6 Factors in production processes
Pre-treatment
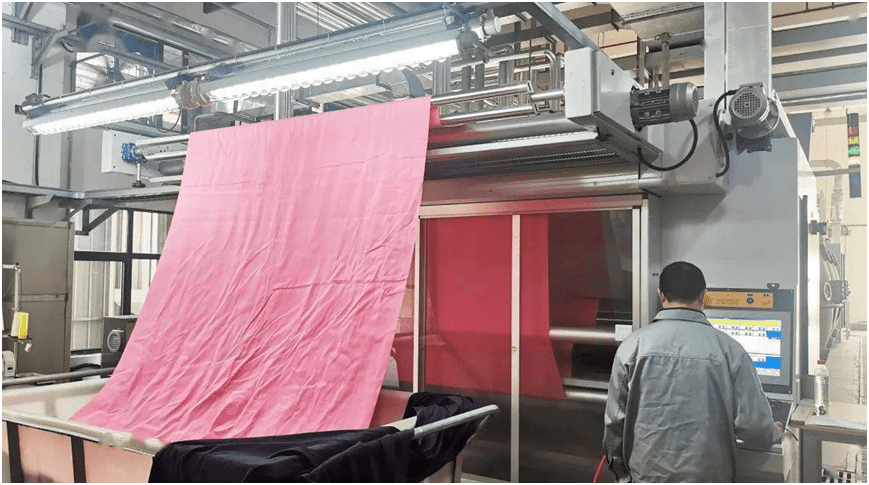
Uniformity in pre-treatment is necessary to prepare for the control of colour differences. If the pre-treatment does not meet the requirements, it is difficult to achieve the desired effect in the subsequent processing. Therefore, it is important to start with the pre-treatment to control colour differences.
Turning the head of the cloth
The same fabric carriage requires the same specification, the same manufacturer and the same batch of blanks to be sewn together. If the list is too small and different batches of cloth need to be carpooled, they must be well marked so that they can be distinguished in the subsequent process.
Burnt wool
Blank fabric stock generally contains a large amount of chemical slurry, if the speed of the car is fast and slow, or the fire opening is not uniform, the fabric surface is not flat when the fabric passes through the fire opening, which will lead to uneven desizing and cause colour differences. Therefore, the burning speed should be consistent, the fabric surface is flat and the fire opening is even.
Practice bleaching
When boiling, the amount of caustic soda and auxiliaries should be strictly controlled, and the process conditions such as steam time, temperature, roll residual rate and water washing should be stable. After cooking, peroxide bleaching should be fully washed to prevent residual peroxide. The drying drop cloth width is consistent and contains the same moisture.
Mercerisation
Strictly control the speed and concentration of caustic soda, and test the wool effect and barium value after the cloth is dropped. The difference in dampness of mercerised fabrics should not be too great, especially for some heavy fabrics. This is because uneven dampness on the fabric surface can lead to inconsistent mercerising effects and make a difference to the printing effect. Cotton fibres are fully mercerised, the affinity of the dye to the fibres increases, it is not easy to migrate with the moisture after adsorption, and covalent bonding with the fibres occurs during the steam process, making the fabric surface deep and full of even colour.
Brushing
The abrasive effect should be even and consistent. It is not recommended that the sanding is too coarse, preferably above 280 mesh. During the grinding process, the tension and speed should be uniform and the abrasive should be changed frequently. If the grinding time is too long, the roughness of the sanding surface will be reduced and the effect of grinding will decrease. Uneven grinding can also lead to inconsistencies in the colour of the print, resulting in colour differences.
6 factors in printing prescriptions and process
Dyes
The reactivity of the dyestuff chosen for printing should be moderate and similar. If the reactivity is too strong, the stability of the paste will not be good, especially in the summer, and the colour of the paste will drop significantly as the storage time increases; if the reactivity is too weak, the dyestuff will not react sufficiently during the steam process, and fluctuations in the process conditions will produce significant colour differences. When colour matching, the reactivity of dyestuffs in the same prescription should be as close as possible so that there are no significant colour changes due to fluctuations in process conditions.
