyester, đan xen vải phân tán khi nướng nhiệt độ bên trái ở bên phải là khác nhau; xe lăn đồng đều từng bộ phận Mức độ hao mòn khác nhau. Giảm nhiệt độ nồi hấp (màu đặc) là không đủ.
5. Công thức nhuộm chọn quá nhiều sự khác biệt về hiệu suất của thuốc nhuộm tạo màu.
6. Áp suất cán không đồng đều, nhiệt độ bên trong hộp quá cao, chênh lệch nhiệt độ quá lớn khi hoàn thiện và tạo hình.
Biện pháp phòng ngừa
1. Thường xuyên kiểm tra mức độ hao mòn của từng quá trình cán của bồn chứa chất lỏng đang làm việc (bao gồm rũ hồ, đun sôi và tẩy trắng, làm bóng, nhuộm và cán máy tạo hình, cán đồng đều) để đảm bảo lượng chất lỏng mang theo từng bộ phận của vải đồng đều và nhất quán.
2. Mỗi bể chứa chất lỏng làm việc sử dụng ống tràn để cung cấp nguyên liệu nhằm đảm bảo hệ thống chất lỏng làm việc đồng nhất và nhất quán.
3. Kiểm soát chặt chẽ các thông số kỹ thuật của từng quy trình như rũ hồ, tinh chế, tẩy trắng, làm bóng và các chất lỏng làm việc khác với nồng độ tác nhân, nhiệt độ trong nồi hấp, thời gian xếp chồng, độ ẩm trong hộp, nồng độ kiềm làm bóng, vòi giãn nở, kiềm độ đồng đều hấp thụ, v.v. phải được kiểm soát chặt chẽ và hiệu quả xử lý bán thành phẩm phải đáp ứng nhu cầu chất lượng của sản phẩm nhuộm.
4. Tăng cường giặt nước, sử dụng lưới chảy ngược theo lưới, bể giặt nước được ngăn cách bằng vách ngăn để tạo thành trạng thái dòng nước ngoằn ngoèo, phun nước nóng thích hợp để đảm bảo vải được giặt hoàn toàn đều và đều tác dụng.
5. Sấy khô trước bằng không khí nóng ở nhiệt độ phù hợp, thể tích không khí phải đồng đều, đảm bảo tất cả các phần của vải được làm nóng đều, tránh trường hợp thuốc nhuộm xảy ra hiện tượng trôi và gây ra hiện tượng lệch màu. Thường xuyên kiểm tra xem khí thải của hộp sấy trước có bình thường không, hoạt động của quạt tuần hoàn có bình thường không, độ đàn hồi của đai có ổn định, nhiệt độ tản nhiệt trái và phải ổn định hay không.
6. Trước khi nướng và sấy, cố gắng giảm độ ẩm trên vải để tránh quá nhiều độ ẩm trên vải, đồng thời khi nướng và sấy, chênh lệch nhiệt độ trên bề mặt hộp nướng sẽ khiến thuốc nhuộm bơi theo dòng hơi ẩm để tạo thành sự khác biệt về màu sắc.
7. Lò nướng ở nhiệt độ bên trái và bên phải để duy trì nhiệt độ ổn định, sao cho vải được làm nóng đều, thuốc nhuộm phân tán mức độ thăng hoa của độ cố định màu phù hợp. Lượng không khí trong ống dẫn khí trên và dưới của lò nướng phải nhất quán, lượng không khí ở bên trái, bên phải của cửa thoát khí phải đồng đều và hiệu suất cách nhiệt của lò phải tốt; lượng khí thải phải vừa phải, không quá lớn nếu không sẽ làm chênh lệch nhiệt độ trong lò tăng cao dẫn đến chênh lệch màu sắc.
8. Công thức quy trình nhuộm khoa học và hợp lý, phải chọn nhuộm các loại thuốc nhuộm phù hợp với hiệu suất khác nhau để phù hợp với màu sắc, chẳng hạn như thuốc nhuộm phân tán, hiệu suất tốc độ màu thăng hoa ở nhiệt độ cao, gần gũi, vị trí màu đặc biệt cần chọn các loại thuốc nhuộm tương tự cho màu phù hợp; thuốc nhuộm hoạt tính nên chọn độ trực tiếp thấp, giá trị dịch chuyển cao, khả năng kháng kiềm và chịu nhiệt độ, tỷ lệ màu rắn cao, dễ giặt, điều kiện màu đặc, thuốc nhuộm phù hợp để phối màu. Giảm sự thay đổi màu sắc do sự biến động bình thường của các thông số quy trình.
