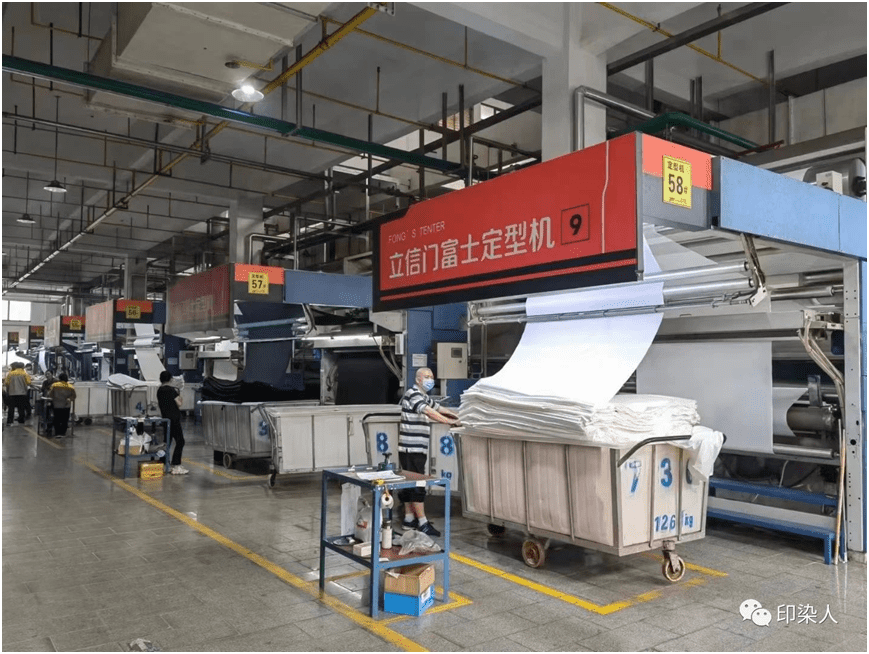
Usually, the pre-treatment, dyeing, printing and finishing processes are all carried out in the same dyeing and finishing factory. The pre-treatment, dyeing, printing and finishing processes are carried out independently of each other, where the pre-treatment and finishing processes have an important significance on the dyeing and printing effect of the fabric, as well as the handfeel and style of the fabric formed in the end.
In addition to the fabric taking performance with the fiber, yarn, fabric structure and other factors, but also with the fabric dyeing and finishing processing technology level is closely related. The dyeing and finishing technology of fabrics or garments is an important means to improve the grade and added value of products, and the level of dyeing and finishing technology is a comprehensive reflection of a country’s textile processing level.
The main trends and priorities in the development of dyeing and finishing technology are
① products using raw materials development, weaving, dyeing combined in a one-stop way, the development of completely new textile fabrics, such as new combined fiber products, Tencel textile products, new nylon, acetate products, etc.
② Further improve the appearance and style of the fabric, taking performance, give the fabric comfortable, leisure, beautiful, easy to maintain a variety of properties, improve the added value of the fabric. Functional finishing of fabrics to give special performance.
③Research on less polluting and energy-saving textile processing technology with ecological and environmental protection concepts, focusing on the ecological balance of each link of the whole production process.
Usually the object of finishing can be fibres, yarns, fabrics and garments, with the most amount of fabric dyeing and finishing processing. Although the processing objects are different, their purpose and principles are basically the same. This chapter introduces pre-treatment, dyeing, printing and finishing in order. Pre-treatment of fabrics
Before dyeing and finishing the cloth should be pre-treated to remove the fabric fibre hindering the dyeing of hair and impurities, improve the whiteness of the product, but also to ensure that its dyeing, printing product colour purity, brightness and colour fastness. Pre-treatment process generally includes thermal characterisation, burning, desizing, boiling, bleaching, etc., cotton textiles also have to go through mercerisation process. The pre-treatment of fabrics is the first process that needs to be carried out before dyeing, printing or finishing. By the strict definition of finishing, pre-treatment is not part of textile finishing, as it is carried out before dyeing and printing. However, many experts see pre-treatment as a basic finishing and many specialist books often include pre-treatment in the finishing process.
In heat setting, when the heating temperature exceeds the glassy temperature of the fibres, the molecules in the amorphous zone start to move and it is possible for the fibrous material to change shape in response to external forces, when the temperature is lowered the textile will retain that shape. Heat setting stabilises the shrinkage, deformation and creasing of the raw material.
Desizing is not only used to remove the pulp, but also to remove some of the natural impurities from the original fabric for later cooking and bleaching processes. The desizing of the fabric can be based on the original cloth containing impurities and the requirements of the desizing, using different methods, such as enzyme desizing, alkali desizing, acid desizing, oxidant desizing, etc.
Boiled fabric by desizing treatment has removed most of the pulp and part of the natural impurities and oil agent, but most of the natural impurities such as waxy substances, pectin substances, nitrogenous substances and part of the oil agent and other people residue in the fabric, will certainly affect the future printing and dyeing processing. In order to make the fabric with certain water absorption, to facilitate the dyeing process in the adsorption, diffusion, the need to fabric in a concentrated alkali solution for a certain period of time boiling, in order to remove the above impurities.
Bleached fabric by boiling, there are natural pigments on the fibres, its appearance is not yet white, used for printing and dyeing, will affect the brightness of the colour. The purpose of bleaching is to make the impurities fade, so that the fabric presents natural white, and the fibres themselves are not significantly damaged.
Mercerised cotton textiles are treated with a caustic soda solution under a certain tension to obtain a stable size, a durable lustre and a process that improves the ability to absorb dyes.
Sintering uses a high temperature flame to burn away the lint on the surface of the fabric or yarn. It prevents uneven dyeing or printing defects due to the presence of lint during dyeing and printing. Burning of blended fabrics can be carried out after dyeing to reduce the pilling of the fabric in the process of taking.
Dyeing of fibres and fabrics
Giving textiles their colour and thus successfully integrating them into fashion trends is a field where artistic creativity and scientific technology are combined, usually through dyeing and printing processes. The colour and pattern of the fabric are probably the most important factors in the sales process of a textile product. This is because it is the colour and pattern of the fabric that first attracts the consumer and then the texture and feel of the fabric.
Dyeing is a process in which dyes or pigments are physically or chemically combined with fibres to colour the clothing material or garment. In addition to the requirement for uniform colour, dyed products also require good colour fastness, such as soaping, sunlight and rubbing fastness. Dyeing fastness is mainly determined by the chemical structure of the dye itself, followed by the dyeing method and process conditions.
Classification of dyestuffs
There are many varieties of dyestuffs, and different dyestuffs are suitable for different fibres (see Table 1). Commonly used dyestuffs include direct dyes, reactive dyes, reductive dyes, acid dyes, acid mordant dyes, neutral dyes, cationic dyes, basic dyes, disperse dyes, etc.
Different dyes have different dye fastnesses and dyeing processes, so when choosing dyes it is important to have an understanding of their properties. The following are some of the dyestuffs that are commonly used.
Direct dyes are soluble in water and can be directly dyed on cellulose fibres by boiling in the presence of neutral or weakly basic salts. Direct dyes are easy to use: they are easy to master, inexpensive, have a full colour spectrum and are brightly coloured, but the fastness of the dyeing is not satisfactory and sometimes has to be improved by means of a colour fixing agent. They are currently used in the dyeing of cellulose fibre garments and can also be used for silk dyeing.
Reactive dyes are also known as reactive dyes. It is bonded to the fibre by a chemical bond, so it has good colour fastness, bright colour, good leveling and is easy to use. It is mainly used for dyeing cotton, linen, silk, wool and other fibres. Reactive dyes are available in low-temperature, high-temperature, medium-temperature and woollen types, which need to be selected according to the specific situation when dyeing.
These dyes are insoluble in water and require caustic soda and reducing agents to dissolve them into a silver body before they can be dyed on the fibres, which are then oxidised by air or other oxidising agents before the fibres show their true colour. It has good colour fastness and is resistant to washing and sunlight, but is expensive and cumbersome and is mainly used for dyeing cellulose fibres.
