It is not easy to produce high quality printed fabrics, and it is even more difficult to produce high quality printed fabrics that are marketable. Because printed fabrics are the result of technology and art. It is both an industrial product and a work of art, to be loved by the consumer and to be accepted by the market. From the creation of the pattern to the printing of the fabric, a lengthy production line is required. Many main and auxiliary machines have to be used. The relationship between the production of printed fabrics is therefore traditionally compared to the ”five rings of contact”, that is, pattern design, colour matching and sizing. The five stages of production are: pattern design, colour matching and stitching. The five production stages are closely interlinked and a disconnection in any one of these stages will affect the quality of the printed fabric and its finish. Any disconnection will affect the quality and delivery of the printed fabric, while the printed fabric is the link between upstream and downstream. The upstream has to match the fibre material. The fabric style has to be matched. The downstream has to meet the fashion needs of the garment, so the pattern designer, the weaving designer and the garment designer have to work together to create the perfect printed fabric, which will eventually be presented on the market as a fashion garment.
Technical exchange activities for printing technology advancement
The printing industry in China has developed rapidly over the past 30 years and has undergone two technological leaps: before the 1970s, copper tumbling was the mainstay of printing, relying for a long time on hand-engraved copper spokes, and in the 1980s the use of photographic engraving became widespread. In the late 1980s, computerised colour separation and the use of wax and wax spraying were introduced. Computerised colour separation and wax and inkjet direct screen making and photographic engraving were used in a complementary way. This stage was the second leap forward in printing efficiency. This stage was the second leap forward in printing technology and greatly contributed to the technical progress of the printing process, with the penetration of high technology into the printing field. Various fibres. New materials. The application of new auxiliaries in the printing of fabrics has enriched the special effects of the printed fabrics.
The two leaps in printing technology are the result of the hard work and wisdom of the printing staff, and also reflect the importance that leaders at all levels have long attached to the printing industry, one is to organise study trips abroad for their printing counterparts, for example, the former Ministry of Textile Industry organised a study trip for printing technicians to Stork (Stork) to learn the technology of making circular nets. Finally, they have succeeded in making their own cylindrical nets, which are now commonly used in China from 60 to 125 mesh shackle nets; they also organised a study trip to Japan to learn about photographic engraving techniques. The second is to organise various forms of national exchange activities. For example, the former Ministry of Textile and Maggot Industry organised a national competition in Chengdu, Sichuan for the production of patterned printed fabrics on a considerable scale. Another example is the national technical exchange meeting on printing plate and screen production organised by Shenzhen Huawen Printing and Dyeing Technology Company, commissioned by the China Printing and Dyeing Industry Association. In addition to a live demonstration by experts from Stork, the Netherlands, on the production of cloud patterns on a circular mesh with computerised colour separation. For the first time in China, the Swiss company Rössbauer also presented the new technology of direct screen making with wax spraying. This was an important role in the creation of this new technology in China.