9. Thường xuyên kiểm tra bộ phận mồi và bộ phận khử xà phòng của tốc độ chất lỏng lăn xe đồng đều, giữ cho xe lăn ở tình trạng tốt, đường dẫn dầu khí trơn tru, van điều chỉnh linh hoạt và hiệu quả, và màn hình hiển thị đồng hồ linh hoạt và chính xác.
10. Tăng cường phát hiện tác động mài mòn của các sản phẩm mài mòn để ngăn chặn sự khác biệt màu nhuộm do hiệu ứng mài mòn của vải trái và phải không nhất quán.
Sọc màu, hoa màu
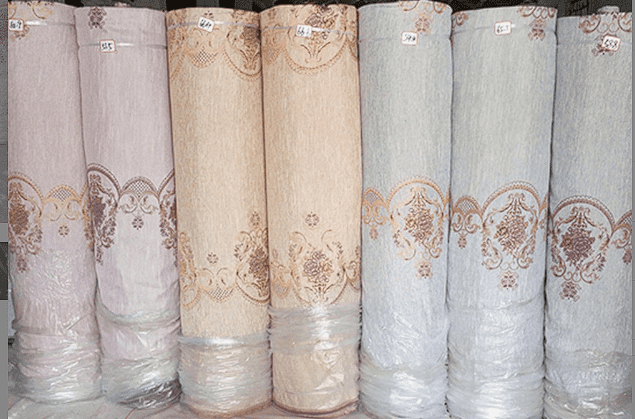
nguyên nhân
1. Hoa dải len cháy: dù là máy đốt len bằng ga, máy đốt len bằng điện đều dễ tạo ra hoa dải len cháy.
Những lý do chính khiến tóc bị cháy sọc là.
A. Đốt cháy quá mức, ngọn lửa miệng lửa quá dài (nhiệt độ xi lanh quá cao và hồ quang tiếp xúc với vải quá lớn) thời gian ngọn lửa tiếp xúc với vải quá dài, quá trình làm mát ở giữa không kịp thời, nhiệt độ thân chính của vải quá cao cao. Sợi polyester ở trạng thái nhiệt độ cao chuyển động chuỗi phân tử tăng cường, sự hình thành các kích cỡ và hình dạng khác nhau của các tinh thể khác nhau, do đó đặc tính nhuộm sợi thay đổi hình thành dải nhuộm nhuộm.
B. Miệng lửa bị tắc dẫn đến miệng lửa bị đứt ngọn lửa, bề mặt trụ không phẳng (mảnh vụn). Điều này dẫn đến các vệt lông không bị gián đoạn theo hướng cong vênh trên bề mặt vải sau khi đốt.
C. Tỷ lệ khí và không khí dễ cháy mất cân bằng, tỷ lệ không khí quá lớn, ngọn lửa nhảy vọt; Tỷ lệ không khí quá nhỏ, ngọn lửa dài và yếu, bề mặt vải nhìn tổng thể có cảm giác len không đồng đều của dải hoa.
2. Xả hồ không lưới, nấu không trong suốt dẫn đến nhuộm dải hoa. Chẳng hạn như nồng độ chất lỏng làm việc quá thấp, áp suất xe lăn quá lớn, nhiệt độ hơi quá thấp, thời gian quá ngắn, độ ẩm không đủ có thể dẫn đến hiện tượng rũ vải vải không đều, nấu không thấm nước, dẫn đến hiện tượng nhuộm sọc hoa .
3. Sự hao mòn cục bộ của xe cán, chất lỏng làm việc nhúng và cán vải với lượng chất lỏng khác nhau, hiệu quả xử lý vải là khác nhau, nhuộm màu khác nhau.
4. Đường vải trắng mỏng và dày, dải khô không đều, nhuộm và sấy khô khi nhuộm chuyển dịch tạo thành dải bóng và dải hoa giống như mưa.
5. Nhuộm khi sấy quá nhanh thuốc nhuộm sẽ bơi dịch chuyển tạo thành sọc như mưa.
6. Độ phân tán huyền phù thuốc nhuộm kém, dung dịch nhuộm trong máng cán thấp, dung dịch nhuộm chảy không đều trên bề mặt vải khi vải đi vào xe cán đồng đều, phân bố thuốc nhuộm không đều.