Acid dyes have acidic molecules, are easily soluble in water, have bright colours, have a full colour spectrum and are easy to use. Acid dyes are divided into strong acid, weak acid and neutral dyeing dyes, the first one is mainly used for dyeing wool with poor colour fastness; the latter two are mainly used for dyeing wool, silk, nylon and leather.
Acid mordant dyes are used to dye wool, silk, nylon and leather. They are mainly used for dyeing wool or leather.
Neutral dyes are made by complexing a dye molecule with a metal atom in a 2:1 mixture, known as neutral dyes or metal complex dyes. It can be used to dye wool, nylon and vinyls under neutral conditions with good colour fastness, but the colours are not as vibrant.
Cationic dyes have been developed from earlier basic dyes, which differ from the above in that the pigment ions are cationically charged rather than anionically charged. They are now mainly used for dyeing acrylics and are bright in colour, have good fastness and are particularly resistant to sunlight.
Disperse dyes are non-ionic dyes. These dyes are generally insoluble in water and rely on dispersants to disperse the dye into very fine particles for dyeing. They are mainly used for dyeing polyester and vinyl, but can also be used for dyeing nylon and vinyls. Disperse dyes are available in low-temperature, high-temperature and general-purpose types. Their colour fastness is good, but they are more expensive and special conditions need to be used when dyeing.
In addition to the above conventional dyes, there are also functional dyes, which not only involve light and colour, but also extend to light, electricity, magnetism, photochemistry and biochemistry and other marginal disciplines, and are a class of high-tech materials of modern technology, with a very wide range of applications, and their application in the textile dyeing and finishing process is still in its infancy, mainly in inkjet printing, colour change printing, thermal diffusion transfer printing or electronic photography, and the development Very quickly, its application in the dyeing and finishing process is very promising.
Dyeing methods, which can also be divided into normal temperature and normal pressure bunch dyeing, high temperature and high pressure overflow dyeing, high temperature and high pressure jet dyeing, as well as the supercritical C02 dyeing technology which is currently being devoted to research. Supercritical C02 dyeing technology is a waterless dyeing process with 100% dyeing rate, no pollution and C02 can be recycled. Its technical points and basic principles are: when the pressure exceeds the critical point, C02 has the density of a liquid and the mobility of a gas, becoming a fluid that is neither a liquid nor a gas, but has liquid properties (high density) and gas properties (low viscosity, high diffusivity). Because of its high density, it has the ability to dissolve dyes; its high diffusivity gives it excellent permeability and makes it an ideal dye carrier.
Dyeing process
Dyeing can take place at any stage of the textile manufacturing process and textiles can be dyed at different stages of the process such as fibre, yarn, fabric or garment, depending on the type of fabric or garment being processed.
1. Loose fibre dyeing
Loose fibre dyeing is the process of dyeing fibres or loose fibres before they are spun into yarn. The loose, unspun fibres are generally first put into a large dyeing tank with a dyeing solution and then dyed as if heated to the appropriate temperature. Between 500 and 3000 lbs of fibre can be dyed at one time, averaging about 1000 lbs per dyeing (see Fig. 1).
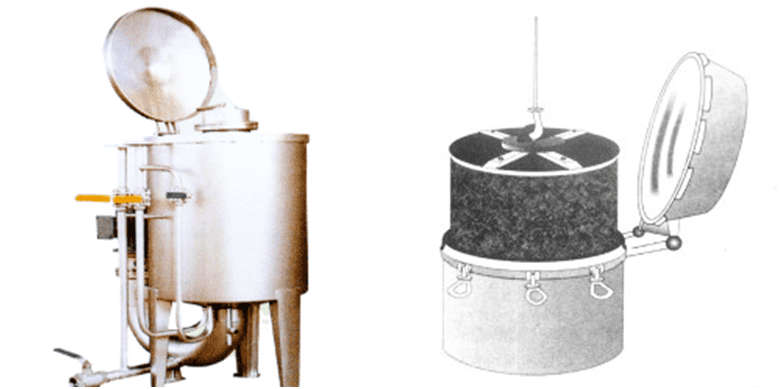
Loose fibre dyeing is mostly used for coarse woollen fabrics when a colour lifting effect is desired. For example, woollen fibres are dyed black and then blended with undyed (white) woollen fibres to produce a soft, mixed grey yarn, also known as linen grey. Tweed fabrics with an ombre effect, such as Helix tweed, are an example of loose fibre dyed materials. Other examples include sesame tweed and worsted tweed.
Strip dyeing
Wool or cotton strip dyeing also belongs to fibre dyeing before the fibres have been spun into yarn and has the same purpose as loose fibre dyeing, i.e. to produce a soft blending effect. The term wool sliver refers to woollen fibres that have been stripped of their short fibres. The sliver is a long fibre that has been selected for use in spinning combed wool yarns. The wool in the form of carded sliver is dyed and blended with other colours of wool to produce the desired blended product. Loose fibre dyeing is not used in worsted textiles because the short fibres are removed from the card sliver production. If all the short and long fibres are dyed before the card is made, then some of the fibres are removed before the wool is made, which results in waste. Some typical wool dyed fabrics include waders, worsted tweeds and clackers (see Figure 2).
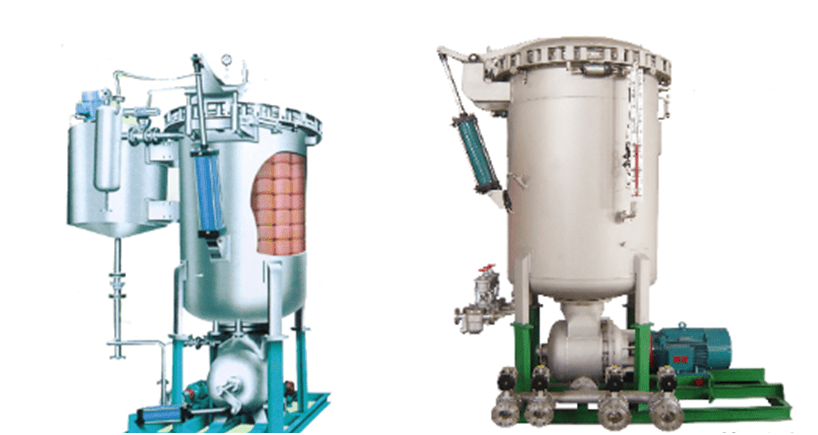
Yarn Dyeing
As the name suggests, yarn dyeing is the dyeing of yarns before they are woven or knitted into fabric. The main reason for yarn dyeing is to give the final product a colourful pattern such as tartan, stripes and chevrons. Some typical coloured fabrics include colourful chevrons, madras shirtings and satin woven knitted fabrics. Yarn dyeing for monochrome fabrics is a special example. Yarns can be dyed in different forms, such as stranded yarns, tube yarns or warp dyeing.
1) Twisted yarn dyeing
Strand dyeing involves impregnating large, loose stranded yarns into a specially designed dye bath for this purpose. Soft, fluffy yarns such as hand-knitted fleece are often dyed in stranded yarns. Strand dyeing is the most costly method of yarn dyeing.
Strand dyeing
Strand dyeing is the impregnation of large, loose stranded yarns into specially designed dyeing vats for this purpose. Soft, fluffy yarns such as hand-knitted fleece are often dyed in stranded yarns. Strand dyeing is the most costly method of yarn dyeing.
Tube Yarn Dyeing
In tube yarn dyeing, about 1 lb. of yarn is wound on a small perforated tube or tube called a barrel. A number of tubes are loaded into the dyeing machine and the dyeing solution flows through the machine, alternately circulating from the centre to the outside and then from the outside to the centre again (see Figure 4). Yarns dyed with cylinder yarns do not retain as much softness and fluffiness as those dyed with stranded yarns. However this dyeing method is satisfactory and is very widely used for dyeing most types of yarn in knitted and woven fabrics.
