Original colour difference, before and after colour difference
Causes
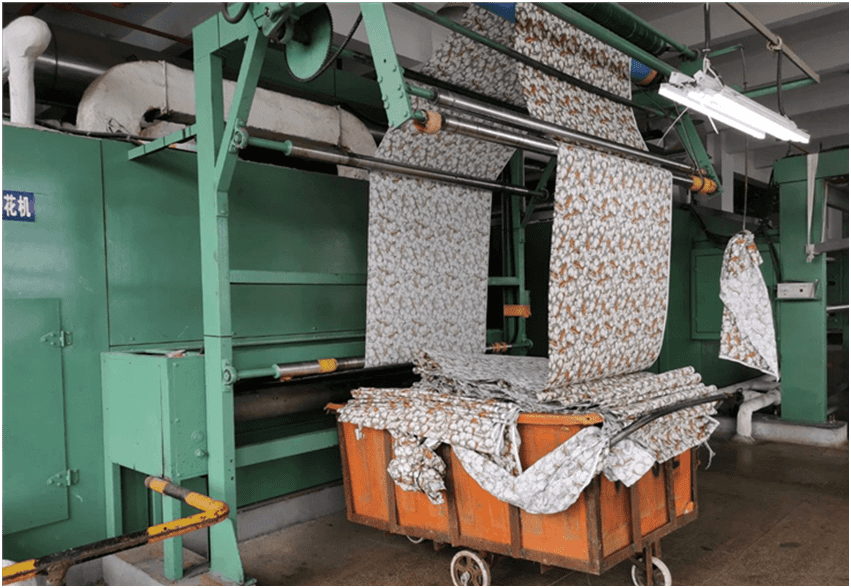
1.The operation is not standardized and the control of process parameters is not in place when imitating the colour of small samples, so the imitation colour samples cannot reflect the real colour and light of the dyeing formula.
2. Inaccurate weighing, inaccurate chemical material and inappropriate control of various technical parameters when releasing the sample, the sample cannot reflect the normal colour of the dyeing formula, which affects the normal judgement of the colour matching personnel and the deviation of the formula adjustment.
3. The samples from customers are not carefully analysed, and the dyestuff combinations chosen for the dyeing formula are different from the dyestuffs used in the samples from customers, and there is the phenomenon of the same colour and different spectrum (jumping lights), presenting different colours under different light sources.
4. Errors of vision of the colour mixing personnel, resulting in inaccurate colour matching.
5. Small sample colour imitation, large car release sample after not according to the customer’s contract standards for finishing, resulting in large goods for finishing colour and light changes.
6. Dyeing formula in the dyestuff performance difference is too large, large car production process when the process parameters fluctuate fabric colour change is too large.
7. inconsistency in wool effect, whiteness, pH value, desizing and wool grinding effect of semi-finished products before dyeing.
8. Fluctuations in the main technical parameters of the dyeing process, such as fluctuations in the level of the dyeing liquid in the rolling trough, the speed of the vehicle, the temperature of the baking, the baking temperature, the pressure of the rolling car, the temperature of the reduction (solid colour), the time, the concentration of the dye, the solid colour liquid, the concentration of the reduction liquid, etc., resulting in colour changes.
9. Dyestuff ironing discolouration, resulting in inaccurate colour matching.
10. Blank fabric causes: Different manufacturers, different batches of blank fabric from the same manufacturer are often due to different quality of cotton fibres, different twist of yarns, different sizing of warp yarns, differences in water absorption and dyeing properties of the fabric after treatment, resulting in colour differences between pits when dyeing.
11. Dyestuff causes: differences in colour light and power of dyestuffs from different manufacturers and different batches from the same manufacturer.
Preventive measures
1. Carefully analyze the fiber type, dyestuff type, colour light source, finishing effect, etc. of the customer’s sample, and use the same specification blank fabric, the same type of dyestuff, and the same finishing process as required by the contract. If the customer’s sample is different from the contract fabric, a small sample should be imitated and then handed over to the customer for approval before organising the production of large vehicles.