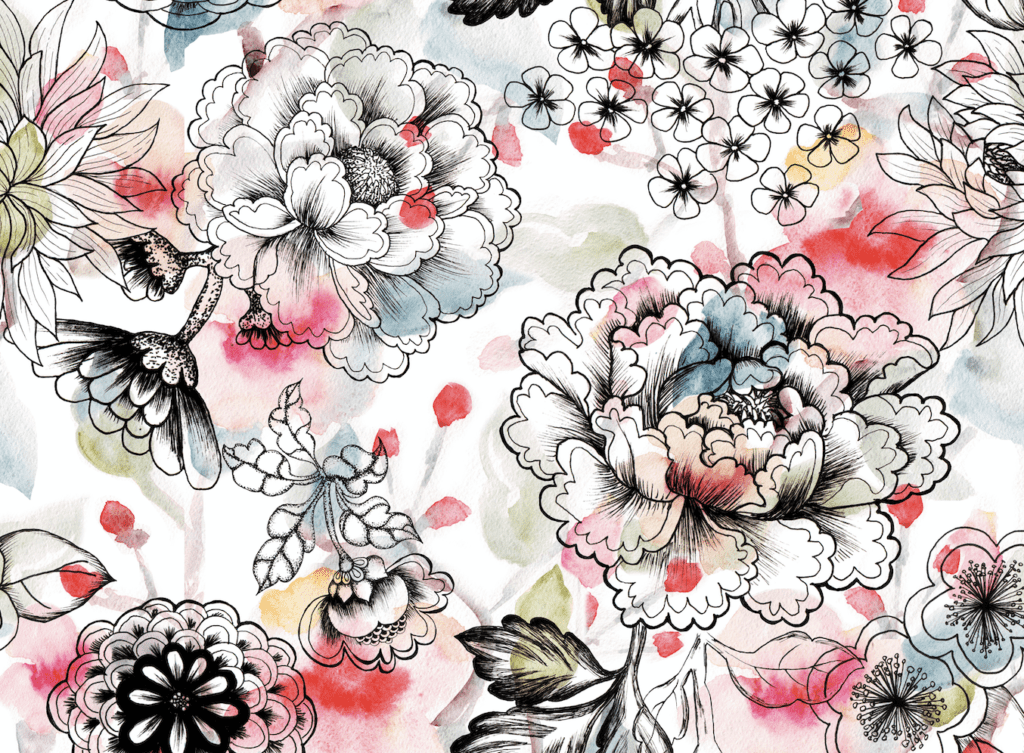
Foresight and thinking for the printing industry
The printing technology exchange is new every year’ with frequent academic activities. The printing experience and achievements from all over the country. This has led to the continuous improvement of the printing industry in China. In the past three years, the technical equipment and technology of China’s printing industry have been greatly improved, and the technical progress has never been so remarkable. Printing trend of instantaneous information feedback is still very weak. These are anxiously waiting for printing counterparts to redouble their efforts.
Printed fabric is the link between the upper yarn weave and the lower garment, to Better role in carrying on
The pattern of a printed fabric is the essence of a floral fabric. A good pattern can attract many consumers, which is good for promotion and increases revenue. This was true in the days of the planned economy. Many of the best patterns, such as the first stroke, the Rubik’s cube and the bamboo leaf, launched the market. They were sold well and led to the revival of a print factory. This was still the case in the market economy, as in the case of the APEC International Economic Forum in Shanghai in 2001. For example, at the 2001 APEC International Economic Forum in Shanghai, the Shanghai clothing research department designed a Tang suit for the heads of the conference with a flower pattern, reflecting both the national style and the spirit of the times, which was much appreciated by the VIPs and people from home and abroad. It was very popular for a while, although it didn’t last long, but it shows that patterns need to be both timely and innovative.
The event was held in Shanghai Mart in August 2005 and was a platform to showcase outstanding printed fabrics and to conduct trade activities, as well as a platform for apparel designers and pattern designers to communicate and discuss their ideas. It is also a platform for apparel designers and pattern designers to exchange information and ideas. Even the weaving designers of grey fabrics form a tight upstream and downstream chain from raw fibres to weaving and dyeing. Printed fabrics really become the link between the top and the bottom, between the weaving and the garment industry. It is hoped that the printed fabric will be tailored to the style and use of the garment. The final product is the leader, forming a whole design chain for the final garment, creating a famous brand and creating a brand name. We hope that this platform will also be a salon for pattern designers for printing, and that through this channel and platform we will revive the glory of pattern design. At the same time, we also want to discuss the way of independent design for pattern design in China, and gradually get rid of the situation of relying on foreign patterns°.
Focus on new digital technology research and development to promote another leap in printing technology
Digital inkjet printing is a combination of computer, information technology. It is a new technology that integrates computer, information technology, precision machinery and fine chemicals, which is conducive to energy saving, consumption reduction, environmental protection and fast delivery. In recent years, the industry has gained a better understanding of it. Although there is still low operational efficiency. High costs. But after all, it has individual characteristics. If multiple machines are used in combination, they still have certain advantages. Recently, printing factories around the world have also become aware of this. In fact, some foreign printers are also following this path of cluster production. Some foreign R & D departments are still continuing their efforts to improve the speed of digital inkjet printing, and at the same time are working on digital electrostatic printing technology ‘the United States, Japan and other countries continue to report on this, the use of electrostatic mechanism, but the use of different technical routes, so the choice of colour developer is not the same. The US produces a negative charge on the surface of the toner cartridge, while Japan produces a positive charge on the surface of the toner cartridge. This is why the properties of the colour developers used in both countries are different. The composition and manufacturing methods are also different. China has not had much contact with digital electrostatic printing technology, so we need to keep an eye on the principles and colour rendering agents and keep abreast of foreign developments and the latest information in order to grasp the path of independent innovation. But at the same time do not give up the advantages of the shortcut. Digital electrostatic printing technology abroad is still in the prototype test stage of development, for China is also an opportunity to catch up, to ensure that this new technology can be recognized and attention from all sides.