Avoid colour matching with dyes that are pH sensitive. For example, C.L. reactive black 8 (domestic reactive black K-BR, Texta’s reactive black PX-N black) and P-SG black are very pH-sensitive, with a reddish tint under acidic conditions and a greenish tint under neutral and weakly alkaline conditions. The use of these dyes can easily lead to significant colour differences due to small fluctuations in the pH of the fabric.
Some dyes are more sensitive to humidity during steam, such as KN-B black. When the relative humidity is 30 to 100%, the amount of colour obtained decreases as the humidity increases. Other types of dyestuff, such as P-SG black, have very little variation in the amount of colour obtained within a relative humidity range of 80-96%.
Colour blocking using non-contrasting dyes, such as Huntsman’s Nc-type reactive dye combinations. The dyestuff chosen should have good fastness, especially to washing, otherwise the degree of residual floating colour on the fabric surface will be inconsistent with fluctuations in washing conditions after printing, again causing colour differences.
Sodium alginate
If the sodium alginate slurry contains Ca2+, it can combine with the carboxyl group in the sodium alginate molecule to reduce its electronegativity, weakening the electrostatic repulsion between the sodium alginate and the dye molecule, resulting in the carboxyl group in the sodium alginate molecule reacting with the dye, reducing the amount of reactive dyes on the cotton fabric, and causing colour differences due to the instability of the colour given. If a starch slurry is included, the hydroxyl group of the starch can also react with the reactive dyestuff and reduce the colour yield. Therefore, in order to obtain a high and stable colour fixation rate, a good quality sodium alginate should be used.
Alkali
Alkalis provide the optimum pH for the reaction between the reactive dyestuff and the fibres during the steam process. The type of alkali and the amount of alkali used should be chosen according to the reactivity of the dyestuff. If the alkali is too strong, some reactive dyestuffs will have poor storage stability and will hydrolyse prematurely; if the alkali is not sufficient, some poorly reactive dyestuffs will not be sufficiently fixed on the fibres, which will also result in wastage of dyestuff and produce colour differences.
Anti-dye salt S
Anti-dyeing salt S is a weak oxidising agent which prevents the dyestuff from being damaged by reductive substances during drying and steaming. If the amount of salt used is too small, it will not prevent the dyestuff from being damaged by reductive substances, resulting in colour differences; if the amount used is too large, some dyestuffs that are not resistant to oxidation will also change colour, for example vinylsulphone-type reactive brilliant blue dyestuff, which will become darker and less vivid.
Urea
Urea is used in the printing process as a moisture absorber and solubiliser. However, at high temperatures it reacts with the vinylsulphone reactive group and consumes part of the alkali agent. For some dyes containing vinylsulfone reactive group, the amount of urea should be as low as possible; for dyes without vinylsulfone reactive group with low solubility, the amount should be increased appropriately. Too high or too low a dosage of urea will make the colour of the print unstable and lead to colour differences.
Sodium Hexametaphosphate
The main function of sodium hexametaphosphate is to complex the calcium and magnesium ions in the colour paste. If the water quality of the printing and dyeing plant is hard, or the calcium ion content of sodium alginate is high, sodium hexametaphosphate can be added to avoid the combination of calcium and magnesium ions with sodium alginate to reduce the colour yield, resulting in colour difference.
2 factors in the print process
Steaming
Drying: The drying before steaming should be even after printing. If the fabric surface contains different dampness, this will inevitably lead to differences in temperature and humidity when steaming, resulting in colour differences.
Steaming time: Steaming time depends on the properties of the dyestuff. Different dyestuffs have different reactivity and require different steaming times. Dyestuffs that are highly reactive, such as those containing vinylsulphone reactive groups, can be steamed for too long, resulting in a reduction in colour yield and a change in colour phase. Likewise, if the steam time is insufficient for less reactive dyestuffs, the dyestuff will not react sufficiently with the fibres, which will also cause colour differences.