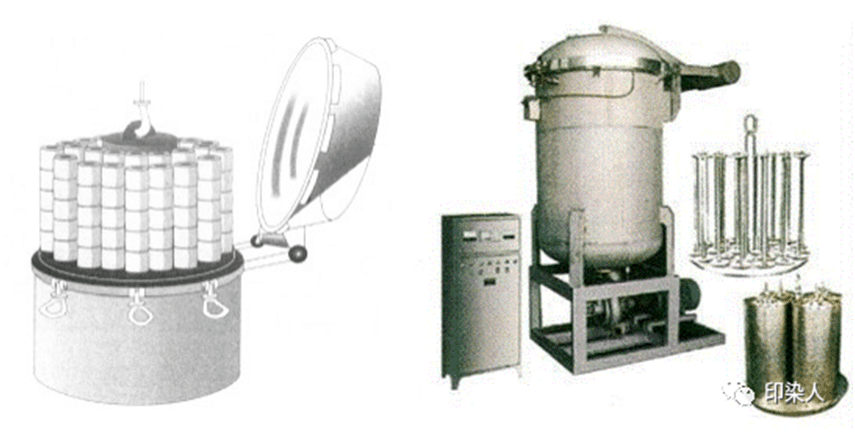
Warp dyeing
Warp beam dyeing is a type of large-scale reel dyeing. A whole warp yarn is wound on a warp beam with perforated rollers and put into a warp beam dyeing machine, in which the dyeing liquor circulates in the same way as in the case of cylinder yarn dyeing. Warp beam dyeing is more economical than stranded and cylinder yarns, but it is only suitable for the dyeing of woven fabrics, i.e. a whole roll of warp yarn. Knitted fabrics are mostly dyed in cylinder colours and are therefore not suitable for warp dyeing.
Pitch Dyeing
The dyeing of woven or knitted fabrics is called pique dyeing and is one of the most common dyeing methods. Rope dyeing, jet dyeing, roll dyeing, roll dyeing and warp dyeing are some of the methods utilised, each of which is described in the following sections, together with its operation.
When dyeing heavy or tightly woven fabrics, as well as fabrics with strongly twisted yarns, the dye sometimes does not penetrate into the centre of the yarn, a condition known as poor penetration, which leaves the fibres in the centre of the yarn or in the interweaving of the fabric lightly coloured or uncoloured. To identify this phenomenon, remove some yarns from the fabric, untwist them and observe the uneven hue of the fibres in the untwisted yarns. When these fabrics are relatively new, they are not a problem. However, after a period of wear, fabrics such as uniforms, children’s clothing, decorative fabrics and other fabrics that have been used intensively will fade at the point of wear and the white, undyed fibres will migrate to the surface of the fabric. For this reason, many high-quality, heavy and tightly woven fabrics, especially furniture covers, are yarn dyed even if they are monochrome. Yarn dyeing, although more costly, eliminates the problem of poor dye penetration.
Rope dyeing Rope dyeing is also known as dye bath dyeing. When dyeing, the heads and tails of the fabric are sewn together, bringing the total length to around 1000 yards. The rope fabric is dyed under loose (tension-free) conditions and retains most of the original fabric. The soft feel and fullness of the fabric is retained. This method is used for knitted fabrics, coarse woollen fabrics and worsted woven fabrics, as well as fabrics with special textures (see Fig. 5).
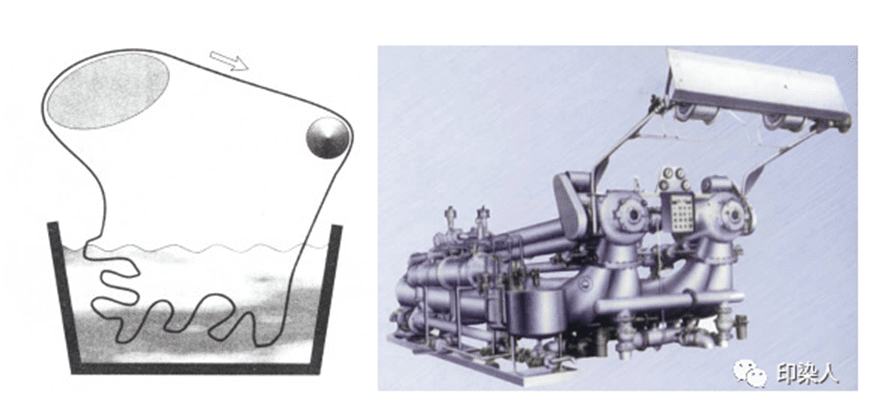
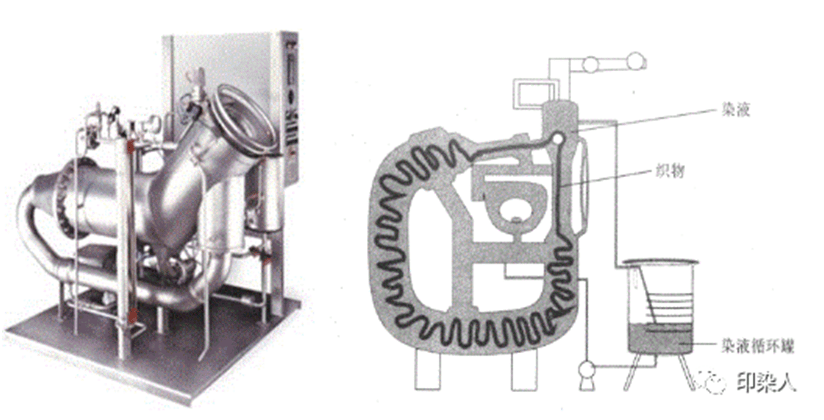
Jet Dyeing
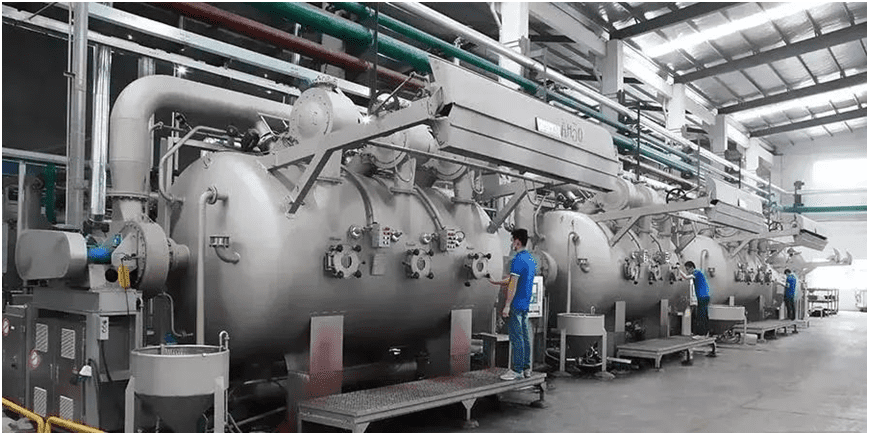
Jet dyeing is somewhat similar to rope dyeing. Only the fabric to be dyed needs to be circulated (or agitated, see Fig. 6) through the dyeing machine under the jets of the dye bath. Most jet dyeing machines can be pressurised and can achieve dyeing temperatures above the boiling point of water. Jet dyeing is superior to rope dyeing because it consumes much less water, energy and chemicals and has a shorter dyeing cycle, and it also has a small dye bath ratio. Jet dyeing machines have a capacity of approximately 1400 lbs. As a dyeing method, jet dyeing has replaced rope dyeing in large numbers.