Digital inkjet printing technology will be the future direction of development and has been gradually recognized by most printing and dyeing factories. Today, the slow printing speed and high price of printing ink This has affected the expansion. Due to the involvement of microelectronics and fine chemicals. This new technology is progressing at an alarming rate, and many well-known international manufacturers have become involved in inkjet printing machines and ink printing technology, especially some multinational dye giants. Such as Swiss ± Ciba, the United States DuP “nt (DuPont), Germany Bayer (Bayer), Herst (Herst), Japan Mitsubishi Chemical (Mitsubishi Chemical), etc., have developed their own series of ink, some will also be developed with the inkjet printing machine companies supporting special ink. Some of our research institutions. In the international seizure of this new technology territory, also spared no effort to participate in the competition. In the “Tenth Five-Year Plan” national key scientific and technological research project “new technology development of digital ink-jet printing of fabrics”, there are Shenyang Research Institute of Chemical Industry, Zhejiang Silk Research Institute, Soochow University, East China University of Science and Technology, etc. have declared the development and application of ink-jet printing ink system projects. After three years of research, the project successfully developed a nano pigment ink for inkjet printing of textile maggots with China’s own intellectual property rights. This is a happy event for the printing industry in China, and we hope to further accelerate the industrialisation process. We hope to further accelerate the industrialisation process and make new contributions to the promotion and application of digital ink-jet printing technology for textiles in China.
In short, the new inkjet printing technology in the international development time is not long, but also in the continuous improvement and improvement, one is how to improve the efficiency of inkjet printing machine. Nozzle how to extend the service life; the second is how to improve the quality of ink and its curing technology; the third is how to configure and fabric matching before and after the treatment process and equipment, but also to meet the environmental requirements. These are to seriously study the solution, the development and application of China’s new inkjet printing technology to shorten the gap between and international. 2.3 special printing is a reflection of the progress of printing technology, is also the inevitable trend of printing development
In 2004, the Dyeing and Finishing Committee of the Chinese Society of Textile Engineering successfully held the “International Symposium on Application of Coatings and Special Printing” in Shanghai. This was a continuation of the International Symposium on Coatings Application held in Shenzhen in 199. The continuous development of printing technology has resulted in a wide range of special printed fabrics with high-tech materials and a variety of special features for viewing, touching and smelling. This enriches the quality of life and meets the specific needs of each act. Special printing meets the needs of the elbow generation and the need to improve the value of the order, it reflects the progress of printing technology, is the inevitable trend of today’s printing process technology.
If some special treatment is used. If special treatments are applied, the finished fabric can be made water and oil repellent as well as breathable and breathable, e.g. lamination: laminated porous films; partial dissolution of coating materials: coated films are composed of components containing dissolved components, which are extracted after drying. These methods can be used to achieve water and oil repellency, breathability and moisture permeability in the finished fabric. These methods can be used to achieve a water and oil repellent finish for silk.
Chemical grafting
Silk fibres have many reactive groups (e.g. mono-OH, mono-NH], etc.). They can react with alkene monomer compounds containing hydrophobic groups. The hydrophobic groups are covalently bonded to the fibres to increase the hydrophobicity of the fibres. The use of chemical grafting to improve the water and oil repellency of silk fabrics is an ideal method.