2. Small sample colour imitation personnel, large car colour matching personnel to carry out training and testing of colour recognition ability, unified vision of relevant personnel.
3. When operating colour matching, ensure the consistency of colour matching conditions, such as colour matching light source, brightness, observation angle and distance, etc.
4. Strengthen the performance testing of the dyestuffs used, such as the high temperature baking and colour fixing performance of disperse dyestuffs, the directness of reactive dyestuffs, the specific shift value, alkali resistance and temperature resistance, etc., to ensure consistent application performance of the dyestuffs used.
5. Strengthen the management of weighing, chemical and batching materials to eliminate mistakes and reduce errors.
6. Strictly regulate the operation of the machine to ensure that the technical conditions of each process meet the standards of the process design.
7. During normal production, the machine should leave a standard sample of the production of the large car at the drop cloth, and the drop cloth worker, the machine manager and the colour checker should check the sample at any time, so that problems can be found and dealt with in time.
8. When colour matching, the sample should be fully cooled to reach the normal level of dampness, and can be dried by steam dampness and electric blowing.
9. Strengthen the management of blank cloth, a contract, a colour position as far as possible to use the same manufacturer of the same batch of blank cloth.
10. Use the same manufacturer and the same batch of dyestuffs for small sample imitation, large car release and normal production to prevent colour fluctuations due to differences in dyestuffs.
Left-centre-right colour difference
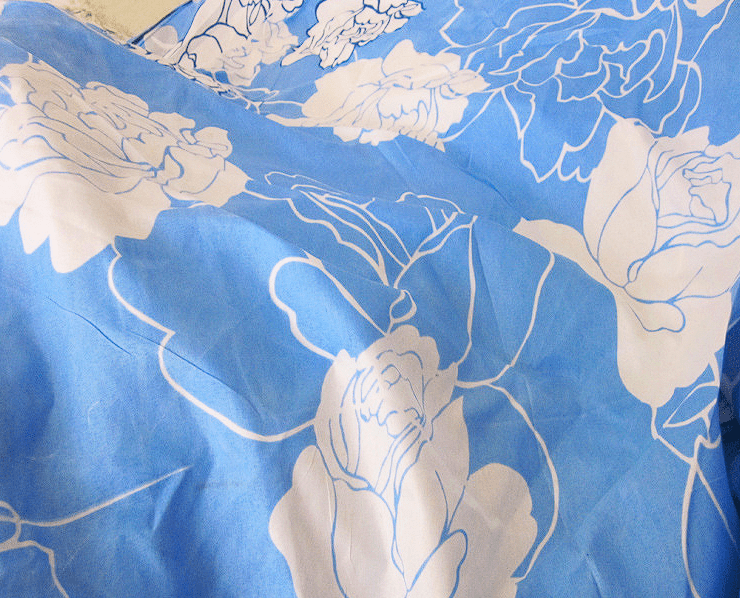
Causas.
1. The semi-finished products are inconsistent in terms of gross effect, whiteness and mercerization effect in the left middle and right.
The main reasons for production are
A. Inconsistent pressure in the middle left and right of the mill. The cylinder air pressure at both ends of the mill is inconsistent, the bearing wear degree at both ends of the mill is inconsistent, and the roller wear degree is different resulting in inconsistent amount of fabric with liquid.
B. Each working liquid rolling tank in the left and right concentration is not consistent.
C. mercerization when drenching alkali, absorbing shouting degree is not consistent.
D-Washing is not sufficient, the fabric left in the right pH, containing impurities, surfactants are not consistent.