7. Thuốc nhuộm trong nồi hấp khử (màu đặc) ở nhiệt độ quá thấp, mức độ khử thuốc nhuộm (màu đặc) không đồng nhất, đã khử thuốc nhuộm có ái lực cao với vải, chưa bị khử thuốc nhuộm không có ái lực với vải, vải trong quá trình chạy thuốc nhuộm có dòng nước ngưng tụ dẫn đến hình thành các sọc.
8. Khi nhuộm vải chải, hiệu ứng chải không đồng đều trên bề mặt vải dẫn đến hình thành các sọc.
A. Giấy nhám dùng để đánh răng quá thô và độ nhám không đồng đều.
B. Lực căng mài mòn quá lớn và độ cong tiếp xúc giữa vải và con lăn mài mòn quá lớn.
C.Vải bị mài mòn trong tình trạng ẩm hoặc ẩm không đều, rất dễ tạo ra sọc.
D. Vết thương của đai mài mòn trên con lăn mài mòn không được cố định tốt, lỏng lẻo và di chuyển dẫn đến hiệu quả mài mòn không nhất quán.
biện pháp phòng ngừa
1. Xây dựng quy trình đốt len hợp lý, vận hành tiêu chuẩn máy đốt len nghiêm ngặt. Đảm bảo miệng lửa len cháy thông suốt không bị tắc nghẽn, sao cho miệng lửa ngắn, khí, đồng đều, cháy mạnh, không bị đứt ngọn, không nhảy vọt. Vải polyester và vải pha trộn, đan xen được đốt với ngọn lửa nhỏ và quá trình cháy nhanh. Tăng khả năng làm mát trung gian, giảm nhiệt độ thân chính của vải, giảm nhiệt độ vải để duy trì dưới 50 độ.
2. Tăng cường kiểm tra chất lượng vải phôi, chọn vải phôi đạt tiêu chuẩn chất lượng của sản phẩm nhuộm để tổ chức sản xuất.
3. Tăng cường công tác kiểm tra bán thành phẩm’ hiệu quả len, độ trắng, giá trị pH và hiệu ứng mài len để đảm bảo chất lượng bên trong và chất lượng bề ngoài của bán thành phẩm đáp ứng tiêu chuẩn chất lượng nhuộm.
4. Cải thiện độ ổn định phân tán cũng như khả năng làm ướt và thẩm thấu của dung dịch nhuộm huyền phù, cố gắng duy trì chiều cao của bề mặt chất lỏng để vải có thể hấp thụ đều dung dịch nhuộm; cố gắng giảm lượng chất lỏng mang theo vải để giảm sự dịch chuyển của thuốc nhuộm; khi sấy bằng không khí nóng, cố gắng hạ nhiệt độ phòng sấy và giảm tốc độ quạt tuần hoàn để tránh lượng không khí lớn và sấy khẩn cấp ở nhiệt độ cao làm trầm trọng thêm sự dịch chuyển của thuốc nhuộm gây ra bóng dải và sọc giống như mưa; khi sấy trong xi lanh sấy, cố gắng giảm nhiệt độ xi lanh sấy để tránh làm khô khẩn cấp. Máy hấp giảm (màu đặc) áp dụng phương pháp bịt kín không khí, giảm lượng vải bằng chất lỏng rõ ràng có thể cải thiện hiện tượng sọc; giữ nhiệt độ nồi hấp, cải thiện tốc độ khử thuốc nhuộm (màu đặc) để giảm dòng chảy của thuốc nhuộm, tránh tạo ra các sọc.
5. Theo đặc tính của vải, đặc điểm màu sắc của việc lựa chọn chất chống dịch chuyển hiệu suất tốt có thể cải thiện đáng kể hiện tượng sọc bóng.
6. Polyester pha trộn, nhuộm vải đan xen để đảm bảo độ đồng đều về độ sâu màu và độ sáng màu trên cả hai sợi.
7. Chọn hiệu suất nhuộm thuốc nhuộm bằng hoặc tương tự.
8. Tăng cường thiết bị, quy trình, vận hành và quản lý chất lượng của quy trình chải để đảm bảo hiệu quả chải của sản phẩm đáp ứng tiêu chuẩn chất lượng của sản phẩm nhuộm.