Roll dyeing
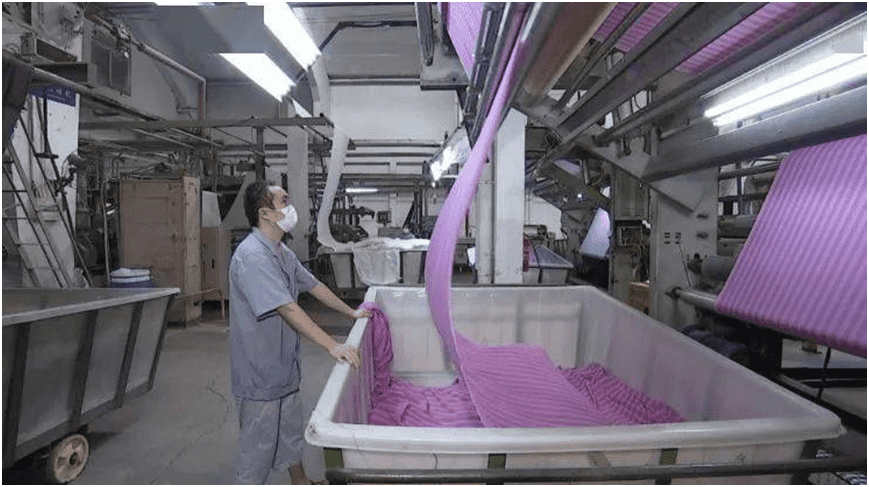
The roll dyeing process is a flat treatment of the fabric, which is not diffused in the dyeing process for a long time, but is drawn through the dye bath by the machine. After the first complete pass, the fabric runs in reverse and passes through the dye bath again (see Fig. 7).
As the fabric is wound between the two rollers, the rollers apply tension to the fabric, which makes the fabric flatter but less pleasant to the touch.
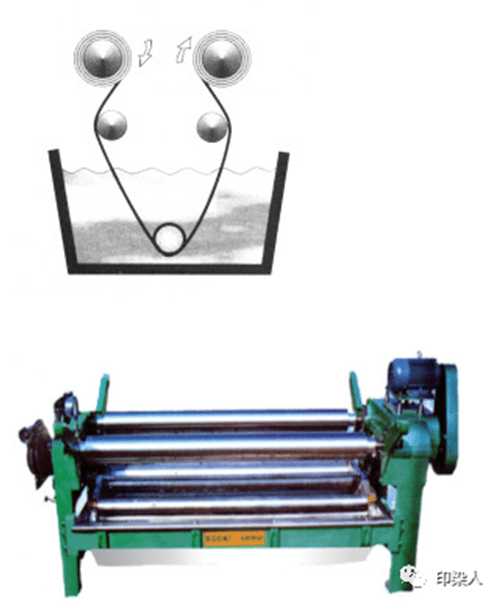
Roll dyeing is more economical than rope dyeing or jet dyeing, and most lining fabrics and many other light fabrics such as taffeta and twill soft fabrics are usually roll dyed, but not fabrics that are too light or where the fabric tissue could be damaged by the tension generated by the roll dyeing machine. Knitted and stretch woven fabrics cannot be roll dyed because the tension generated by the roll dyeing will stretch the fabric and distort it.
Roll dyed fabrics sometimes have a slight colour difference from body to edge or head to tail. This is usually due to the uneven tension created by the roll dyeing machine on the fabric. This type of defect on roll dyed fabrics must be carefully checked.
Roll dyeing
Dyeing is carried out by a dyeing machine called a dye-roller: the dyeing machine is shaped somewhat like a giant clothes dryer (with 12-inch diameter rollers). The fabric is first passed through the dye bath in a flat pattern and then through the rollers, where the dye is squeezed into the fabric.
Roll dyeing is like roll dyeing in that tension is created as the fabric passes through the rollers, which causes the fabric to be flattened but with a poorer feel (see Figure 8).
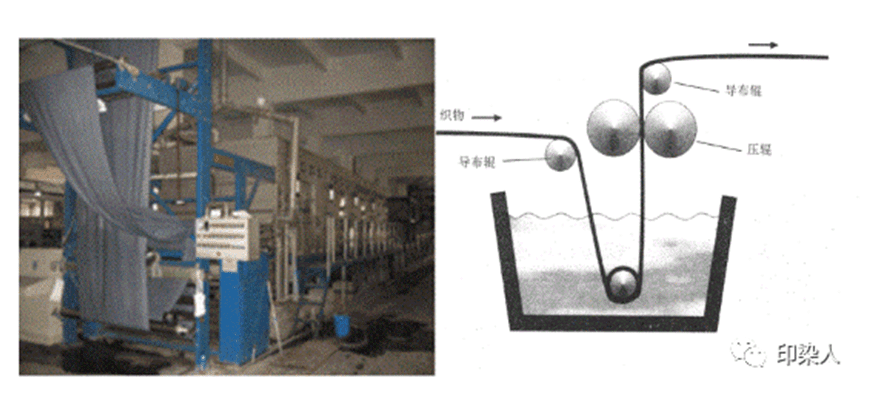
Most of the rolling is done as part of a continuous dyeing system or continuous dyeing plant, where large quantities of fabric, sometimes a million yards, pass continuously through the rolling machine, into the heating or steam chamber (where the dye is fixed) and through the washers, rinsers and ovens. The final presentation is the fully dyed fabric.
Warp dyeing
Warp dyeing of piqué is practically the same as warp dyeing of yarn. This process is used to dye light, loosely structured fabrics because the dyeing solution cannot circulate through the tightly structured fabric on the entire warp beam. Trico warp-knitted fabrics are the fabrics that are usually warp-dyed. Warp beam dyeing is a fast and economical method for dyeing light, thin and loose fabrics. Furthermore, warp-dyed fabrics are not as susceptible to stress and tension as roll-dyed and roll-dyed fabrics. Approximately 10,000 yards or 4,000 lbs of fabric can be wound on a warp beam and placed in the dye bath (see Figure 9).
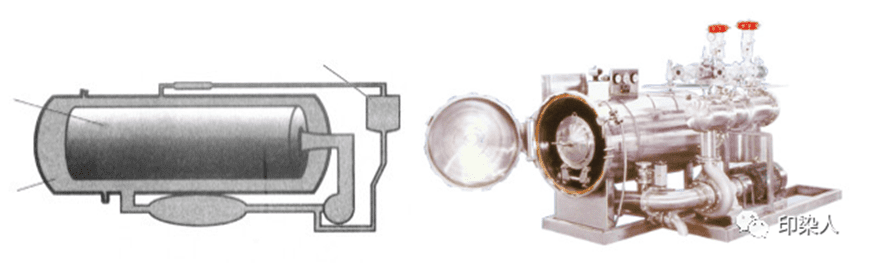
Garment Dyeing
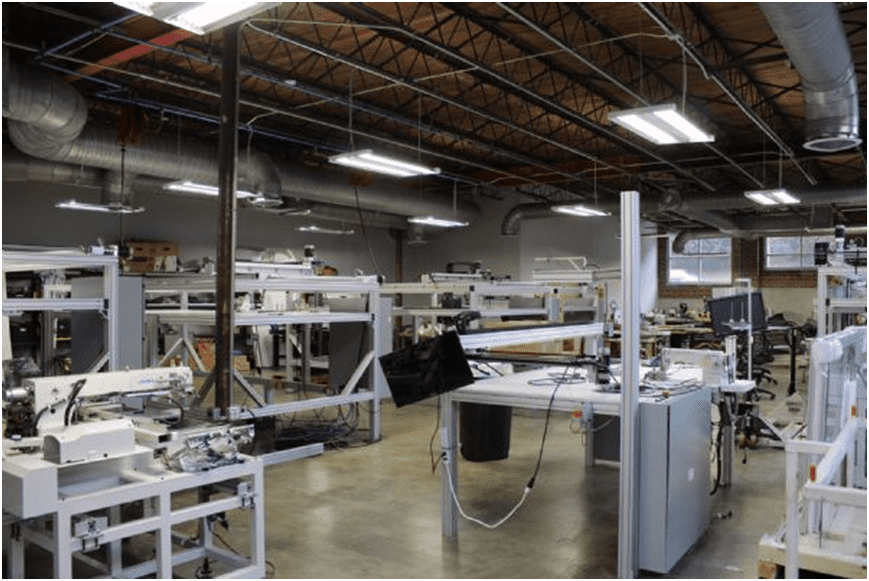
Garment dyeing is the dyeing of entire garments. The majority of garment types that can be dyed are non-cut garments, such as knitted pullovers, round-necked long-sleeved sweatshirts, coarse twill skirts, coarse twill jackets, knitwear and pantyhose. Tailored garments, such as wish suits or dresses, cannot be dyed as garments because the different shrinkage properties of the different components and linings can distort and distort the whole garment.