2. Polyester and blended, interwoven fabrics when shaping inconsistent temperature in the box left and right.
3. Inconsistency in the effect of abrasion in the left and middle right of the fabric.
4. When dyeing, priming, reducing uniform rolling car at both ends of the air pressure, middle oil pressure control is not appropriate, rolling car line pressure is not consistent, resulting in the fabric left in the right with different amounts of liquid; rolling tank dyeing liquid (reducing liquid, solid colour liquid) concentration is not consistent; hot air drying, drying cylinder drying when the drying degree of each part is not consistent, resulting in dye swimming shift; polyester blended, interwoven fabric dispersion baking when baking temperature left in the right is different; uniform rolling car each part The degree of wear and tear is different. Reduction (solid colour) steamer temperature is not enough.
5. Dyeing formulas choose too much difference in the performance of the coloring dyes.
6. inconsistent rolling pressure, too high temperature inside the box, too big temperature difference when finishing and shaping.
Preventive measures
1. Regularly inspect the degree of wear and tear of each working liquid tank rolling, (including desizing, boiling and bleaching, mercerizing, dyeing, and shaping machine rolling, uniform rolling) to ensure that the amount of liquid carried by each part of the fabric is even and consistent.
2. Each working liquid tank use overflow pipe to supply material to ensure that the working liquid system is uniform and consistent.
3. Strictly control the technical parameters of each process, such as desizing, refining, bleaching, mercerising and other working liquids with various agent concentrations, temperature in the steamer, stacking time, humidity in the box, mercerising alkali concentration, expansion shower, alkali absorption uniformity, etc. must be strictly controlled, and the semi-finished product processing effect must meet the quality needs of the dyed products.
4. Strengthen the water washing, adopt the backward flowing way grid by grid, the water washing tank is separated by partitions to form a serpentine water flow state, spraying with hot water is appropriate to ensure that the fabric is fully washed with even and consistent effect.
5. Hot air pre-drying left in the right temperature, air volume should be uniform, to ensure that all parts of the fabric is heated evenly, to prevent the dyestuff occurred swimming shift and cause colour difference. Often check whether the pre-drying box exhaust air is normal, circulating fan operation is normal, belt elasticity is consistent, heat sink left and right temperature is consistent.
6. Before baking and drying, try to reduce the moisture on the fabric to prevent too much moisture on the fabric, and when baking and drying, the temperature difference on the surface of the baking box will cause the dye to swim with the moisture flow to form a colour difference.
7. baking oven in the left and right temperature to maintain consistent, so that the fabric evenly heated disperse dyestuff sublimation degree of colour fixation consistent. The air volume in the upper and lower air ducts of the baking oven should be consistent, the air volume in the left middle right of the air outlet should be uniform, and the insulation performance of the oven should be good; the exhaust air volume should be appropriate, not too large otherwise it will cause the temperature difference in the oven to increase, resulting in colour difference.
8. scientific and reasonable formulation of dyeing process, must choose to dye the various performance consistent dyes for colour matching, such as disperse dyes high temperature sublimation solid colour rate performance to be close, special colour position need to choose similar types of dyes for colour matching; reactive dyes should choose low directness, high than shift value, alkali resistance and temperature resistance, high solid colour rate, easy to wash good, solid colour conditions consistent dyes for colour matching. Reduce colour changes due to normal fluctuations in process parameters.
9. Regularly test the priming part and the reduction soaping part of the uniform rolling car rolling liquid rate, keep the rolling car in good condition, the oil and gas paths are smooth, the adjustment valve is flexible and effective, and the instrument display is flexible and accurate.
10. Strengthen the detection of the abrasion effect of the abrasion products to prevent the dyeing colour difference caused by the inconsistency of the abrasion effect of the fabric left and right.