Sắc tố, sự biến màu
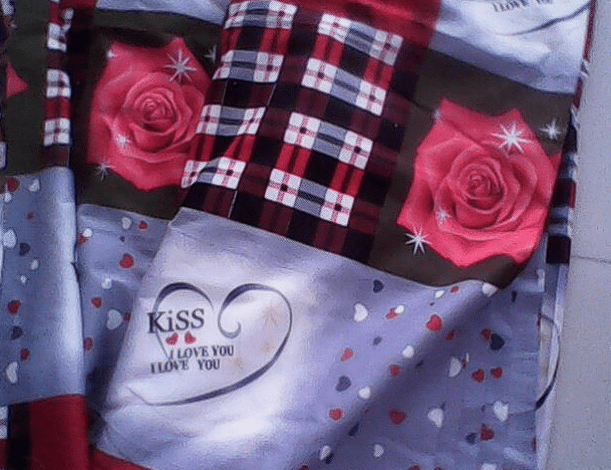
nguyên nhân
1. Khi chuẩn bị dung dịch nhuộm, thuốc nhuộm không được làm ướt và phân tán (hòa tan) đủ.
2. Dung dịch nhuộm không đủ ổn định, tích tụ và kết tủa thuốc nhuộm.
3. Dung dịch nhuộm ức chế tạo bọt kém, dung dịch nhuộm chảy không đều trong máng cán tạo thành bọt khi vải chạy. Thuốc nhuộm hấp phụ trên bề mặt bọt và quay trở lại bề mặt vải để tạo thành các đốm màu.
4. Xả cặn không hợp vệ sinh và không đồng đều, tích tụ bột giấy và ố màu. Nhuộm tạo thành vết màu.
5. Dư lượng phụ trợ tiền xử lý, chất hoạt động bề mặt trong axit, kiềm cao khi hình thành keo tụ, dán vải nhuộm màu dẫn đến đốm màu.
6. Sau khi hoàn thiện vải, các chất trợ hoàn thiện được nhuộm bằng thuốc nhuộm hoặc chất hoạt động bề mặt anion khi nhuộm và làm lại, dẫn đến sự kết dính làm ố bề mặt vải và tạo thành các đốm màu và đốm dầu.
7. Vệ sinh máy nhuộm chưa kỹ lưỡng, thùng nguyên liệu hóa chất, ống, van, máng cán, chia vải, con lăn dẫn hướng bị dính thuốc nhuộm, xe lăn, con lăn dẫn hướng, sấy sơ bộ, hộp nướng ống dẫn khí, hộp gió, hộp bị ố màu với thuốc nhuộm trên bề mặt vải để tạo thành các đốm màu.
biện pháp phòng ngừa
1. Sử dụng nước mềm khi chuẩn bị thuốc nhuộm để ngăn chặn các ion kim loại hình thành các đốm canxi với thuốc nhuộm và chất phụ trợ cũng như sự đông tụ và kết tủa của thuốc nhuộm.
2. Quản lý chặt chẽ hoạt động của các loại thuốc nhuộm, phân tán, khử và chuẩn bị dung dịch nhuộm huyền phù khác là tốt nhất nên sử dụng nước lạnh, quá trình khuấy thuốc nhuộm để kiểm soát chặt chẽ nhiệt độ dưới 50oC, để ngăn chặn sự ổn định phân tán tăng nhiệt độ khuấy tốc độ cao để giảm đông tụ thuốc nhuộm. Đối với thuốc nhuộm hoạt tính và thuốc nhuộm hòa tan trong nước khác, nên sử dụng nước lạnh để tạo thành bùn và thêm nước nóng ở nhiệt độ thích hợp để hòa tan thuốc nhuộm khi khuấy. Khi chuẩn bị dung dịch nhuộm, lọc kỹ thuốc nhuộm để loại bỏ các chất kết tủa và tạp chất không phân tán và hòa tan hoàn toàn.
3. Thực hiện vệ sinh máy nhuộm một cách cẩn thận và cẩn thận để tránh thuốc nhuộm còn sót lại trên máy làm ố vải và gây ra các đốm màu và vết ố.