Garment dyeing involves taking a suitable amount of garments (usually about 24 sweatshirts or clothes of considerable weight), putting them into a large nylon mesh bag (see Fig. 10), which are to be loosely packed, putting 10 to 50 of these packs into a huge dye bath containing a dyeing bath and continuously agitating the garments by means of paddles driven by an electric motor in the dye extraction tank. The machine is therefore called a paddle dyeing machine.
Garment dyeing is the dyeing of entire garments. The majority of garment types that can be dyed are non-cut garments, such as knitted pullovers, round-necked long-sleeved sweatshirts, coarse twill skirts, coarse twill jackets, knitwear and pantyhose. Tailored garments, such as wish suits or dresses, cannot be dyed as garments because the different shrinkage properties of the different components and linings can distort and distort the whole garment. Garment dyeing involves taking a suitable amount of garments (usually about 24 sweatshirts or clothes of considerable weight), putting them into a large nylon mesh bag (see Fig. 10), which are to be loosely packed, putting 10 to 50 of these packs into a huge dye bath containing a dyeing bath and continuously agitating the garments by means of paddles driven by an electric motor in the dye extraction tank. The machine is therefore called a paddle dyeing machine.
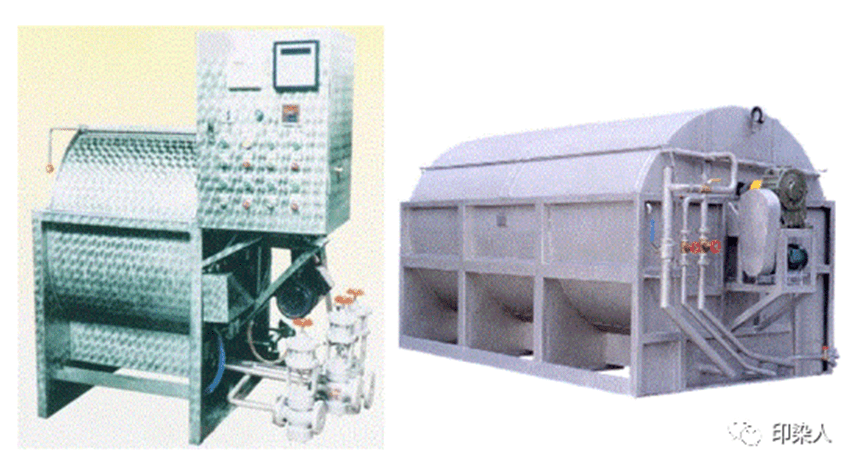
Printing on fabrics
Printing and dyeing are the same, but in the dyeing process the dye makes the whole textile, the overall colouring, while printing is the dye only to some parts of the textile colouring. In order to overcome the bleeding of the dyeing solution and obtain various clear patterns, printing is done by mixing the dye and the necessary chemicals with the original paste into a colour paste and then printing onto the textile. The dye is generally steamed so that the dye is transferred from the colour paste to the fabric. Finally, the printed fabric is also washed and soaped to remove the residual paste, chemicals and floating colours from the fabric.
Fabric printing methods, according to the different dyeing equipment mainly divided into traditional roller printing, screen printing, the newer transfer printing and the latest inkjet printing technology.
Screen printing uses the principle of a leaky plate, i.e. a screen plate to stop the printing paste from dissolving into the area that does not need to be printed.
The dye from the intaglio pattern on the roller printing cylinder is transferred to the fabric.
Transfer printing has outstanding significance in terms of cost reduction, water saving and environmental protection compared to traditional printing techniques. It is the first printing method to print the pattern with dyes made into printing ink onto paper, which becomes transfer printing paper, and then the front of the transfer printing paper is closely laminated to the front of the fabric being printed, and together they enter the transfer printing machine, where the dyes from the transfer printing paper are transferred to the fabric under certain conditions.
Inkjet printing is a digital printing technology that enables the ink (printing paste) to be sprayed directly onto the textile, with the advantages of short processes, instantaneous response, wide adaptability and reduced pollution.
According to the different printing processes, there are three kinds of direct printing, dye proof printing and dye pulling printing.
Direct printing in white or light-coloured fabrics first directly printed with colour paste, and then after steaming and other post-processing to get the pattern of the printing and dyeing process.
Anti-dyeing printing in the fabric first printed to prevent the ground colour dye on the dye or colour printing paste, and then dyeing or colour and the production of colour ground flower fabric printing process.
Dyeing printing in the dyed fabric, using printing methods to partially eliminate the original colour to obtain white or coloured patterns of the printing process.
Finishing of textiles
There are many purposes for finishing fabrics, sometimes to make them softer and fuller, sometimes to make them evenly dyed and bright, sometimes to make the surface of the fabric glossy and high-grade, sometimes to give the fabric some useful functions: such as making the fabric stiff, making the fabric water repellent, making the fabric shrink-proof, making the surface of the fabric with a peach skin velvet feel and so on.
There are several ways to classify textile finishing. The most common classification is appearance finishing (also known as general finishing) and functional finishing (also special finishing). Appearance finishes are those that change the appearance, feel and drape of the fabric; functional finishes are those that improve the inherent function of the fabric.
Finishing can also be divided into chemical and mechanical finishing, which are sometimes referred to as wet finishing and dry finishing respectively. Chemical finishes are usually applied to fabrics by dipping and rolling, followed by drying or curing; mechanical finishes are usually applied to fabrics by physical means to change their appearance.
Finishes can also be classified according to their degree of durability, i.e. permanent, durable, semi-durable and temporary finishes.
Permanent finishing: usually refers to a chemical change in the fibre structure that remains unchanged over the life of the fabric.
Durable finishes: usually remain effective for the life of the product, but their effect diminishes after each wash and is almost completely lost towards the end of the normal service life of the fabric.
Semi-durable finish: withstands several washings and dry cleaning, and many finishes can be renewed in home washings and dry cleaning. Temporary finishing: after the fabric has undergone its first wash or dry clean, the finishing effect is removed or greatly reduced. The effect of finishing on the processing of fabrics is mainly in the change of appearance style and inner quality.
Style finishing for fabric appearance
Dimensional Stabilization Finishing
General fabrics are subject to sizing and stentering, cotton fabrics by pre-shrinking finishing can reduce shrinkage, polyester, nylon and other thermoplastic fibres and their blends by heat setting, woollen fabrics by boiling and steaming tweed can make the size stable.
Sizing refers to the finishing process of fabric dipping and drying to obtain a thick and stiff feel. The slurry is mainly made of pulp and a small amount of preservative, can also add softener, filler or fluorescent whitening agent in the slurry.
Stretching refers to the use of cellulose, silk, wool and other fibres in moist conditions have a certain plasticity, the width of the fabric will gradually broaden to the required size and drying stability of the finishing process, also known as fixed width. After the fabric has been practiced bleaching, printing and dyeing processes, the warp elongation and weft shrinkage, stretched finishing can reduce the deformation of the fabric in the process of taking.
Pre-shrinkage commonly used physical methods to reduce the shrinkage of the fabric after immersion in water to reduce shrinkage of the finishing process. The fabric is first wetted by spraying steam or spraying, and then dried by applying a mechanical squeeze in the warp direction to increase the flexural wave height, and then by loosening. Pre-shrinkage of cotton shrinkage can be reduced to less than 1%, and due to the mutual extrusion between the fibres, yarns and rubbing, the softness of the fabric feel will also be improved. Wool fabric can be used to relax pre-shrinking treatment, fabric by warm water dip rolling or spray steam, in a relaxed state of slow drying, so that the warp and weft of the fabric are contracted.