Colour stripes, colour blooms
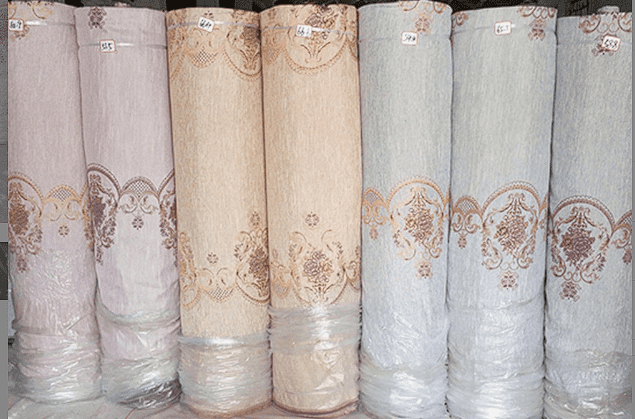
Causes
1. Burnt wool strip flowers: whether gas burnt wool machine, electric burnt wool machine are easy to produce burnt wool strip flowers.
The main reasons for burning hair stripes are.
A. excessive burning, fire mouth flame is too long (cylinder temperature is too high, and fabric contact arc is too large) fabric contact flame time is too long, the middle cooling is not timely, the main body of the fabric temperature is too high. Polyester fiber in the high temperature state molecular chain movement intensified, the formation of different sizes and forms of different crystals, so that the fiber dyeing properties change dyeing formation strip flower.
B. Fire mouth blockage leads to fire mouth flame break flame, cylinder surface is not flat (debris). This leads to uninterrupted hair streaks in the warp direction on the fabric surface after burning.
C. Combustible gas and air ratio is out of balance, the proportion of air is too large, the flame jumping; air proportion is too small flame long and weak, fabric fabric surface appear overall uneven wool sense of the strip flowers.
2. Desizing is not net, cooking is not transparent to lead to dyeing strips of flowers. Such as working liquid concentration is too low, rolling car pressure is too large, steam temperature is too low, time is too short, humidity is not enough may lead to fabric desizing uneven, cooking impermeable, leading to dyeing stripes of flowers colour flower phenomenon.
3. The local wear and tear of the rolling car, fabric dipping and rolling working liquid with different amounts of liquid, fabric processing effect is different, dyeing colour differences.
4. Blank fabric thin and dense road, strip dry uneven, dyeing and drying when the dye swimming shift formed strip shadow and rain-like strip flowers.
5. Dyeing when drying too fast dyestuff swimming shift to produce rain-like stripes.
6. Poor dispersion of dyestuff suspension, low dyeing solution in the rolling trough, uneven dyeing solution flowing on the fabric surface when the fabric enters the uniform rolling car, uneven dye distribution.
7. Dyestuff in the reduction (solid colour) steamer steam too low temperature, dyestuff reduction (solid colour) degree of inconsistency, has been reduced dyestuff has a high affinity for the fabric, has not been reduced dyestuff has no affinity for the fabric, the fabric in the process of running dyestuff with the flow of condensate led to the formation of stripes.
8. When dyeing brushed fabrics, the inconsistent brushing effect on the fabric surface leads to the formation of stripes.
A. The sandpaper used for brushing is too coarse and the grit is not uniform.
B. The abrasive tension is too large and the contact curvature between the fabric and the abrasive roller is too large.
C.The fabric is abraded in the state of damp or inconsistent damp, and it is very easy to produce stripes.
D. The abrasive belt wound on the abrasive roller is not well fixed, loose and moving, resulting in inconsistent abrasive effect.
preventive measures
1. Develop a reasonable burning wool process, strict burning wool machine standard operation. Ensure that the burning wool fire mouth smoothly without blockage, so that the fire mouth flame short, Qi, uniform, burning powerful, no broken flame, no jumping. Polyester and blended and interwoven fabrics are burned with a small fire and a fast burning process. Increase the intermediate cooling, reduce the temperature of the main body of the fabric, drop cloth temperature to maintain below 50 degrees.
2. Strengthen the quality inspection of the blank fabric, choose the blank fabric that meets the quality standard of the dyed product to organize the production.
3. Strengthen the testing of semi-finished products’ wool efficiency, whiteness, pH value and wool grinding effect to ensure that the inner quality and appearance quality of semi-finished products meet the dyeing quality standard.