The grafting of vinyl oxides onto silk by irradiation initiation has been reported overseas to improve the water and oil repellency of silk fabrics, and the acylation of silk fibres with dodecyl or octadecyl succinic acid vinegar (ODSA or ODSA) in a solvent medium (e.g. DMF, DMSO, etc.) by AraiT et al. to give the egg white fibres long hydrocarbon chains. The water repellency of the silk fibres is improved. The grafting modification is not uniform at high grafting rates, but has good water repellency when the grafting rate is controlled at 3 % – 6 %. The grafting of the silk fibres has no effect on the properties of the fibres themselves. In addition, water can be used as the reaction medium and hydrophobic monomers can be grafted onto silk fibres by phase transfer using a pre-emulsification process to improve the water and oil repellency of the silk fabric.
Chemical grafting of fibres for water- and oil-repellent finishes has been the subject of interest and research, but there has been no large-scale industrial application or problem with the process of scaling up the reaction between fibres and hydrophobic finishes, and how to make the grafting reaction as fast and workable as possible. If the process and equipment problems are solved, then similar grafting methods, including grafting with active agents containing fluorinated hydrophobic and oleophobic groups, would be a simple and straightforward way to treat fibres for water and oil repellency.
2.4 Nanotechnology
Research into nanomaterials began in the 1960s and research into the use of nanotechnology for water and oil repellent finishing of fabrics is just beginning.
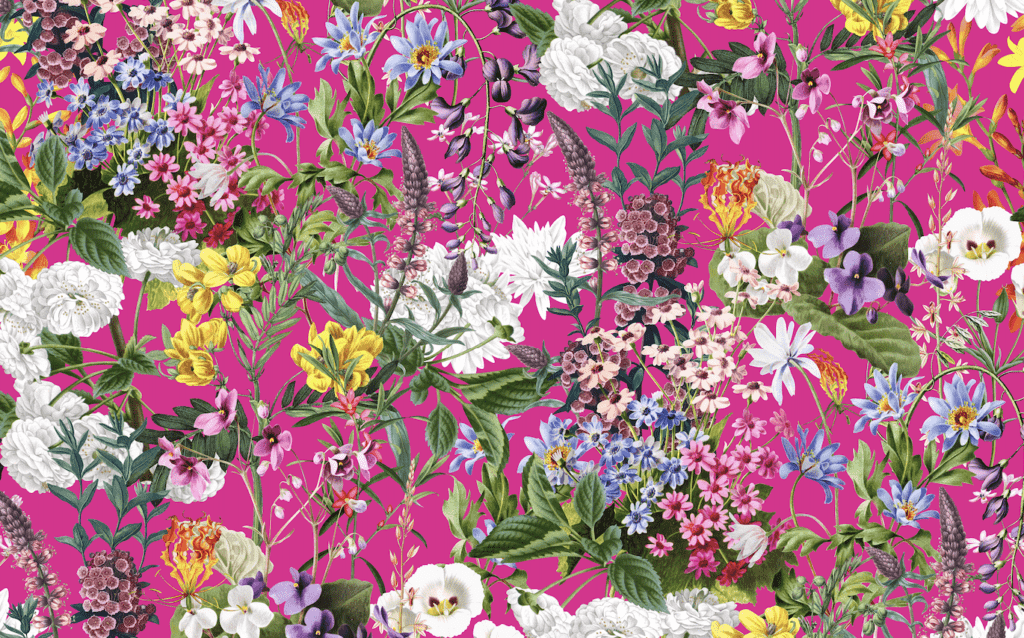
Conclusion
Silk fabric water and oil repellent finishing in China is still in the initial stage. At present, fluorinated finishes with superior water and oil repellency, such as Sri Proof WORF, AG- 915, 925, 950, etc., are still dependent on imports, and it is necessary to speed up the development of gas-carbonated finishes with superior performance in China. And continue to reduce costs. At the same time should strengthen the chemical grafting modification and nano-modification research.
Currently. Fluorinated fabric finishes are combined with other lower cost water and oil repellent finishes to reduce costs and improve performance. The popularity of fluorinated finishes will be greatly enhanced. At the same time, the research on the combination of fluorinated finishing agents with other finishing agents (such as non-iron resin) is of great significance for the development of new multifunctional products. Research on the combined efficiency of each auxiliary has become an important research direc