Boiled wool fabrics are treated in a hot water bath under tension to make them flat and not easily deformed in the subsequent wet treatment finishing process. Boiling is mainly used for fine woollen fabrics. Wool is subjected to various deformations during the weaving process and shrinkage occurs when the fibres are relaxed, more so when wetted. During the hot water bath process, many of the hydrogen bonds in the fibres are broken and the disulphide cross-links are broken, reducing the internal stress in the fibres. After the disulphide cross-chain is broken, a more stable cross-chain is created in a new location, which, together with the newly formed hydrogen bonds, acts as a shaping agent for the fibres after cooling, making the woollen fabric less susceptible to shrinkage and deformation in the wet treatment of the post-process.
Steaming is a finishing process that makes use of the styling properties of woollen fibres under hot and humid conditions, making the woollen fabric stable in form and improving its hand feel and lustre by steaming. The steam temperature should not be too high to avoid damage to the fibres.
Flattening
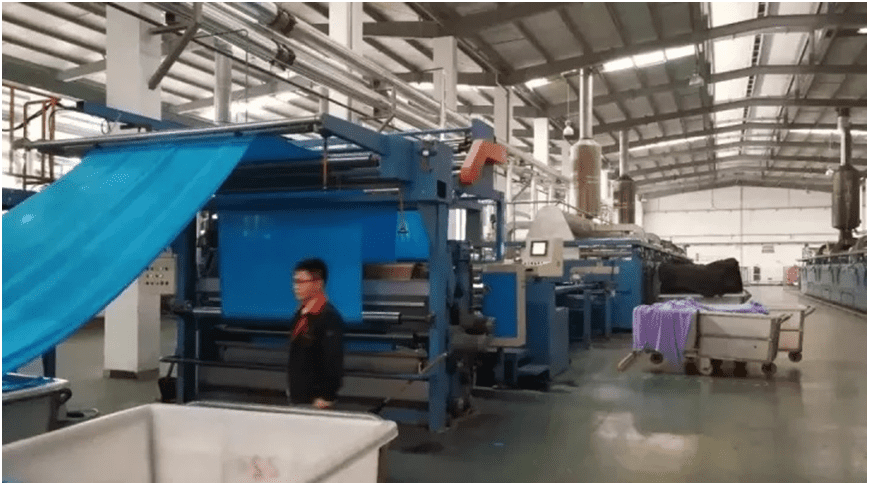
A flattening finish flattens the fabric, thus improving its lustre. The following are commonly used.
Pressing: Under hot and humid conditions, mechanical pressure is applied to flatten the woollen fabric and improve its lustre and hand feel. There are two ways to press it, one is the rotary tweed, woolen fabrics by steam jet evenly to wet, in the heated roller and the matching arc bed between the ironing flattened by squeezing and friction, and endowed with lustre, but the effect is not long; another is the cardboard electric tweed, fabric by voltage after the lustre soft, feel stiff, there is a temporary effect, but the equipment is huge, low production efficiency, mainly for worsted woolen fabrics.
Rolling, electric light, rolling grain using the plasticity of fibres in wet heat conditions, through the two tightly pressed rollers will roll the surface of the fabric flat or roll out parallel fine oblique grain, in order to enhance the finishing process of fabric lustre. A hard rolling point is formed by a hard roller and a soft roller. After the fabric has been rolled and pressed, the yarn is flattened, the surface is smooth, the lustre is enhanced and the feel is stiff, known as flat rolling light. By two soft rollers to form a soft rolling point, the fabric is rolled and pressed, the yarn is slightly flattened, the lustre is soft and the feel is soft, known as soft rolling light. The use of multi-roller equipment, soft, hard rolling point of different combinations and pressure, temperature, through the way of change, can get a different surface gloss. If the fabric is first dipped and rolled resin primary shrinkage and after pre-drying, stentering, after rolling light can get a more durable lustre. If the rollers are heated with electricity and the fabric is polished, it is called electric light. Steel rollers and soft rollers engraved with a pattern of rolling point, in the hot press conditions, the fabric can be obtained to present a lustrous pattern, called rolling pattern. Imitation Finishes
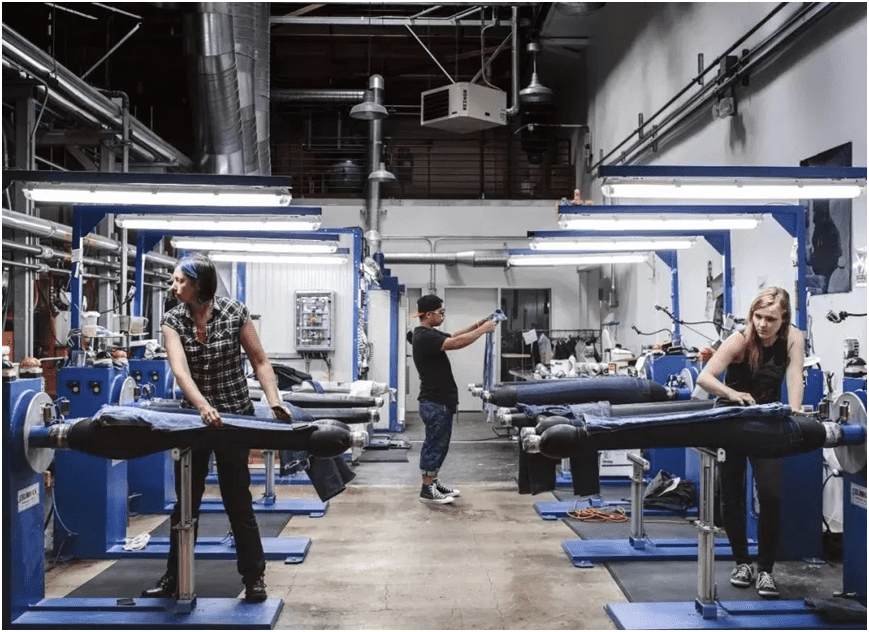
A faux aged finish gives the fabric an aged appearance with a washed out look, derived from the production of denim, commonly used in sand washing, washing and stonewashing.
Washed, sand-washed, stone-washed Firstly, stone-washed finishes were triggered in denim, initially by adding pumice or chemical reagents to achieve a partial whitening effect under mechanical rolling, producing a natural old look style. The processing has now evolved from pure cotton to a variety of fibres. In recent years, to enhance the washing effect, a washing process with the addition of cellulase has emerged. The end result of this process is a good softness and finish, which is difficult to achieve with general softener treatment. Enzymatic washing is limited to pure or blended textiles made from cellulose fibres.
Sand washing is done through the mechanical friction between the fabric surface and the sand and the swelling effect of the sand washing solution on the fibres, grinding away some of the fibres and dyes, so that the fibre molecules are damaged to some extent. After sand washing, the fabric has a uniform thin layer of fleece, the fabric is thick, soft and has a mushy and glutinous feel, good drapability, increased elasticity and improved washability. The sand washing process started with sand washed silks and has now developed into a variety of fibre products. There are two main methods of sand washing, one is by mechanical abrasion method, the other is the chemical pilling method.
suede effect finishing
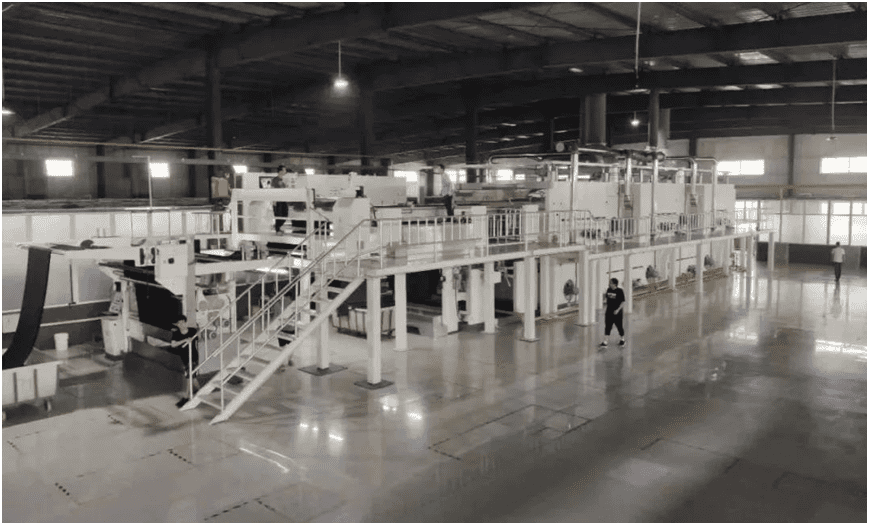
Pile finish can make the surface of the fabric with a layer of long or short pile. Often used to shrink, cut pile, pile, grinding, electrostatic flocking and other methods, such as worsted, corduroy, single-sided velvet, velvet fabrics.