4.Improve the dispersion stability and wetting and penetration ability of the suspension dyeing solution, try to maintain the height of the liquid surface, so that the fabric can evenly absorb the dyeing solution; try to reduce the amount of liquid carried by the fabric to reduce the dye swimming shift; when drying with hot air, try to lower the drying room temperature and reduce the speed of the circulating fan to avoid the high air volume and high temperature emergency drying to aggravate the dye swimming shift causing strip shadows and rain-like stripes; when drying in the drying cylinder, try to lower the drying cylinder temperature to prevent emergency drying. Reduction (solid colour) steamer adopts air sealing method, reduce the amount of fabric with liquid can obviously improve the phenomenon of stripes; keep the steamer temperature, improve the dyestuff reduction (solid colour) speed to reduce the flow of dyestuff, to avoid the production of stripes.
5. According to the characteristics of the fabric, colour characteristics of the choice of good performance anti-swim shift agent can significantly improve the phenomenon of strip shadow.
6. Polyester blends, interwoven fabric dyeing to ensure the consistency of colour depth and colour light on both fibres.
7. Choose dyestuff dyeing performance to be the same or similar.
8. Strengthen the equipment, process, operation and quality management of the brushing process to ensure that the brushing effect of the product meets the quality standards of the dyed product.
Pigmentation, discolouration
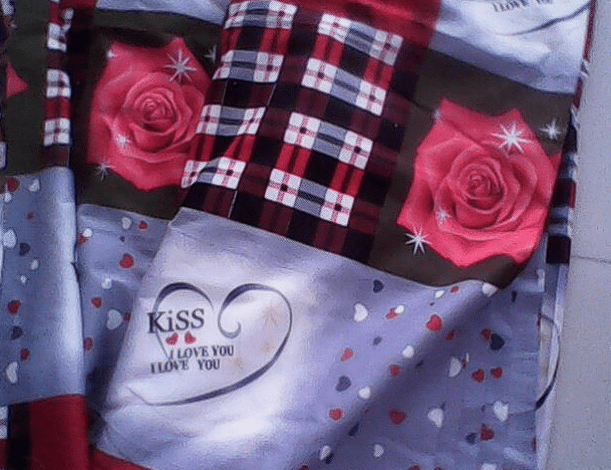
Causes
1. When preparing the dyeing solution, the dyestuff is not sufficiently wetted and dispersed (dissolved).
2. Insufficient stability of the dyeing solution, dyestuff accumulation and precipitation.
3. Poor foam inhibition of the dyeing solution, irregular flow of the dyeing solution in the rolling trough forming foam when the fabric is running. Dyestuff adsorbs on the surface of the foam and returns to the fabric surface to form colour spots.
4. Unsanitary and uneven desizing, pulp accumulation and staining. Dyeing forms colour stains.
5. Pre-treatment auxiliaries residue, surfactants in acid, high alkali when the formation of flocculent, paste stained fabric dyeing lead to colour spots.
6. After finishing the fabric, the finishing auxiliaries are stained with dyestuff or anionic surfactants when dyeing and reworking, resulting in cohesions that stain the surface of the fabric and form colour spots and oil spots.
7. Dyeing machine mechanical hygiene is not thorough, chemical material barrel, pipe, valve, rolling trough, cloth division, guide roller stained with dyes, rolling car, guide roller, pre-drying, baking box air duct, wind box, box stained with dyes on the surface of the fabric to form colour spots.
preventive measures
1. Use soft water when dyestuffs are being prepared to prevent metal ions from forming calcium spots with dyestuffs and auxiliaries and dyestuff coagulation and precipitation.
2. Strictly regulate the operation of various dyestuffs, dispersion, reduction and other suspension dyeing solution preparation is best to use cold water, dye stirring process to strictly control the temperature below 50 ℃, to prevent high-speed stirring temperature rise dispersant stability to reduce dye coagulation. For reactive and other water-soluble dyestuffs, cold water should be used to form a slurry and hot water should be added at the appropriate temperature to dissolve the dyestuff under stirring. When preparing the dyeing solution, fully filter the dyestuff to remove any precipitates and impurities that are not completely dispersed and dissolved.