4. Tăng cường kiểm tra hiệu suất của các chất trợ chất khác nhau được sử dụng trong tiền xử lý, nhuộm và hoàn thiện để đảm bảo tính ổn định của các chất lỏng làm việc khác nhau và giảm các đốm màu và vết bẩn khác nhau do hiệu suất của các chất trợ chất gây ra.
5. Tăng cường khả năng ngăn chặn bọt của chất lỏng nhuộm và khử (cố định). Khi bọt lỏng hoạt động nhiều hơn có thể thêm một lượng nhỏ chất khử bọt không chứa silicone (chất khử bọt phải được pha loãng và thêm từ từ từng giọt).
Lỗ và nước mắt
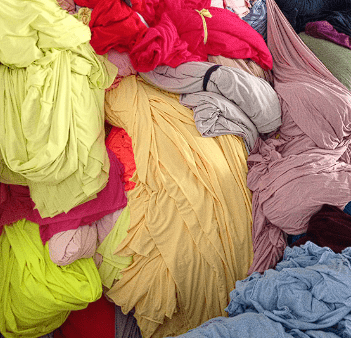
nguyên nhân
Lỗ thủng là vấn đề thường gặp ở các nhà máy in, nhuộm sản xuất sợi xenlulo và vải pha trộn, đan xen, gây ra mối đe dọa nghiêm trọng đến chất lượng sản phẩm. Các lỗ có thể được chia thành các lỗ oxy hóa và các lỗ cơ học. Các lỗ cơ học rõ ràng hơn, dễ tìm và xử lý, các lỗ oxy hóa rất ẩn, thường không dễ tìm thấy, chỉ trong quá trình kiềm hóa vải thông qua vai trò oxy hóa kiềm đậm đặc của cellulose, quá trình thủy phân tiếp theo, độ bền giảm đáng kể và sau đó thông qua con lăn dẫn hướng, kẹp vải của sợi dọc và sợi ngang đóng vai trò tạo ra các lỗ hình thành đứt sợi.
Những lý do chính cho việc này là
1. Vải có chứa sợi dầu hoặc các ion kim loại nặng, mạt sắt, rỉ sét, tro và các chất khác có tác dụng xúc tác cho quá trình phân hủy hydro peroxide.
2. Nước sử dụng (nước tái sử dụng) có hàm lượng ion kim loại nặng cao.
3. Độ ổn định của hệ thống tẩy trắng bằng hydro peroxide là không đủ và sự phân hủy hydro peroxide quá nhanh trong điều kiện nhiệt độ cao và kiềm cao.
4. Việc sử dụng nồng độ hydro peroxide quá cao, nồng độ xút quá cao, nhiệt độ hơi khí quá cao và thời gian quá dài.
5. Các mảnh vụn cứng bám vào các cuộn máy cán. Khi vải đi qua máy cán, nó tạo thành các lỗ đều đặn, có hình dạng tương tự với khoảng cách giữa chúng và chu vi của cuộn bằng nhau.
6. Các nút bông, sợi dọc và sợi ngang của vải trắng được nghiền bằng máy mài len khi các nút bông, sợi dọc và sợi ngang thô nhô ra khỏi bề mặt vải, sợi bị đứt tạo thành lỗ và đứt khi mài.
7. Kẹp vải của máy làm bóng bị biến dạng, biến dạng đường ray, điều chỉnh không đúng cách, khiến mặt vải chịu lực không đều, giãn nở chiều rộng của chiều rộng cửa quá rộng do mặt vải có lỗ, mép bị gãy.
8. Tấm kim của máy định cỡ bị hỏng, kim cong, đường đi của máy định cỡ không điều chỉnh được, chiều rộng của cửa quá rộng, nhiệt độ quá thấp khiến vải ra khỏi kim hiệu quả không tốt .
biện pháp phòng ngừa
1. Tăng cường chất thâm nhập, chất tinh chế, chất ổn định tẩy oxy, chất chelat và chất phân tán và các chất phụ gia khác, kiểm tra hiệu suất và rũ hồ, tinh chế, tẩy oxy chất lỏng làm việc, kháng kiềm và chịu nhiệt độ, ổn định dung dịch, hiệu suất nhũ hóa và phân tán, tinh chế, hydro peroxide tốc độ phân hủy và các thử nghiệm khác, đánh giá toàn diện về hiệu suất của các chất phụ gia khác nhau, theo đặc tính hiệu suất của chất phụ gia và các quy trình khác nhau để lựa chọn chất phụ gia thích hợp.