Pile shrinking is a finishing process that uses the shrinkage of wool felts to make woollen fabrics tight and thick and to form pile on the surface, also known as pile shrinking. The shrinkage improves the feel and appearance of the fabric and increases its warmth, and is particularly suitable for products such as worsted woollens.
Pilling is a finishing process in which the fibres on the surface of the fabric are picked up with intensive needles or pricks to form a layer of pile, also known as pile pulling. The pile layer increases the warmth of the fabric, improves its appearance and makes it soft to the touch. Pilling is mainly used on coarse woollen fabrics, acrylic fabrics and cotton fabrics. Woolen fabrics are piled in a dry state, the pile is fluffy and short: woolen fabrics can be sprayed with wet pile to obtain a longer pile, pile after soaking can be obtained wavy long pile. Cotton fabrics are only easy to dry pile.
Abrasion Abrasive rollers wrapped in emery are rotated at high speed by the tip of the abrasive grain to hook out the fibres on the surface of the yarn in the fabric and grind them into a layer of short pile finishing process, also known as abrasion. The size of the abrasive rollers, the organisation of the fabric and the operating conditions are closely linked to the quality of the abrasive. Abrasive fabrics are thick, soft and warm, which improves the performance of the fabric. The knitted fabric of deformed yarn or high shrinkage polyester can be made into a kind of imitation suede fabric after grinding down; the base fabric made of microfiber, after dipping and rolling polyester emulsion and grinding down is the basic process of manufactured artificial suede.
Electrostatic flocking uses an electrostatic field to flock short pile-like fibres to a fabric coated with adhesive to form a raised surface. The entire surface of the fabric can be flocked or only a certain area of the fabric can be flocked to produce a certain pattern.
Special surface effects finishing
Special surface effect finishing can make the surface of the fabric to form a special surface effect, such as copy tweed production in the rubbing tweed, imitation wool production in the ball, crepe fabric production of wrinkles and rolling, cutting flowers, grinding flowers, etc..
Coating finishing
Coating finishing is a uniform coating on the surface of the fabric with different colours or different functions of the coating agent, so as to get a colourful appearance or special function of the product. The main component of the coating agent is a polymer film-forming materials, it is different from the resin finishing, is part of the surface treatment of the fabric, so the coated fabric is a binary composite of fibres and polymer films, both with the performance of the fibres themselves, but also with the performance of polymer films. Resin finishing is not a surface finish, the resin used is infiltrated inside the fibre molecules and chemical cross-linking takes place to become one product.
Coating finishing process is being respected, with high-tech production of coated products, soft to the touch, moisture absorption and breathable. At present there is a wide variety of coated fabrics for a wide range of applications. For example, the surface has a metallic bright or pearl fabric, is coated on the fabric containing metal powder or imitation pearl powder coating made; oil light cloth is the surface of the fabric coated with a transparent light agent; luminous fabric is coated with luminous paint on the fabric, can put light in the dark; and imitation animal fur, the paint will be painted on the surface of the fabric to imitate the pattern of animal skin colour, after rolling grain finishing to get the leather pattern. In addition, coated with different functional coatings on the surface of the fabric, you can get waterproof, oil-proof, fire-proof, UV-proof, anti-static, anti-radiation and other functional coating fabrics.
Inherent quality finishing of fabrics
General wear properties
Conventional wear properties can improve the application properties of the fabric in the wear process.
Soft finishing: textile in the dyeing and finishing process, by a variety of chemical agents, wet heat treatment and mechanical tension and other effects, not only tissue structure deformation, but also can cause a stiff and rough feel. Soft finishing is the process of making up for this defect to make the fabric soft to the touch. Soft finishing has mechanical and chemical methods, mechanical method using pounding cloth and other processes, so that the yarn or fibre between each other loose, so as to obtain a soft effect; chemical method is to use the role of softener to reduce the coefficient of friction between the fibres, in order to obtain a soft effect. The chemical method is more commonly used and is sometimes supplemented by mechanical methods. Usually the textile is impregnated in a softener solution for a certain period of time, then dehydrated and dried, sometimes the softener can also be used together with other finishing agents. Some softeners can be baked to produce a washable finish. Due to the different softeners, some products are smooth and plump, while others are smooth to the touch, sometimes the two are mixed to make the finishing product both plump and smooth.
Stiff finishing: the use of natural or synthetic polymeric substances with a certain viscosity made of slurry, forming a film on the fabric, thus making the fabric smooth, stiff, thick, plump, etc., and improve the strength and abrasion resistance, to extend the service life. In order to obtain a more washable stiffness effect, thermoplastic resins and cellulose preparations are often used to finish fabrics.
Non-iron finishing: Cellulose fabrics and their blends are prone to wrinkling due to the breakage of hydrogen bonds between the molecular chains in the amorphous zone of the fibres, resulting in the molecular chains slipping and re-forming at a new location and stabilising to produce wrinkles. The mechanism of non-iron finishing is to limit the slippage of the molecular chain of fibres, improve the resilience of fibres and make the fabric less prone to wrinkling in the course of consumption. Mainly used for cellulose fibre fabrics, viscose fabrics and their blended fabrics, can also be used for silk fabrics. Commonly used resin anti-wrinkle finishing, fabric by finishing often make the mechanical and physical properties of the fabric changes. In the normal process conditions, viscose fabric breaking strength less increase, so that the strength of a significant increase; cotton fabric strength has decreased, which is due to finishing after the fiber stress is difficult to disperse and caused. Commonly used resin finishing agent is divided into two categories: 1) aldehyde resin finishing agent, this type of resin finishing effect is good, but can not avoid taking the release of formaldehyde harmful to humans, so at home and abroad are committed to formaldehyde and low formaldehyde finishing technology. 2) no formaldehyde finishing agent, such as polycarboxylic acid compounds, but from the finishing effect and the balance of prices, can not yet replace the widely used aldehyde finishing agent.
Anti-felt shrinkage finishing: a finishing process to prevent or reduce shrinkage and deformation of woollen fabrics during washing and taking. Wool is scaly and has a high degree of elongation and resilience in the wet state. When woollen fabrics are washed and squeezed, they are prone to felt shrinkage, known as felting. Felt shrinkage can be reduced by felting the fabric, and pilling can also be reduced. There are two traditional methods of felting: 1) chemically corroding the scales to change the surface properties of the wool, and 2) using polymers to cover the scales on the wool surface or bonding at the fibre intersections. In addition, with the development of high technology, biological enzymes, low temperature plasma on the wool of the anti-felt shrinkage finishing has made good achievements, but not mature, need further research.
Weight Gain Finishing: A process to increase the weight of silk fabrics by chemical means. The main purpose is to make the silk fabric feel rich and increase its drapability. The main processing methods are the tin weighting method and the tannin weighting method. The deformation of silk fabrics can also be treated to achieve a weighting effect.
Weight reduction or reduction finishing: chemical methods to cause dissolution on the surface of polyester fibres, so that the weight of the fabric is reduced to form a silk style finishing process. Polyester by weight reduction finishing, soft lustre, light and soft, flat and smooth, draping properties greatly improved.