3. Carefully and carefully do the dyeing machinery hygiene to prevent the residual dyestuff on the machinery from staining the fabric and causing colour spots and stains.
4. Strengthen the performance test of various auxiliaries used in pre-treatment, dyeing and finishing to ensure the stability of various working liquids and reduce the various colour spots and stains caused by the performance of auxiliaries.
5. Strengthen the foam suppression of dyeing and reducing (fixing) liquids. When the working liquid foam more can add a small amount of non-silicone defoamer (defoamer must be diluted and slowly added drop by drop).
Holes and tears
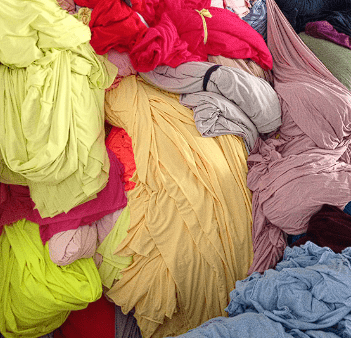
Causes
Holes are a common problem for printing and dyeing factories producing cellulosic fibres and blended and interwoven fabrics, posing a serious threat to product quality. Holes can be broadly divided into oxidative holes and mechanical holes. Mechanical holes are more obvious, easy to find and deal with, oxidative holes are very hidden, often not easy to be found, only in the mercerization of the fabric through the role of concentrated alkali oxidation of cellulose further hydrolysis, a significant drop in strength and then through the guide roller, cloth tongs of the warp and weft tension role of yarn breakage formation holes.
The main reasons for this are
1. The fabric contains oil yarn or heavy metal ions, iron filings, rust, ash and other substances that have a catalytic effect on the decomposition of hydrogen peroxide.
2. The water used (recycled reuse water) has a high content of heavy metal ions.
3. The stability of the hydrogen peroxide bleaching system is not enough, and the decomposition of hydrogen peroxide is too fast under high temperature and high alkali condition.
4. The use of hydrogen peroxide concentration is too high, the concentration of caustic soda is too high, the gas steam temperature is too high and the time is too long.
5. Hard debris embedded in the rolling mill rolls. When the fabric passes through the rolling mill, it forms regular, similar-shaped holes with the same distance between them and the circumference of the rolls.
6. Cotton knots, coarse warp and weft of blank cloth are ground by the wool grinding machine when the cotton knots and coarse warp and weft are protruding from the cloth surface, and the yarn is broken to form holes and broken when grinding .
7. Mercerizing machine cloth tongs wear deformation, track deformation, improper adjustment, so that the cloth side of the uneven force, expansion of the width of the door width too wide caused by the cloth side of the hole, broken edge.
8. The needle plate of the sizing machine is broken, bent needle, the track of the sizing machine is out of adjustment, the width of the door is too wide, the temperature is too low at the cloth off the needle effect is not good.
preventive measures
1. Strengthen the penetrating agent, refining agent, oxygen bleaching stabilizer, chelating and dispersing agent and other additives performance testing and desizing, refining, oxygen bleaching working fluid alkali resistance and temperature resistance, solution stability, emulsification and dispersion performance, refining, hydrogen peroxide decomposition rate and other tests, a comprehensive evaluation of the performance of various additives, according to the performance characteristics of additives and different processes to choose the appropriate additives.
2. According to the characteristics of the fabric species, choose the pre-treatment processing methods that are compatible with it. Such as cotton fabrics can be used to cold roll pile process, fabric rolling alkali oxygen liquid after room temperature pile, fabric peroxide on the slow orderly decomposition, fabric damage is small, less weight loss, feel good, reduce the risk of oxygen bleaching hole. Polyester and cotton fabrics can be used alkali oxygen a bath low temperature steam process, fabric shrinkage small, less weight loss, simple process, less sewage discharge, low COD.