Steaming temperature: The steaming temperature is generally controlled at 101-103°C and should not fluctuate too much.
Steaming humidity: for most dyestuffs, the relative humidity is controlled at 90-95% to achieve a stable and high colour yield. Individual reactive dyes, such as reactive black KN-B, are more affected by steam humidity, relative humidity is 30 ~ 110%, with steam humidity increases, the amount of dye colour is gradually reduced.
Therefore, the use of this dye should be avoided as far as possible in reactive printing. If it must be used, the humidity should be strictly controlled within a reasonable range when steaming to avoid colour differences.
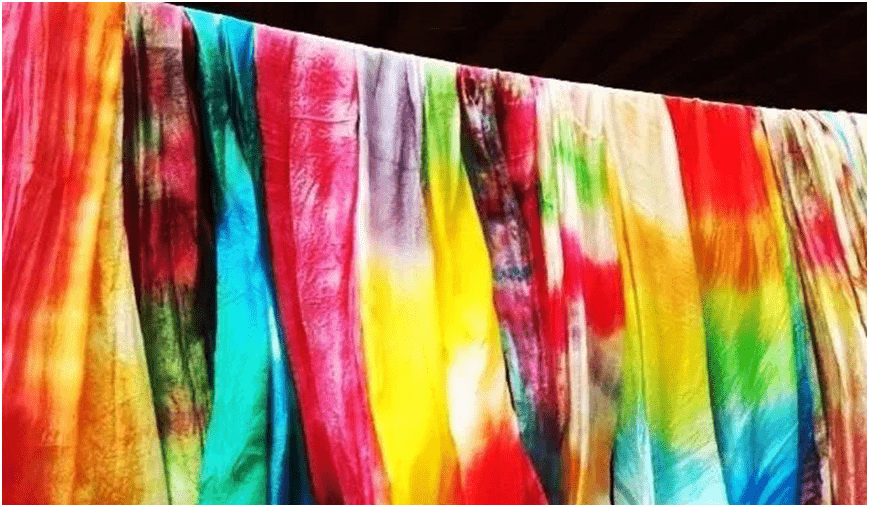
Washing
After steaming, the fabric should be washed to remove the unconsolidated dyes.
Adequate removal of floating colours: some dyes such as reactive emerald blue have poor fastness and low fixation rates. Inadequate washing can lead to residual floating colours, which can affect both the colour fastness of the finished product and lead to colour differences. Removal of staining during washing: dark colours stain lighter colours differently, which can also lead to colour differences. The same flower type, flower colour has dark and shallow, dark colour when washing more dye off, if its affinity for the phase of the fibre is greater, but also re-stain the cotton fabric, stain the white background or light colour flower colour, especially for some sensitive colours, discolouration is very obvious. In order to avoid the colour difference caused by washing, washing to add anti-staining agent, while washing tank to change the water in time.
4 factor in Finishing Processes
After printing and washing, the reaction between the dye and the fibre is basically complete, however, colour differences can still occur during the finishing. It is therefore necessary to analyse some of the common colour changes caused by finishing in order to effectively control colour differences.
Acids
When finishing the finished product, the pH of the fabric is adjusted to a weak acid to neutral, commonly used are citric acid, formic acid and acetic acid. The addition of acids can have an effect on the dyestuff, and improper control can also cause colour differences.
Citric acid is a ternary acid and also has a chelating effect, which can change the colour and light of some reactive dyes containing metal ions more significantly. Citric acid also has a reducing effect under light conditions and can have a damaging effect on the chromophore of the dye.
Formic acid contains aldehyde groups, which are reductive and, under certain conditions, can also damage the chromophores of dyestuffs, leading to aberrant colour changes.
Acetic acid has a less pronounced effect on the colour light than citric acid and formic acid, and it is recommended to adjust the pH of the fabric with acetic acid. It is recommended to adjust the pH of the fabric with acetic acid. During use, attention should be paid to the volatility of acetic acid and the odour of the fabric.