Silk finishing: cotton fibres treated with alkali, alkali can penetrate deep into the fibre crystalline area, partly to overcome the bonding force within the crystal, causing the crystal area or the original fibre to dissolve. After heating or washing, the lye is removed from the fabric so that the fibre molecules are stabilised in a new position, resulting in a reduced crystallinity and a silk-like lustre on the surface of the fabric.
Functional Finishes
Functional finishing gives the fabric one or more new properties.
Flame-retardant finishing: some special-purpose textiles, such as firefighting work clothes, military clothing, baby clothes, carpets, etc., require a certain degree of flame retardant properties, so that the fabric in contact with the source of fire becomes scorched and no bright flame, leaving the source of fire no longer burning, no residual combustion or negative combustion phenomenon.
The role of flame retardants is mainly to change the reaction process when the fibre is on fire: 1) Under burning conditions, the reaction process of the fibre will be changed.
1) Under burning conditions, the generation of strong dehydration of the material, so that the fiber charring and less likely to produce combustible volatile substances to prevent the spread of flame.
2) The flame retardant can be decomposed to produce non-combustible gases, thus diluting the combustible gases and acting as a shield for the air or inhibiting the flame burning.
Water Repellent Finishing: A finishing process that uses a chemical water repellent to form a water repellent surface on the fibre. Silicone is a relatively newly developed wash-resistant water repellent finishing agent, the reaction performance is more active, after finishing, the fabric has a good and more wash-resistant water repellent performance, and for a variety of fibres, can increase the tear strength of the fabric, improve the feel of the fabric and sewing performance.
Anti-static finishing: the use of chemical agents applied to the surface of the fiber, increasing its surface hydrophilic, textile fibers on the accumulation of static finishing process.
Synthetic fibres are poorly hygroscopic and electrically conductive and can cause a lot of trouble during processing or use due to friction and electrostatic charges. Antistatic agents can give fibres and fabric surfaces a certain degree of moisture absorption and ionicity, thus improving the conductivity and achieving antistatic purposes. Washable fabric antistatic finishing methods are: with moisture-absorbing polymer electrolyte treatment fabric, and fixed with the surface of the fiber; with hydrophilic groups containing polymer treatment fabric, so that the plant has a certain antistatic and easy to decontaminate; grafting to make the fiber denaturation method to improve the moisture absorption, and to achieve a durable antistatic effect.
Stain Release Finishing: A chemical finishing process that makes it easy to remove dirt from the surface of a fabric by normal washing methods and prevents the dirt from re-staining during the washing process. Fabrics, especially chemical fibres and their blends, are susceptible to electrostatic attraction of dirt, and due to the poor hydrophilicity of the surface, dirt is difficult to remove, and due to the oleophilic nature, the dirt in the suspended washing solution is easily re-stained on the surface of the fibres. Therefore, the principle of easy stain removal finishing is to increase the hydrophilicity of the fibre surface and reduce the surface tension between the fibre and water. This is achieved by impregnating the surface of the fabric with a hydrophilic polymer.
Mothproofing: Wool fibres made up of protein molecules are susceptible to moth in the course of storage and consumption. A mothproof finish means that the wool fabric is treated with a mothproof agent to make it mothproof and no longer a food source for larvae, or to poison them with an insecticide. The insecticide used is harmless to humans and does not affect the colour or fastness of the wool fabric, or the feel or appearance of the wool fabric. The most commonly used mothproof finishing method is to use the affinity of wool for mothproofing agents to make the wool itself a mothproof fibre with mothproofing properties.
Anti-radiation finishing: different finishing methods are used for different types of radiation. Anti-electromagnetic wave radiation clothing commonly used to achieve shielding method, that is, through the surface of the fire layer of metal will be reflected back radiation waves to achieve shielding, protective materials available metal mesh protective layer, can also be coated with metal powder on the fabric, nickel metal coating is the most used. Anti-x-ray, can be lead, barium, molybdenum, tungsten and other metals and their compounds and fabric bonding or mixed with fibres.
Antibacterial finishing: With the improvement of living standards, people are not only satisfied with the “food therapy”, but also began to pay attention to “clothing therapy”, antibacterial finishing of textiles for “clothing therapy” an The antibacterial finishing of textiles is an effective way of “clothing therapy”. The antimicrobial agent is combined with the fabric through chemical additives, or the use of its active group of antimicrobial agent prefabricated species of fibre cross-chain and made of antimicrobial fabric, not only can effectively kill bacteria or inhibit the growth and reproduction of bacteria, but also reduce cross-infection, thereby reducing the spread of disease. Fabrics with different antimicrobial properties can be produced depending on the antimicrobial agent. Antibacterial finishing methods include impregnation, dipping and rolling, coating and spraying. To achieve long-lasting antibacterial properties, fabrics can be produced by blending antibacterial fibres through the spinning process.
New Finishing Technologies
As human beings become more and more concerned about environmental pollution and damage and pay more and more attention to health, the need to reform the traditional, more polluting finishing process becomes more and more urgent. Continued advances in science and technology as well as crossover between disciplines are leading to a search for new energy-saving, efficient, fast, stable and non-polluting finishing systems.
The following are the main ones introduced.
Biological enzyme finishing technology biological enzyme is a biological catalyst, usually produced by living organisms with catalytic effect of a class of proteins, with efficient, stable, non-polluting characteristics.
At present, the more mature processes are
1) Amylase desizing, which allows continuous desizing at high temperatures. The corresponding traditional processes are alkali desizing and alkali-acid desizing.
2) Cellulase is used in the “bio-wash” finishing of denim garments to make the jeans softer and more comfortable, while still retaining their natural flavour on the surface and having greater strength. The corresponding traditional processes are washing and stoning.
3) Protease treatment of woollen fabrics, replacing the traditional organochlorine salt method. By treating the outer scales of wool fibres, through puffing, deformation, removal can achieve the following effects: ① wool fabric anti-felt shrinkage; ② wool sweater “machine washable”; ③ wool fabric dyeing more colourful; ④ feel soft, rich style. 4) Protease for silk fabric degumming finishing, instead of the traditional process of high temperature soap and alkali method, to avoid soap and alkali method damage, and The rate of degumming is high, the feel is soft, the style is rich and the whiteness is excellent.
Low temperature plasma finishing technology Low temperature plasma technology is a means of changing the performance of fibres in the discharge treatment. Under high vacuum conditions, an alternating electric field of high field strength is used to ionise the gas into a plasma that remains electrically neutral as a whole. Through these high speed moving active particles an energy exchange takes place on the surface of the textile material, thus achieving a surface etching or surface modification effect.
Current applications in textile processing are.
1) increasing the surface roughness of fibres and improving fibre spinnability
2) anti-felt shrinkage treatment of wool.
3)improvement of dyeing performance or dyeing depth
4) various functional finishes (anti-wrinkle, flame retardant, anti-bacterial, anti-static, etc.).
Microcapsule finishing technology will be a certain substance with certain polymer compounds or inorganic compounds, using mechanical or chemical methods wrapped up, made of particles with a diameter of 1 ~ 500μm, in the normal state for the stable solid particles, while the original properties of the substance is not lost, in the appropriate conditions, it can be released again, this particle is called microcapsules, its main materials are the core and wall materials. Using the classical coalescence method, the core and wall materials are made into microcapsules, dried and dispersed in an aqueous solution, coated directly or mixed with appropriate additives and sprayed onto the fabric, then the capsules are all adhered to the inside of the fabric by means of group pressure rollers, releasing the core material by diffusion, wall dissolution or biodegradation. The use of different core materials, wall materials, will produce different finishing effects, the current application of flame retardant, water repellent, oil repellent, anti-bacterial, insecticide, anti-static, aroma, etc..
Foam finishing technology is characterised by low energy consumption and speed. It can save a lot of water for dyeing and finishing, reduce the amount of effluent discharge as well as improve the treatment capacity of effluent.
Vacuum coating finishing technology is able to form an extremely thin metal film on the surface of fibrillated fabrics. Its products are mainly shielding materials, such as anti-radiation, anti-electromagnetic wave, space cotton, metal cotton, shielding materials for computers, etc.