2. Tùy theo đặc điểm của loại vải mà chọn phương pháp xử lý sơ bộ phù hợp với loại vải đó. Chẳng hạn như vải bông có thể được sử dụng để xử lý đống cuộn lạnh, vải cuộn chất lỏng oxy kiềm sau khi đóng cọc ở nhiệt độ phòng, peroxide vải trên phân hủy có trật tự chậm, thiệt hại vải nhỏ, giảm cân ít hơn, cảm giác dễ chịu, giảm nguy cơ lỗ tẩy oxy . Vải polyester và bông có thể được sử dụng oxy kiềm trong quá trình tắm hơi ở nhiệt độ thấp, độ co rút của vải nhỏ, giảm trọng lượng ít, quy trình đơn giản, ít xả nước thải, COD thấp.
3. Xả hồ, tinh chế để tăng cường khả năng làm mềm nước và loại bỏ các ion kim loại trên vải.
4. Áp dụng quy trình tẩy trắng và đun sôi mạnh, giảm lượng hydro peroxide và chọn sử dụng chất ổn định có độ ổn định tốt, tốc độ phân hủy hydro peroxide thấp, khả năng chịu kiềm và nhiệt độ. Đảm bảo sự phân hủy chậm của hydrogen peroxide.
5. Tăng cường công tác phòng chống rỉ sét và loại bỏ rỉ sét của nhà máy, thiết bị, xe vải và các cơ sở khác để ngăn ngừa rỉ sét và mạt sắt làm ố vải.
6. Tăng cường kiểm tra chất lượng vải trắng và kiểm soát quy trình của máy mài, cải thiện độ mịn của giấy nhám và áp dụng quy trình mài nhẹ nhiều con lăn để giảm hư hỏng vải.
7. Tăng cường công tác kiểm tra, bảo dưỡng máy làm bóng, máy định cỡ vải (tấm kim) và đường ray, vận hành đúng quy trình.
In làm khô bằng không khí
nguyên nhân
1. Vải bị cháy cuộn nước (chất lỏng) sau khi bảo quản quá lâu, màng dịch chuyển bùn gây ra bởi bản in khô trong không khí.
2. Vải xếp chồng lên nhau trong hộp hấp, nhiệt độ không đều. Vải có lượng chất lỏng quá nhỏ, hộp hơi ở đáy mực nước quá thấp (hơi nước rò rỉ trong hộp) tạo thành hơi quá nhiệt do mất nước cục bộ khiến vải khô trong không khí. Áp suất hơi quá nhỏ và không khí lạnh đi vào bàn ủi làm khô không khí.
3. Lưu trữ lâu dài các bán thành phẩm, chất hoạt động bề mặt và chất kiềm còn sót lại trên vải bị ảnh hưởng bởi không khí, độ khô và độ ẩm hình thành sự phân bố không đồng đều và thay đổi tính chất của sợi.
4. Giặt vải nhuộm không đúng cách, bảo quản lâu, thuốc nhuộm trên vải bị ảnh hưởng bởi chất kiềm, khử khí, tiếp xúc với ánh sáng mặt trời tạo ra sự thay đổi màu sắc. Hầu hết các loại thuốc nhuộm hoạt tính không có độ bền ánh sáng mặt trời cao, chất kiềm dễ tạo ra thuốc nhuộm loại vinyl và phá vỡ liên kết sợi để tạo ra bản in khô trong không khí.
biện pháp phòng ngừa
1. tăng cường quản lý sản xuất, tránh đốt len sau thời gian dài bảo quản vải. Bảo quản ngắn hạn nên bọc màng để tránh bị khô trong không khí.
2. Tăng cường kiểm soát và vận hành quá trình rũ hồ, tinh chế, tẩy trắng, giữ cho hộp hơi có đủ hơi bão hòa, để loại bỏ hơi khô. Khi vì lý do nào đó mà dừng lâu, chúng ta nên để nguội và giặt vải kịp thời để loại bỏ bột giấy và chất tinh chế, đồng thời giặt và sửa chữa kịp thời.