Colour changes caused by fixing agents
Commonly used fixing agents can cause colour changes in printed fabrics to a greater or lesser extent. In particular, incomplete reaction of dicyandiamide in fixing agents can cause significant colour changes in some azo dyes at certain pH and high temperatures. The type of fixative, dyestuff and process conditions are different and produce different colour changes. In practice, it is important to find effective measures to control the colour change after trials and large scale production verification to avoid colour differences.
Colour change of some dark blue and navy dyes caused by formaldehyde
In resin finishing, some auxiliaries release formaldehyde, which can chemically combine with the H acid double azo group of dark blue and navy blue dyes, causing a change in the colouring body.
This is the reason why some dark blue or black varieties have an obvious reddish colour after resin finishing. When operating, try to control the drying and baking temperatures. If possible, resin finishing patterns should be avoided by using such dyes for colour blocking printing. If this cannot be avoided, strict control should be exercised over the moisture content of the fabric, pH value, baking temperature and time to ensure a consistent degree of colour change. When printing colour matching, resin finishing of the colour samples should be compared with the standard samples to ensure that the colour of the finished product meets the standard.
Colour change in flame retardant finishes
In the Proban/ammonia flame retardant process, the fabric goes through a process of dipping and rolling the flame retardant finishing solution, drying, ammonia fuming, oxidation and washing. The flame retardant finishing solution is highly reductive and it is easy to destroy the molecular structure of some azo dyes when drying; in the oxidation process, some fuels have a limited degree of tolerance and will also produce colour changes; the formaldehyde release of flame retardants is more serious and there is also the problem of formaldehyde discolouration. As dyestuffs produce complex transformations throughout the flame retardant process, fluctuations in process conditions can easily cause colour differences. Therefore, for fabrics that need flame retardant finishing, the dyestuffs used for printing should be strictly screened to avoid some sensitive dyestuff colour matching, such as reactive blue 194, reactive black 5, etc. At the same time, each part of the flame retardant process should be strictly controlled to prevent colour differences due to unstable process conditions. Special attention needs to be paid to the moisture content of the fabric after drying and rolling the flame retardant. The different moisture content of the fabric has a particularly obvious effect on the colour and light.
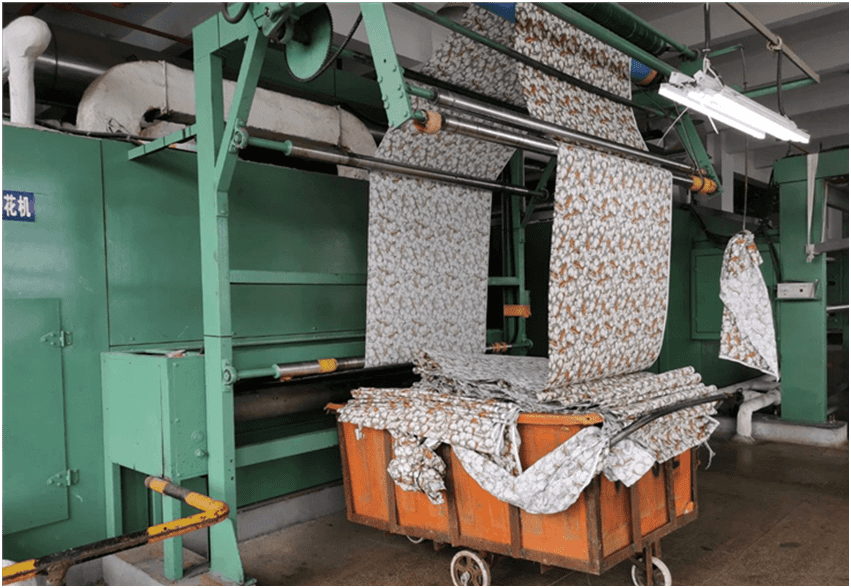