3. Desizing, refining to strengthen the water softening and fabric on the removal of metal ions.
4. Adopt heavy boiling and light bleaching process, reduce the amount of hydrogen peroxide, and choose to use stabilizers with good stability, low decomposition rate of hydrogen peroxide, alkali and temperature resistance. Ensure the slow decomposition of hydrogen peroxide.
5. Strengthen the rust prevention and rust removal work of the plant, equipment, fabric car and other facilities to prevent rust and iron chips from staining the fabric.
6. Strengthen the quality inspection of blank fabrics and the process control of the grinding machine, improve the fineness of sandpaper and adopt multi-roller light grinding process to reduce fabric damage.
7. Strengthen the inspection and maintenance of mercerizing machine, sizing machine fabric tongs (needle sheet) and track, and operate strictly according to the process.
Air-drying print
Causes
1. fabric burned hair rolled water (liquid) after storage for too long, the slurry swim shift film caused by air dry print.
2. fabric stacked in the steam box uneven heat. Fabric with too small amount of liquid, steam box in the bottom of the water level is too low (steam leakage in the box) to form superheated steam caused by local water loss of fabric air dry. The steam pressure is too small and cold air enters the steamer causing air-drying.
3. Long storage of semi-finished products, residual surfactants and alkali agents on the fabric are affected by air, dryness and humidity to form uneven distribution and changes in fibre properties.
4. Inadequate washing of dyed fabrics, long storage, dyes on fabrics affected by alkali, reducing gas, sunlight exposure to produce colour changes. Most of the reactive dyes do not have high sunlight fastness, alkali agent is easy to make vinyl maple type dyes and fiber bonding bond break to produce air dry print.
preventive measures
1. strengthen production management, avoid burning wool after a long period of fabric storage. Short-term storage to cover the film to prevent air-drying.
2. Strengthen the desizing, refining, bleaching process control and operation, keep the steam box has enough saturated steam, to eliminate dry steam. When stopping for a long time for some reason, we should cool down and wash the fabric in time to remove the pulp and refining agent, and wash and repair in time.
3. When semi-finished products are stored for a long time, A-frames can be used to store them in rolls.
4. reactive dyestuff dyeing fabric washing to be adequate, remove the floating colour on the fabric, use acid soap detergent soaping can thoroughly neutralize the alkali agent on the fabric to eliminate the influence of alkali agent on the dye, can alkali less dyeing after air-drying print production. The fabric is stored with a film and cloth cover to avoid sunlight and the influence of harmful gases.
Colour fastness failure
Causes
1. Poor fabric refinement and mercerisation, resulting in insufficient penetration and diffusion of dyestuff into the fabric and the accumulation of dyestuff on the fabric surface.
2. unreasonable choice of dyestuff, dyestuff structure determines its dyeing performance and colour fastness.
3. Dyestuff particles are too coarse or not fully dissolved, which affects the penetration and diffusion of dyestuff into the internal fibres.
4. The dyeing process is unreasonable, such as drying method, drying temperature, baking temperature, baking time and reduction (fixing) temperature. Reduction (solid colour) time, soaping conditions, etc.
5. Disperse dyes do not remove the colour of cellulose fibres.
6. Reactive dyestuff in alkaline soaping. The ether bond formed between the dyestuff and the fibre is easily broken under alkaline and high temperature conditions, resulting in reduced fastness.
7. Finishing auxiliaries in the emulsifier in the shape of high temperature state so that the dyestuff to the surface of the fabric migration, resulting in a decrease in fastness.
8. Washing and soaping are not sufficient and there are residues of unsettled dyestuff on the fabric. Even after finishing with colour fixing agent treatment its effect is not satisfactory.
preventive measures
1. Pre-treatment fabric boiling to be transparent, wool effect to be uniform and consistent, strong water absorption, mercerization to be adequate, fabric with good chemical reactivity.
2. Do a good job in the application of various dyestuff performance testing, choose low directness, high rate of dyeing and colour fixation, easy to wash dyestuff coloring.