3. Khi lưu trữ bán thành phẩm trong thời gian dài, có thể sử dụng khung chữ A để lưu trữ ở dạng cuộn.
4. Giặt vải nhuộm thuốc nhuộm hoạt tính cho vừa đủ, loại bỏ màu nổi trên vải, sử dụng chất tẩy rửa xà phòng axit, xà phòng có thể trung hòa hoàn toàn chất kiềm trên vải để loại bỏ ảnh hưởng của chất kiềm lên thuốc nhuộm, có thể kiềm ít nhuộm hơn sau không khí -sấy khô sản xuất in ấn. Vải được bảo quản bằng màng và bọc vải để tránh ánh nắng và ảnh hưởng của các loại khí độc hại.
Lỗi độ bền màu
nguyên nhân
1. Quá trình sàng lọc và đánh bóng vải kém, dẫn đến thuốc nhuộm không thấm và khuếch tán vào vải và tích tụ thuốc nhuộm trên bề mặt vải.
2. Sự lựa chọn thuốc nhuộm không hợp lý, cấu trúc thuốc nhuộm quyết định hiệu suất nhuộm và độ bền màu của nó.
3. Các hạt thuốc nhuộm quá thô hoặc không hòa tan hoàn toàn, ảnh hưởng đến sự thẩm thấu và khuếch tán của thuốc nhuộm vào các sợi bên trong.
4. Quá trình nhuộm không hợp lý, chẳng hạn như phương pháp sấy, nhiệt độ sấy, nhiệt độ nướng, thời gian nướng và nhiệt độ giảm (cố định). Thời gian khử (màu đặc), điều kiện xà phòng, v.v.
5. Thuốc nhuộm phân tán không làm mất màu của sợi xenlulo.
6. Thuốc nhuộm hoạt tính trong xà phòng kiềm. Liên kết ether được hình thành giữa thuốc nhuộm và xơ dễ bị phá vỡ trong điều kiện kiềm và nhiệt độ cao, dẫn đến độ bền giảm.
7. Chất trợ hoàn thiện trong chất nhũ hóa ở trạng thái nhiệt độ cao để thuốc nhuộm di chuyển lên bề mặt vải, dẫn đến giảm độ bền.
8. Giặt và xà phòng là chưa đủ và còn sót lại thuốc nhuộm chưa lắng đọng trên vải. Ngay cả sau khi hoàn tất việc xử lý bằng chất cố định màu, hiệu quả của nó vẫn không đạt yêu cầu.
biện pháp phòng ngừa
1. Vải tiền xử lý sôi để trong suốt, hiệu ứng len phải đồng đều và nhất quán, hút nước mạnh, kiềm hóa vừa đủ, vải có khả năng phản ứng hóa học tốt.
2. Làm tốt công việc áp dụng các thử nghiệm hiệu suất thuốc nhuộm khác nhau, chọn độ trực tiếp thấp, tốc độ nhuộm và cố định màu cao, dễ giặt màu thuốc nhuộm.
3. Thuốc nhuộm phân tán (khử) cần tăng cường trộn (nghiền) thuốc nhuộm, kiểm soát chặt chẽ độ mịn của thuốc nhuộm và cải thiện hiệu suất khuếch tán của dung dịch nhuộm.
4. Xây dựng quy trình nhuộm hợp lý theo hiệu suất của thuốc nhuộm để cải thiện hiệu quả cố định màu của thuốc nhuộm.
5. Phân tán/kích hoạt một bồn tắm cho màu tối, sử dụng chất tẩy rửa xà phòng trong một bồn tắm, phân tán và kích hoạt hai bồn tắm để có thêm màu tối.
6. Hoàn thiện mềm mại bằng cách sử dụng dầu silicon khối tự nhũ hóa để ngăn chặn sự di chuyển của thuốc nhuộm lên bề mặt vải; cố định để đảm bảo độ phẳng của vải và tốc độ co ngót với tiền đề giảm nhiệt độ cố định càng nhiều càng tốt.
7. tăng cường xà phòng, cách hiệu quả nhất là sử dụng chất xà phòng có tính axit để trung hòa triệt để chất kiềm trên vải, chọn chất cố định màu thích hợp để cải thiện độ bền của vải.
Dải nhăn, vết nhăn ép
nguyên nhân
1. Hiệu ứng thiết lập sợi ngang trống pha trộn polyester / cotton (bông nhân tạo) không nhất quán, trong quá trình in và nhuộm nhiệt ướt, trạng thái nhiệt độ cao để tạo ra mức độ co rút khác nhau.
2. Độ phẳng cơ học không đủ, áp suất không đồng đều ở các bộ phận khác nhau của máy nghiền (mòn cối xay, mòn ổ trục, áp suất không khí không đồng đều ở hai đầu) giữa các con lăn dẫn hướng không song song, v.v. khiến vải phải chịu sức căng khác nhau ở sợi dọc hướng và tạo ra nếp nhăn.
3. Khoảng cách giữa các con lăn dẫn vải, giữa các con lăn dẫn vải và các con lăn quá lớn.
4. Sấy bằng không khí nóng khi thể tích không khí quá lớn, vải chạy không êm sẽ tạo ra nếp nhăn.
5. Vải pha polyester trước nhiệt độ cài đặt quá thấp, chiều rộng cửa quá hẹp, lệch kim, v.v.
6. Mở rộng Mercerization không đủ chiều rộng chiều rộng quá hẹp; Máy kẹp vải kẹp vải bị biến dạng, kẹp đứt, cả hai bên của dây xích mòn không nhất quán, v.v.
7. Độ nghiêng của sợi vải quá lớn.
8. Con lăn bị mòn hoặc góc uốn không đúng, hiệu quả giãn nở kém; hướng dẫn biến dạng uốn con lăn vải.
9. Vải len trong len trước khi gấp vải áp lực bề mặt vải không phẳng, len khi hình thành các vết nhăn áp lực; nhuộm vải pha trộn polyester trước khi gấp nhiệt độ bảo quản quá cao, quá lâu để hình thành các vết nhăn do áp lực.
10. Vải bó sát sử dụng phương pháp hấp đống gấp, khi hấp dễ tạo ra vết nhăn do áp lực.
biện pháp phòng ngừa
1. Tăng cường bảo trì máy móc và thiết bị, duy trì độ phẳng cơ học, áp suất lăn đều và nâng cao khả năng thích ứng của các loại thiết bị.
2. Dải co rút sợi ngang có thể được sử dụng khi vải trống xuất hiện; nhuộm trước khi tạo hình để đảm bảo nhiệt độ đạt trên nhiệt độ nhuộm.
3. mài vải trước quá trình rơi vải bằng cách sử dụng cách cuộn, để tránh in nếp nhăn do áp lực.
4. Đóng vải bằng cọc cán nguội trước khi xử lý, có thể loại bỏ vết nhăn do áp lực.
5. Tăng cường máy định cỡ, kiểm tra đường ray (dây xích) của máy làm bóng, giữ cho cả hai mặt của chiều dài dây xích đều nhau, kẹp vải, tấm kim còn nguyên vẹn.
6. Sấy khô vải bằng khí nóng, tùy theo đặc tính của vải mà điều chỉnh lượng không khí của quạt tuần hoàn hợp lý, vải mỏng để giảm lượng không khí.
7. Kiểm soát chặt chẽ độ dốc sợi ngang của vải trong mỗi quy trình và sợi ngang của thiết bị hoàn thiện sợi ngang không được bị nhăn. Không có toàn bộ máy thiết bị sợi ngang vào vải và ra khỏi mức độ sợi ngang của vải, sự khác biệt quá lớn để tìm ra nguyên nhân và xử lý kịp thời.
Trong công nghệ in và nhuộm thay đổi nhanh chóng ngày nay, quy trình in và nhuộm để thích ứng với yêu cầu bảo vệ môi trường ít carbon, dựa vào tiến bộ công nghệ trong việc ứng dụng hiệu suất tuyệt vời của phụ gia in và nhuộm để đạt được nhiệt độ thấp, xử lý quy trình ngắn hiệu quả phương pháp nâng cao hiệu quả sản xuất và giảm chi phí sản xuất. Tăng cường quản lý chất lượng của doanh nghiệp, làm tốt công việc chuẩn bị trước khi sản xuất sản phẩm, xây dựng các biện pháp phòng ngừa đối với các vấn đề về chất lượng và kỹ thuật có thể xảy ra, để đạt được mục tiêu phòng ngừa. Tăng cường kiểm soát chất lượng quy trình, đảm bảo tỷ lệ thành công của sản phẩm cùng một lúc, loại bỏ việc sản xuất số lượng lớn sản phẩm làm lại và sản phẩm bị lỗi, đồng thời nâng cao danh tiếng về chất lượng sản phẩm và tầm nhìn của doanh nghiệp.