3. Disperse (reduction) dyestuff should strengthen the mixing (grinding) of the dyestuff, strictly control the fineness of the dyestuff and improve the diffusion performance of the dyeing solution.
4. Develop a reasonable dyeing process according to the performance of the dyestuff to improve the colour fixing effect of the dyestuff.
5. Disperse/activate one bath for dark colours, use soap detergent in one bath, disperse and activate two baths for extra dark colours.
6. Soft finishing using self-emulsifying block silicone oil to prevent the migration of dyes to the surface of the fabric; fixing to ensure the flatness of the fabric and shrinkage rate under the premise of reducing the fixing temperature as far as possible.
7. strengthen soaping, the most effective way is to use acidic soaping agent to thoroughly neutralize the alkali agent on the fabric, choose the appropriate colour fixing agent to improve the fastness of the fabric.
Wrinkled strips, pressed wrinkle marks
Causes
1. Polyester / cotton (man-made cotton) blended textile blank weft yarn setting effect is not consistent, in the printing and dyeing process of wet heat, high temperature state to produce different degrees of shrinkage.
2. Insufficient mechanical flatness, uneven pressure in various parts of the mill (mill wear, bearing wear, inconsistent air pressure at both ends) between the guide rollers are not parallel, etc. so that the fabric is subject to different tensions in the warp direction and produces wrinkles.
3. The distance between the fabric guide rollers, between the fabric guide rollers and the rollers is too large.
4. Hot air drying when the air volume is too large, the fabric does not run smoothly to produce wrinkles.
5. Polyester blended fabrics before the setting temperature is too low, the door width is too narrow, off the needle, etc.
6. Mercerization expansion is not enough width width is too narrow; cloth tongs mercerization machine cloth tongs wear deformation, off tongs, both sides of the chain wear inconsistent, etc.
7. Fabric weft slant is too large.
8. Bending roller wear or angle is not right expansion effect is poor; guide cloth roller bending deformation.
9. woolen fabric in the woolen before the fabric folding pile pressure fabric surface is not flat, woolen when the formation of pressure wrinkle marks; polyester blended textile dyeing before folding storage temperature is too high, too long to form pressure wrinkle marks.
10. tight fabric using folded pile steaming method, steaming when easy to produce pressure wrinkle marks.
preventive measures
1. Strengthen the maintenance of machinery and equipment, maintain mechanical flatness, even rolling pressure, and improve the adaptability of equipment varieties.
2. Weft shrinkage strip can be used when the blank fabric appears; dyeing before shaping to ensure that the temperature reaches above the dyeing temperature.
3. fabric grinding before the process of falling cloth using the way to play roll, to prevent pressure wrinkle print.
4. Close fabric using cold rolling pile before treatment process, can eliminate the pressure wrinkle print.
5. Strengthen the sizing machine, mercerizing machine track (chain) inspection, keep both sides of the chain length consistent, cloth tongs, needle sheet intact.
6. Fabric hot air pre-drying, according to the characteristics of the fabric reasonable adjustment of the circulating fan air volume, thin fabric to reduce the air volume.
7. Strictly control the weft slope of the fabric in each process, and the weft of the weft finishing device should not be wrinkled. There is no whole weft device machine into the cloth and out of the cloth weft degree, the difference is too big to find the cause and deal with in time.
In today’s rapidly changing printing and dyeing technology, printing and dyeing processing to adapt to the requirements of low-carbon environmental protection, relying on technological advances in the application of excellent performance of textile printing and dyeing additives to achieve low temperature, efficient short process processing methods to improve production efficiency and reduce production costs. Strengthen the quality management of enterprises, do a good job in the pre-production preparation of products, develop preventive measures for possible quality and technical problems, so as to achieve prevention-oriented. Strengthen the process quality control, ensure the success rate of the products at one time, eliminate the production of large quantities of rework and defective products, and improve the reputation of product quality and enterprise visibility.